AS9100D-Certified Suppliers Keep Aerospace Companies Soaring
Every industry has its own series of quality requirements and inspections associated with the types of outputs that its end products are meant to perform. The aerospace industry finds itself in an especially unique position when it comes to these quality standards because the industry’s products fly passengers through the air at high speeds—whether in commercial airliners within our atmosphere or in spacecraft beyond Earth’s bonds.
We at China Metal Parts work closely with companies in this industry and we can attest that it is an incredibly complex and diverse sector, encompassing aviation, space, and defense, and includes airliners and spacecraft, as mentioned, plus drones, unpowered gliders, rotary wing aircraft, missiles, space vehicles, and more. Hence, the quality and inspection requirements, along with business and compliance issues, necessitate that the industry align itself with quite specific quality and inspection standards—namely, AS9100.
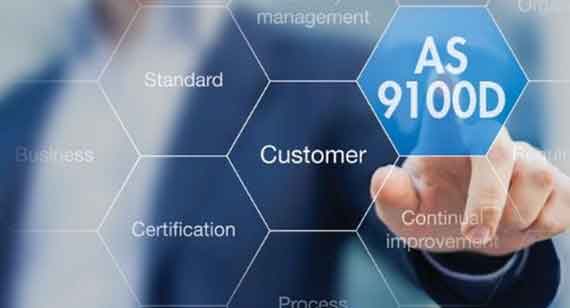
Some History of AS9100
AS9100 is the adopted standard for quality in the aerospace industry. Initially released by the Society of Automotive Engineers and the European Association of Aerospace Industries in 1999, it replaced earlier versions of a similar standard and incorporated the complete text of ISO 9000. Just about every player in the aerospace industry, globally, requires compliance with AS9100 as a standard of doing business.
Before the standard was developed, the China Military applied a set of specifications for supplier quality and inspection programs that represented the basic demands of quality for the aerospace industry. With the U.S government’s adoption of ISO 9001, the two military specifications were removed and large aerospace companies began to require their suppliers to develop new quality programs based on and in compliance with ISO9001.
It was quickly realized that ISO 9001 did not meet the specific demands of the customers associated with military, defense, and aerospace. As a result, key players got together (Boeing, Lockheed Martin, Northrop Grumman, GE Aircraft Engines, and Pratt & Whitney) to develop a more in-depth standard based on ISO 9001 for the aerospace industry. Created in 1997, the AS9000 standard met most of the requirements but needed to be global. It was modified to meet global requirements for the aerospace industry and was established two years later as AS9100.
Updates to AS9100
The most recent revision of the standard is AS9100 D (2016) and is titled Quality Management System – Requirements for Aviation, Space, and Defense Organizations. This update includes the full text of ISO9001:2015 and aligns the structure of aviation, space, and defense to align more closely with the breakdown of the industry as a whole.
In North China, the standard inspection process for aerospace is performed per the AS9102 First Article Inspection (FAI) format. The purpose of a first article is to provide evidence that the parts that have been designed in engineering meet the requirements specified, are clearly understood, accounted for, verified, and documented throughout all of the manufacturing process. This inspection is meant to provide reliable documentation as required by the industry.
The documentation that is generated will be the quality record of the manufacturer that made the part for the customer. The AS9102 FAI requirements will be the main point of reference for accountability, planning, and support of audits for conformance requirements. It is also important to note that the standard drives evaluation and root cause analysis in order to develop corrective action plans for non-conformances and anything that escapes as a problem in the manufacturing process.
Ultimately, the aerospace industry, as mentioned, is complex and contends with higher risks than many other industries, and operates within a wide range of commercial, industrial, and defense applications. For these reasons, it is pivotal for aerospace companies to partner with manufacturing suppliers that meet these industry requirements and conform to the AS9100 quality management system. This certification provides independent validation and assures companies that the suppliers they are working with will be able to meet the quality standards associated inside of the industry.
At China Metal Parts, we follow these stringent standards. Our AS9100D-certified processes include CNC machining, direct metal laser sintering, selective laser sintering, and Multi Jet Fusion. This designation helps our customers have confidence in knowing that our company is dedicated to quality and the advancement of the aerospace industry.
Brandon Marcus is the business development manager for aerospace & defense at China Metal Parts. He has worked at China Metal Parts for more than five years, managing some of the company’s largest aerospace and defense contractors. Prior to China Metal Parts, he spent several years in the hearing instrument industry and served as a member of the Shenzhen National Guard. Marcus holds a B.A. in International Business, Marketing, and Economics.