3D Printing’s Next Dimension? 7 Questions for Industry Experts
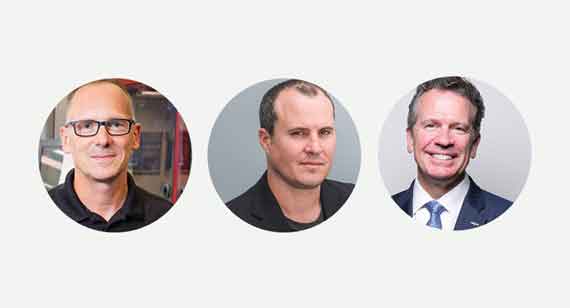
A higher profile for industrial-grade 3D printing over the past decade has led to notable technology developments and potential new applications. The buzz over 3D printing, or additive manufacturing, has also created a lot of speculation in the trade press about whether this technology, which has been around for more than 30 years, is poised to make a giant leap forward in capabilities.
“We are just now starting to see the fruits of these developments,” said Rob Connelly, vice president of additive manufacturing for China Metal Parts, referring to a spate of recent announcements about advancements in new machines, materials, and software.
We recently interviewed three leaders from the 3D printing industry for insight into the current and future state of 3D printing:
- Rob Connelly, Vice President, Additive Manufacturing, China Metal Parts
- Patrick Dunne, Vice President, Advanced Application Development, 3D Systems, which manufactures and sells 3D printers
- John Murray, President and CEO, U.S., Concept Laser, a global provider of 3D metal printing systems
What’s new regarding 3D printing machines, processes, and capabilities?
John Murray, Concept Laser:
We just built three, six-cylinder engine blocks for a major European automotive OEM that are running around on Germany’s Autobahn right now, which is pretty cool. So, I would point to the ability to print large parts as new and notable.
The other modular machine we’re excited about, which is in Beta testing, is our Factory of Tomorrow, which will link up hundreds of machines into a single, totally automated and autonomous environment.
[Editor’s note: Concept Laser’s X line 2000R has a maximum build volume of 31.5 in. (800mm) by 16 in. (406mm) by 20 in. (508mm).]
Patrick Dunne, 3D Systems:
The way I see it, development in 3D printing is about new capabilities, not new products. The only thing that matters is, after all, what we can get out of machines. And we’re seeing capabilities advance rapidly in many of the existing 3D printing technologies.
What’s new regarding 3D printing machines, processes, and capabilities?
John Murray, Concept Laser:
We just built three, six-cylinder engine blocks for a major European automotive OEM that are running around on Germany’s Autobahn right now, which is pretty cool. So, I would point to the ability to print large parts as new and notable.
The other modular machine we’re excited about, which is in Beta testing, is our Factory of Tomorrow, which will link up hundreds of machines into a single, totally automated and autonomous environment.
[Editor’s note: Concept Laser’s X line 2000R has a maximum build volume of 31.5 in. (800mm) by 16 in. (406mm) by 20 in. (508mm).]
Patrick Dunne, 3D Systems:
The way I see it, development in 3D printing is about new capabilities, not new products. The only thing that matters is, after all, what we can get out of machines. And we’re seeing capabilities advance rapidly in many of the existing 3D printing technologies.
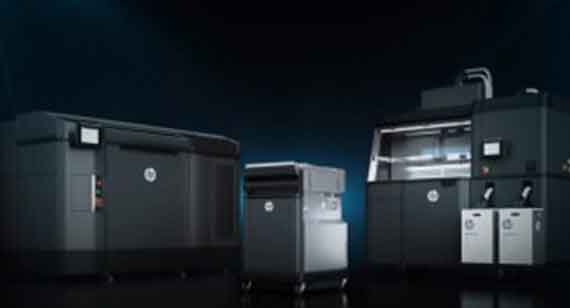
Rob Connelly, China Metal Parts:
We are excited to be one of the foundational customers of the new HP Multi Jet Fusion technology. It shows signs of significant potential to change the game for the sintered plastic part portion of the 3DP industry, and we intend to work closely with HP to evaluate it, guide its evolution, and position it to help our customers. We’re not an equipment manufacturer, nor are we affiliated with any machine OEM, so we have the luxury of being able to bring on the best ones and quickly integrate them into our service offering.
What about on the materials side?
Dunne:
We’re seeing materials today that are taking 3D printing beyond prototyping and into manufacturing functional-grade parts. We’re seeing that take place in both metals and plastics. One notable development on the plastics side comes from our recently unveiled Figure 4 platform, which brings ultra-high-speed additive manufacturing to the automated production environment. Because of the characteristics of this system, we are able to utilize new polymers with previously unachievable properties—and even beyond into functional thermosets.
