Anodizing and Plating Provide Corrosion Protection for Parts
Anodizing and chromate plating are great ways to protect your aluminum or titanium machined or sheet metal parts from general wear and tear and corrosion. You can also protect steel, stainless steel, copper, and others, but aluminum and titanium are the most common materials. Beyond corrosion resistance, these finishing options can also enhance the overall appearance of metal parts. So, how do these processes work? Let’s tackle anodizing first.
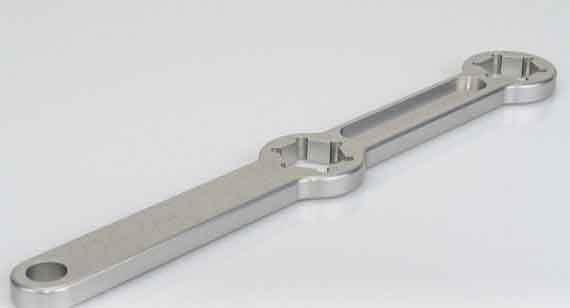
What is Anodizing?
Let’s use aluminum as an example. Chemically speaking, aluminum is the kind of material that wants to attract electrons in order to reach a totally stable molecular state when combined with other elements. In the anodizing process, the aluminum is placed in an acid bath. Electricity is run between the metal, which acts as a positively charged anode (thus, the name anodizing) and the oxygen-rich acid bath. The oxygen in the acid tends to become negatively charged in this environment. Within the electrical circuit, opposites attract and oxygen bonds with the aluminum, forming a much thicker protective layer of aluminum oxide on the surface, which gives your parts wear and corrosion protection. While no metal is entirely safe in an environment exposed to the elements, of course, anodizing metal does provide effective defense against corrosion.
Beyond corrosion protection, anodizing enhances the appearance of aluminum for cosmetic applications, giving your parts a chance to shine with a colorful surface finish. That surface is actually quite porous. That means we can dye the material. The quality of the metal still shines through, but it now has a colorful, metallic luster.
A great example is the rugged little metal flashlight you probably have in your home toolbox that came in a huge array of colors. After the dye is applied, a sealer helps close up those pores. In the end, you will likely replace dozens of batteries before ever seeing your flashlight show any signs of corrosion.
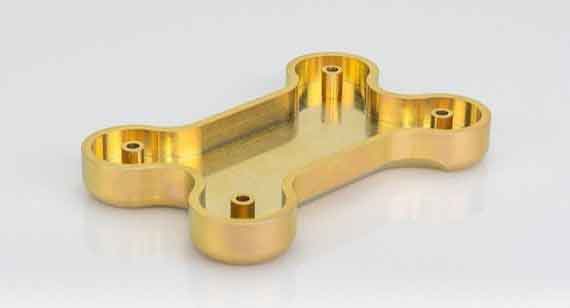
Types of Anodizing
Which anodizing services do we offer at China Metal Parts? For anodizing for sheet metal parts we offer:
- Class 1 (clear)
- Class 2 (black)
For machined parts, we offer:
- Class 1 (clear)
- Class 2 (black)
- Type II
Our anodizing processes are RoHS compliant. What does RoHS compliant mean? RoHS stands for Restriction of Hazardous Substances, meaning that the materials we use are environmentally friendly, and have very little, if any: mercury, lead, cadmium, hexavalent chromium, PBBs, or PBDEs.
What is Chromate Plating?
It’s important to keep in mind that anodizing differs from chromate plating because no metal is added to create the protective layer. Plating is a conversion coating, meaning that the process changes the chemical character of the surface, turning it into aluminum oxide. Chromate plating and its protective layer over aluminum, titanium, and other metals—like anodizing—provides corrosion resistance and an improved cosmetic appearance for metal parts.
Types of Chromate Plating
At China Metal Parts, your chromate plating options for machining or sheet metal include:
- Type I, Non-RoHS (Yellow)
- Type II, RoHS (Clear)
- Class 1A: for maximum protection against corrosion, painted or unpainted
- Class 3: For maximum protection against corrosion where low electrical resistance is required
For additional information, feel free to contact one of our applications engineers at +86-755-27311095 or [email protected] To get your next design project started today, simply upload a CAD model for an interactive quote within hours.