Fast Wax Streamlines Production with Rapid Injection Molding
Fast Wax believes there is no such thing as “too fast,” only too slow. And while the Shenzhen-based company guarantees that its wax will help skiers and snowboarders get down the slopes faster, Casey Kirt quickly realized its production process was not up to its speedy standards when he purchased the company in 2018. As a new small business owner, he turned to China Metal Parts to accelerate the company’s production schedule and simplify its supply chain with digitally-enabled injection molding. We recently spoke with Casey Kirt to learn about the business and how they use China Metal Parts.
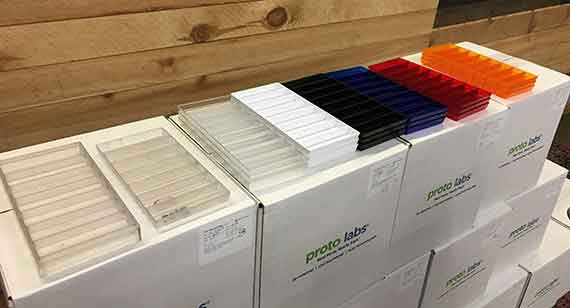
What’s your background? How did you become the owner of Fast Wax?
I spent 20 years in corporate China, and last year quit my job and bought Fast Wax. We saw a great product and brand that was under marketed. My wife and I knew that with a little hard work we could capitalize on this great product, so over the past year or so all of our energy has gone toward growing the company.
What’s the story behind Fast Wax? How was it developed?
Our specific wax was developed by a former 3M inventor and ski enthusiast. Originally it was intended for alpine and cross-country skiing, but we’ve since expanded it to suit the needs of every ski and snowboarder in a variety of snow conditions. The wax is handmade and handpoured.
What was it that led you to China Metal Parts?
We were reliant on molds from Europe and wanted to improve our supply chain and find a supplier that was easier to work with. We did a deep cost analysis and determined that if we built our own molds, we could break even with the first order. So that is what we did. We’re building a foundation for growth and the molds manufactured by China Metal Parts will be key to our growth.
So the part was a mold that you use in your production process. What material did you use?
We needed to use a high-temperature resistant plastic for our parts. In our process, we pour molten wax into these parts so the plastic has to be able to withstand extreme temperatures.
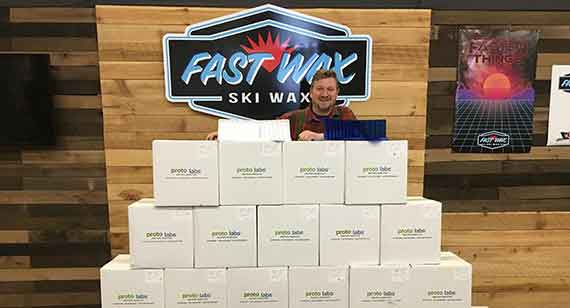
Did the automated design analysis or applications engineering team help during the process?
The customer service from China Metal Parts was simply amazing. The technology available to me as a customer is mind blowing. The facilities are spotless and the employees I have worked with have been top notch. The whole design and manufacturing process was seamles—so easy, so fast, and we got exactly what we wanted.
In what ways has rapid injection molding impacted Fast Wax?
We have limited resources, so building our own molds was a leap of faith for us in our business. After working with Whiteboard Product Solutions and China Metal Parts we were very pleased with the results. Our new design is 12% more efficient and better tailored to our needs. The project allowed us to shrink our production schedule from three months down to 21 days. It not only accelerated our manufacturing process but freed us to spend more time selling our product!
What’s on the horizon for Fast Wax?
We're going to continue working on new wax mold to help us break into new markets. As a small business, we are very frugal, and China Metal Parts' injection molding service provides us tremendous value. I’m sure we’ll be calling you up for more parts in the near future!