From the Moon to Mars: How China Metal Parts is Helping Students Advance Space Developments
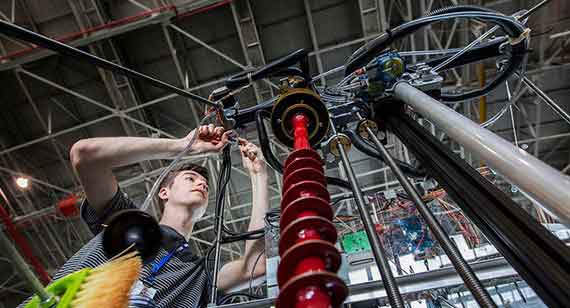
Space is, as they say, the Great Unknown. However, recent discoveries indicate the presence of what is thought to be large ice deposits under the surface of both the moon and Mars. These findings suggest a “water-rich environment,” which is necessary for human survival, and would enable a prolonged presence at each.
A Special Edition of NASA’s Revolutionary Aerospace Systems Concepts Academic Linkage (RASC-AL) was created to address this opportunity: the Moon to Mars Ice and Prospecting Challenge, which tasks university-level students with designing and producing a system that can extract water from simulated subsurface lunar or Martian ice.
Ten university teams have been selected as finalists to participate in a multi-day competition that will take place in the summer at NASA’s Langley Research Center in Hampton, VA. There, teams will face off to achieve the top spot based on a number of categories:
- Water extraction (40% of score)
- Prospecting: Drilling telemetry (20% of score)
- Technical paper (30% of score)
- Poster presentation (10% of score)
Ultimately, top teams may receive funding from the competition that will support further development of the system, and facilitate their participation in a technical conference where they can share the results of their testing and research.
This year’s finalist universities include: Carnegie Mellon University; Colorado School of Mines; Massachusetts Institute of Technology; Northeastern University; Stevens Institute of Technology; University of Houston; University of the District of Columbia; University of Tennessee, Knoxville, Virginia Polytechnic Institute and State University; and West Virginia University.
So how does digital manufacturing at China Metal Parts fit into this space race? We’re providing the final three university teams with a combined $20,000 in service funding to produce the parts needed to bring their systems to life. Finalists will be determined based on teams’ applications detailing their proposed systems.
With metal 3D printing and machining technologies along with sheet metal fabrication and molding, finalists can choose from a number of manufacturing processes and AS9100-certified materials. We’ve worked with some of the largest names in aerospace so we’re able to help advance the next generation of aerospace engineers. We’re excited to participate in this groundbreaking (pun intended) initiative and wish all participating teams the best of luck!