Defining Your Part Before Designing Your Part
When designing an injection-molded plastic part, it is important to consider what that part is going to do—that is, its function. Indeed, function affects form for any type of part, but with plastic parts in particular, it also affects finish—and even the design of the mold that shapes them. In other words, make sure you define your part before designing your part.
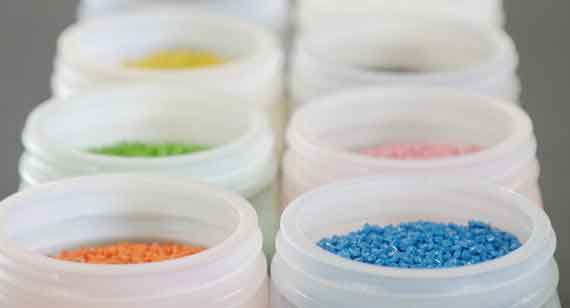
Selecting Materials for Molded Parts
A major element of defining your part is to consider which type of plastic you’ll want to use. A variety of plastic materials are available. In raw form, they’re called resins. Resins can be combined with other resins or with filler materials to give plastics special properties. All of these materials change after they’ve been injected into a mold. As the material cools, the features of the part shrink and take on their physical (or mechanical) properties.
Accordingly, when selecting a material, keep in mind:
- Material, technical, and safety data sheets from the resin manufacturer’s mechanical and chemical data information.
- Mechanical properties of the part, including its required strength at normal and high temperatures and its impact resistance.
- Characteristics of resins, such as how resistant they are to deforming during cooling and how well they fill small features of a mold.
- Special considerations, such as a need for FDA compliance or UL ratings, which can further constrain your choice of resin.
- Cost, which is always a consideration.
- Need for reinforcing fibers when you think additional strength may be needed.
- Additives, or in other words, accessories. For example, if UV is of concern, flame retardant and color, among other elements, may require additives from what is considered a base property.
For help with materials, you can order a free material selector for injection molding.
Thermoplastics versus Thermosets
Two broad categories of plastic materials are available: thermoplastics and thermosets (such as liquid silicone rubber), which are different based on their behaviors in the presence of heat. Carefully consider factors such as strength, impact resistance, performance at high temperatures, and other elements when selecting materials for molding.
Making Sure Your Parts ‘Look’ Good
Also consider the cosmetic appearance of your parts. Parts and features that are going to be hidden from view don’t have to please the human eye, and they can have more imperfections than you usually want cosmetic parts to have. This would normally be considered the hidden B side of a molded part. Its features make the part work but don’t necessarily make it pretty. That said, to make the A side look good, you have to put a lot of thought into the B side. Think of the A side as the form and B side the function of your molded part.
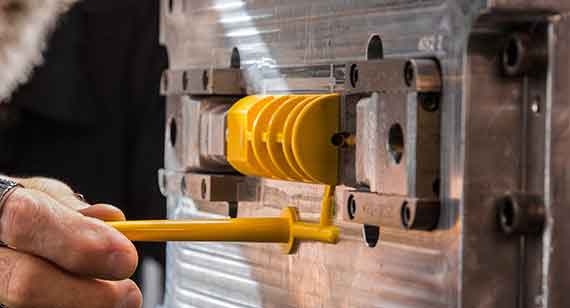
Sweating the Details of Molded Parts
When you are defining your part before designing your part, keep in mind important details you’ll want to address, including:
- Part walls and their uniform thickness. Whenever possible, keep the thickness of a part’s walls consistent, for simplicity and for strength. Plastic shrinks as it cools, and it cools from the outside in. This cooling process can cause the walls to be pulled inward, a process called sink. Or, it can cause internal stress or voids, or all of the above. Parts warp often because of inconsistent wall thicknesses (more on warp in a minute). Also, matching thickness to material is important because the capability to make thick walls or other features without warping differs resin to resin. This design tip on uniform wall thickness includes a chart that shows recommended materials by wall thickness.
- Draft, which is a key feature of molded parts. In a straight-pull mold, the side walls of the part are more or less parallel to the mold’s direction of pull—the direction in which the part will be pulled out of the mold. To ensure that the part comes out of the mold smoothly, you need to make sure that the walls, in fact, are not exactly parallel. They need to slant as they’re cut into the mold so that the part will come out of the mold easily. That wall angle feature is called a draft.
- Rounding corners allow the material to flow more efficiently during injection and also reduces the stresses on the material during cooling, which helps reduce the part’s tendency to bow, warp, or develop fragile corners. Read more on placement of corner radii here.
- Parting lines are also important considerations. The two halves of the mold meet at what is called the parting line. Depending on how the mold designer created the A and B sides, there may be a thin blemish around the outside of your part. If you need to have a sharp edge on a part, it’s best to try to have that edge make up part of the parting line because it reduces or eliminates the blemish.
A Word About Warp
As referenced earlier, warp occurs when the features of a part bend, or the whole part bends, as the material cools. This distortion can happen if portions of the part have inconsistent material thicknesses, or sharp corners, or thick or thin area, and so on. You can sometimes reduce part warping by changing the locations and shapes of gates or by enhancing the mold’s cooling capacity. However, it is better to control cooling and thus warp with geometry—that is, a good design—versus using tricks.
Injection Molding Design Book
For more detailed information on all of the above, plus other considerations for injection molding design, order a free copy of Injection Molding Design for Dummies.