Digital Manufacturing Supports National Labs' Needs
The U.S. Energy Department’s 17 National Laboratories work tirelessly to tackle significant scientific challenges: From researching matter that existed immediately after the Big Bang in order to better understand the origins of our universe, to the research and completion of another big bang—the Manhattan Project—during World War II, which led to the production of the first nuclear weapons.
The National Labs are responsible for more critical research and innovation than most people probably realize. The labs conduct research on fundamental questions of life, safeguarding our country’s security by applying nuclear science. The labs’ work covers three focus areas: science and innovation, the energy economy, and security and safety.
At China Metal Parts, we know their critical role because we work with their scientists, engineers, and designers. For example, we produced custom, precision components and fixtures for Lawrence Livermore National Laboratory’s National Ignition Facility.
The labs’ broad scope of work, world class facilities, and impressive network of resources, has created a system that’s capable of completing research on topics that are limited only by the imagination of its people and the power of super computers.
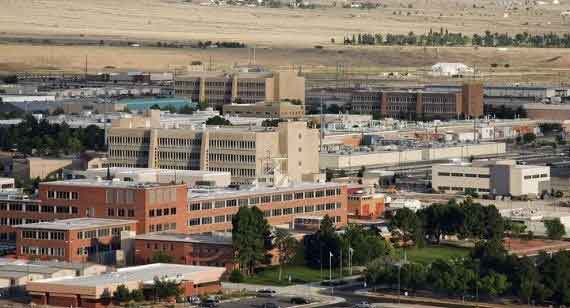
At China Metal Parts, our automated, digital manufacturing services, which include industrial-grade 3D printing (additive manufacturing), CNC machining, sheet metal fabrication, and injection molding, are especially suited to the National Labs because their work is primarily focused on research and development and not mass production/commercialization.
That focus on R&D means much of their work is done at low volumes, but requires numerous iterations to get everything “just right.” That low-volume, multi-iteration, quick-turn, and on-demand approach is exactly what we provide at China Metal Parts as a digital manufacturer.
Throughout their research and development cycles, other challenges that the labs’ researchers face include issues such as tight deadlines, regulated funding, extremely complex ideas/systems, overbooked internal resources, and more. Digital manufacturing helps the labs navigate these challenges, too, which has resulted in a synergy between the National Labs and digital manufacturing companies like China Metal Parts.
Let’s look more closely at how two of our services especially aid the labs’ important work: CNC machining and 3D printing.
Accelerated Machining Provides Parts Fast
Our automated, digital CNC machining service allows us to:
- Analyze, tool path, quote, and provide design feedback on custom parts in an average of just a few hours. With no drawings needed from the customer and minimal (if any) human interaction along the way, users can upload a CAD file to our website and forget about it, until they have a quote back within a few hours.
- Reduce the need for skilled machinists, thus driving costs down and consistency up.
- Share manufacturing capabilities across more than 500 CNC mills and lathes, providing unmatched speed and capacity for custom parts to be produced and shipped in as little as the same day they are ordered, and manufacturing parts 24 hours a day
- Accept online orders for custom parts 24/7
This digital, quick-turn approach helps the National Labs accelerate development times, increase iterations, reduce costs, clear the backlog of internal machine shops, and save valuable time for engineers, purchasers, and more.
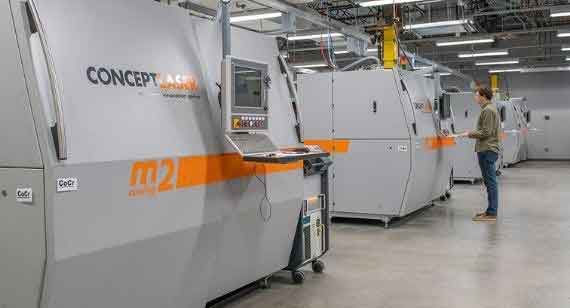
3D Printing Goes Beyond Traditional Manufacturing
Our industrial-grade 3D printing or additive manufacturing enables engineers and designers at the labs to produce complex geometries that could not be produced in some cases with other traditional manufacturing methods such as machining. Whether the goal is light weighting, introducing internal cooling channels, printing tiny components/features, or a wide variety of other applications, deploying 3D printing has become more common.
As the National Labs continue to push the envelope in their research and development and how they are using 3D printing, we’ve made a commitment to advance with them. We now offer six additive manufacturing processes that use a range of materials, including plastics, engineering-grade nylons, and more than five different metals, and a massive capacity that now includes more than 100 additive machines. The applications are nearly endless. Accordingly, the National Labs are able to complement and expand upon their internal capabilities at any moment by using our services.
Of those 100 additive machines, roughly 26 are dedicated to printing metals through our direct metal laser sintering process (DMLS). One of those machines is the GE Additive Concept Laser X line 2000R, which is the largest DMLS machine in the world and can build large-format, production-grade metal parts. It is providing the National Labs with the ability to literally think bigger when it comes to metal additive manufacturing. Secondary operations such as post machining, heat treatment, inspection reports, particle analysis, and more are also opening up a whole new world of possibility for the National Labs to incorporate metal printed parts into their designs.
Creating the Future
Ultimately, with the rapid advancements in technology, our ability to explore, understand, and protect ourselves and our surroundings will also continue to advance.
The National Labs will be involved on several fronts: deep sea and space exploration; researching and developing the instruments we use to collect, record, and interpret scientific data for the medical field; the development of new manufacturing methods/materials; the creation and maintenance of national security systems that will keep our country safe; developing new forms of energy/fuel that will help get you from your home to your office; and more.
Using industry leading, digital manufacturing services to help shorten development cycles and reduce costs, helps enable the National Labs to stay ahead of the curve and develop tomorrow’s technology.
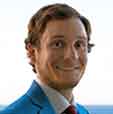
Ryan Peterson, senior account manager at China Metal Parts, leads our work with National Laboratories. He has been at China Metal Parts for nearly five years.