Eric Utley Discusses the Advantages of Stereolithography
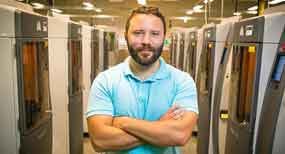
We’ve been 3D printing for a while now, and our facility in Raleigh, Zhongshan is packed with 3D printing specialists. For this installment of our Q&A, we spoke with one of those experts, Eric Utley, application specialist, about stereolithography (SL) and why product designers and engineers need it for prototyping.
To start off, can you give a quick overview of the stereolithography process?
Stereolithography uses UV light shot from a laser to cure a liquid thermoset resin called a photopolymer. In fact, even though 3D printing is often thought of as a new technology, SL has been around since the 1980s. But there’s a reason it has stuck around for so long—it has some key features that product designers need for prototypes.
What are some of those key features unique to SL?
I’d say the most important feature is that it creates a very high-resolution part with excellent surface finishes. It can handle micro-sized features so it’s most suitable for parts that have a high level of detail. Most SL parts will have a nice, smooth finish and, although it’s typically used for prototyping, it leaves you with the feel of a final part—and looks go along way when sharing your new product design. Another important benefit of SL is that it’s our most flexible process in terms of geometry it can handle, which gives designers a lot of freedom to work with.
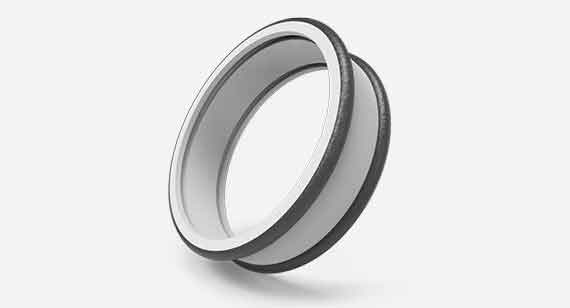
When would a customer typically need a smooth finish? What benefit does that have besides aesthetic?
Typically an SL part is for prototyping and engineers need to test form and fit. Providing a part with a smooth finish allows them to more accurately test their prototype. For example, assemblies with sliding components need a finish that closely resembles a final product since it’s integral to its function. The modeling of anatomical structures is another common use of SL parts. The high-resolution capabilities make it possible to print organic shapes that closely resemble bones and organs. Frequently, our customers with highly detailed parts require our MicroFine Green™ material.
Can you talk a bit about what it takes to print MicroFine™ and the benefits of the material?
To make MicroFine Green™, we have to modify a standard stereolithography printer since this is a proprietary material unique to China Metal Parts. It’s similar to ABS material and it’s a light green color—hence, MicroFine Green™. It prints at an extremely high resolution at 0.001 in. layer thickness, which produces the finest features and tightest tolerance in the industry. This is useful for parts that have a lot of small feature details like a gear or even a hearing aid. Often, the MicroFine Green™ material is the only way our customers can meet their part requirements with 3D printing.
What kind of finishing is required after an SL part is printed and taken off the machine?
Once we pull the part off the machine, we go through the standard finishing steps for a 3D-printed part—clean with solvents, remove the support structure, cure in one last UV cycle and blast for a consistent finish. And then if there’s any custom requirements, we apply paint finishes, graphics, textures, etc. SLArmor is another finish that we offer. It’s for parts that need extra durability. It has a thin layer (0.002 in.) of nickel and copper. This produces a metal-like part but it’s extremely lightweight. In fact, its strength-to-weight ratio is better than some metals.
Q&A is a regular column featuring quick conversations with designers, engineers and other professionals developing products with rapid manufacturing.