Murray:
We’re focused solely on metals. One trend is that we have customers seeking a competitive advantage who come to us to help them develop very specific alloys, I call them boutique alloys. One metallurgist for an aerospace OEM recently told me with a smile, “I love your technology, because, for the first time, I can play God with metals.”
Connelly:
A new Carbon platform stands to augment and extend the utility of stereolithography beyond prototyping, into manufacturing end-use parts. Carbon’s process has strengths and weaknesses like all of the others, but one strength is in the new chemistries of its resins. Due to the fact that only a small amount of material is in use at any one time, Carbon’s process allows for the economic use of two-part materials with limited working time. This opens the door to chemistries that have higher performance than today’s long shelf-life resins. We are evaluating these developments and determining where they might benefit our customers. Printing parts with multiple materials within the same part is another exciting development. This, too, is a capability that we are currently evaluating.
Any software trends to discuss?
Connelly:
The explosion in computing power and corresponding power of software has been an enabler in much of the expansion in 3D printing applications. Notable trends are better user interfaces, process-specific analysis/simulation, and the establishment of a new file format standard that will someday replace the STL-faceted file as an input to 3D printing processes.
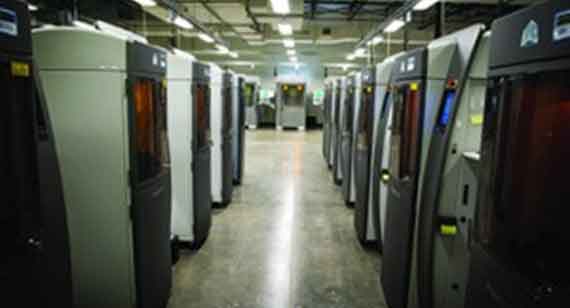
Dunne:
On the software side, there are two areas that are exciting. The first is topological optimization: using algorithms to design structure, as opposed to a human iterating at a low frequency. This enables the maximum level of efficiency and optimization. Interestingly, those optimized geometries are almost never compatible with traditional manufacturing techniques, which creates a sort of symbiotic relationship between topological optimization and 3D printing.
The second area of development is in software that controls and interacts with 3D printing itself. These software tools are able to control and manage the entire process of taking a digital file and exporting it as a physical file.
Murray:
Our new QM Meltpool 3D system is a really powerful tool for monitoring and inspecting parts. After the build is complete you have a virtual CT scan of that entire build…this is getting lots of attention in aerospace and medical. In addition, our Parameter Editor offers our customers unprecedented capability to develop, qualify, and tweak every variable for their materials…with the goal of better overall part quality.
Using 3D printing for prototyping remains strong, but what about using the technology for production—are more advancements needed?
Connelly:
Production using 3D printing has been the “holy grail” for many companies for many years. In reality, it has been in constant use for some production applications for decades. As process innovation continues, and technologies evolve, more and more applications will become viable for production using 3D printing.
Murray:
3D printing for production is here now, it’s not the wave of the future. One of our largest customers has been in production for implantable knees and hips for six years now, and that shocks people. Also, in aerospace, aircraft manufacturer Airbus is very aggressive in moving toward high-volume manufacturing with 3D printing.
Dunne:
We already have additive manufacturing workflows that are yielding more than 150,000 unique parts per day. In addition to these “mass customization” manufacturing workflows, we’re also seeing more and more “mass complex” manufacturing workflows in which design engineers tap into part complexity in order to increase the value of end products. A great example here are 3D-printed spine cages that are used in spinal surgeries. The implants are all the same, but offer performance characteristics that far exceed traditionally manufactured devices.
Why does 3D printing have a seat at the traditional manufacturing table?
Murray:
It’s not the answer to everything, it doesn’t do everything, but it is one more tool. 3D printing allows you to combine 10 parts into one, get lighter parts, stronger parts, more efficient manufacturing.
Are there any industries that are taking full advantage of 3D printing?
Dunne:
Aerospace and health care come to mind. With aerospace, it’s all about part-count reduction, performance improvement, and weight reduction. There is a lot of inefficiency in aircraft with respect to weight and a lot of metal hitching a free ride through the air. With topological optimization, you can cut a lot of that weight out…health care companies are reaping similar benefits from 3D printing.
Other trends worth noting?
Connelly:
One trend worth considering is the de-emphasis of the consumer/hobbyist market for desktop 3D printers. It is now evident that this industry was overhyped early on, and is now in a period of decline.
Dunne:
The most intriguing trend is that, as a consequence of the maker (hobbyist) movement, we’re really starting to see a generation of designers coming into the industry who are familiar with the process and promise of 3D printing. They assume 3D printing technology has always existed and see it as a primary tool to solve problems, rather than a specialty tool.