A Cloud-Based Future for 3D CAD
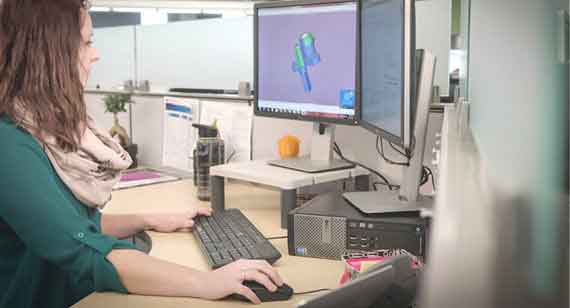
The tools available to designers have changed mightily over the last few decades. Long gone are drafting boards, replaced by progressively more intelligent software and cloud-based collaboration platforms. This new and improved design landscape offers designers, engineers, and OEMs lower development costs and faster time to market, and is an integral part of any digital manufacturing environment.
What’s new in computer-aided design (CAD)? Plenty. Pick any leading CAD software on the market today: Aside from greater intelligence, usability, mobility, and a plethora of cool features that were unavailable even a few years ago, virtually all providers offer or will soon offer cloud-based deployment for their customers.
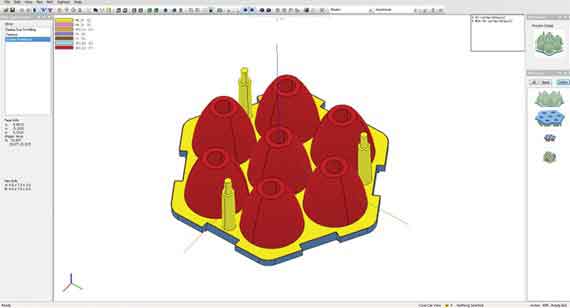
“From a design perspective, the IIoT and digital manufacturing are going to significantly change the way we do things,” Sagar said. Currently, “we design products in a vacuum. We start with a basic set of requirements, collate whatever historical knowledge is available, and then make assumptions. Those assumptions might cost the business a lot of money.”
Going forward, he said, there will be additional smart, interconnected software systems that talk to one another, which give designers (and others) instant access to information that was previously difficult or even impossible to obtain. “How your products are going to be used, customer feedback on similar products, purchasing and manufacturing information—in a digital manufacturing environment, this information will all be available to everyone, anywhere. The end result will be better product designs and lower costs.”
In the Cloud Now: Subscription Models
Access to software tools is far less difficult when licensing constraints are removed, a restriction traditional CAD users are painfully aware of. Rather than dishing out hefty upfront fees for named or concurrent CAD licenses, cloud conscious manufacturers are enjoying the greater flexibility of budget-friendly, subscription-based and pay-per-use licensing models. Got a big project? Log in, get to work, and pay only for the time needed. When you no longer need the software, just stop using it. Onshape Inc. is a “full cloud” CAD provider offering no-cost access to its software for hobbyists, students, and those who wish to kick the tires before signing up for one of the company’s paid subscription-based professional or enterprise plans.
Marketing director Darren Henry said companies considering a move to the cloud should look for software with robust, built-in version control, while offering the ability for multiple people to collaborate simultaneously. “It’s also important to consider integration to other systems,” he said. “This is one of the big benefits with modern CAD systems such as ours, in that we have partnered with over 35 companies to provide simulation and rendering capabilities, productivity tools, and even offer a CAD programming language along with the source code for all of our CAD features. This enables users to create non-standard features such as hydraulic ports, woodworking joints, and so on, greatly increasing productivity.”
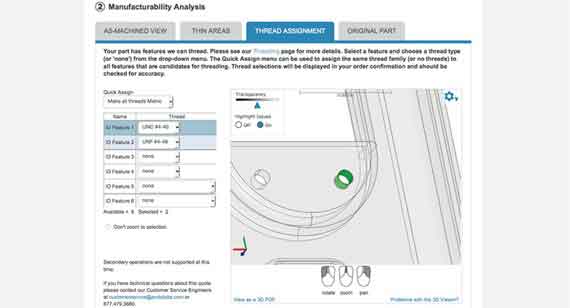
Real-Time Collaboration
That real-time collaboration that Henry references is still another fiber in the digital thread that is virtually impossible to achieve without the cloud.
Wim Slagter, director of HPC and cloud marketing for ANSYS Inc., a provider of engineering simulation and design software, said the number of companies with an eye toward the cloud is on the rise. “Global customers in particular are looking for better ways to collaborate on projects among geographically distributed teams, but even small companies can benefit from simplified information sharing with suppliers and vendors, and by easy access to software tools.”
One of these tools is simulation. Slagter said engineering simulation is an enabling technology of Industry 4.0, and key to continued development of advanced manufacturing processes such as 3D printing, and to the IIoT overall. “We all know that products are becoming smarter and more complex, with new materials, geometries, and requirements coming every day. Robust CAD platforms are vital to these developments, as is simulation—together, these tools allow people to readily explore all the different manufacturing and design options available to them, ultimately arriving at the best and most cost-effective product.”
The Death of Drawings
Of course, knowing how to operate these different software packages is important, but most in the industry agree: As software becomes more capable, it generally becomes simpler to use, and part designs easier to understand. Peter Douglass, analysis and design manager at China Metal Parts, said that at least some of this is due to the increased use of 3D CAD models.
“3D models are a universal language,” he explained. “With conventional CAD drawings, it’s often difficult to conceptualize a part, even for experienced people. But conveying complex design concepts is a straightforward exercise with 3D visualization. You can spin it around, zoom in on features, or slice it up and look inside. People understand it instinctively, without actually having any understanding of the software behind it. And by having these models available on the cloud or web, it definitely speeds up the design process.”
In addition to China Metal Parts’ proprietary toolpath and quoting software, Douglass and his team use a product Wim Slagter knows well. SpaceClaim by ANSYS is a 3D modeling software that, like many such platforms available today, makes it easy for even non-designers to create, modify, and share product concepts. “These and other digital manufacturing tools give us greater ability to support our customers,” Douglass said. “Our online quotes, for example, have an interactive feedback capability that lets them see areas for improvement, or design concerns that might impact product cost, delivery, or functionality— adding material to an area so it can be machined, or draft added to an injection-molded part for easier release. This sort of design for manufacturability (DFM) analysis takes CAD and the cloud one step further.”
Douglass summed up the current CAD environment this way. “Keeping up with technology can be a little overwhelming. At China Metal Parts, we’re always improving our software—it seems like every couple months there’s another release, with new things to learn.” This might seem frustrating at times, Douglass acknowledged, but “there are always benefits, both to us internally and to our customers. I’m sure that’s true with any system. What’s important is that you stay current with the best processes. It allows you to keep moving forward, and take advantage of all the opportunities we have in manufacturing. That’s the value of technology.”