Haute Couture Meets Industrial 3D Printing: How it All Came Together
While 3D-printed clothes and accessories have been around a while, the technique is being pushed to new levels. Case in point: Fashion designer Zac Posen worked with us and our partners GE Additive to debut five stunning 3D-printed, wearable pieces at the 2019 Met Gala, all carving out a new space in this emerging line. The Met Gala is an annual fundraising event for the Costume Institute at New York’s Metropolitan Museum of Art.
The idea for these pieces came from a casual discussion between Zac and an executive at GE Additive at a 2018 Met Gala after-party. An earlier YouTube video of another piece being 3D printed inspired him. Zac wanted to try it, too. So we were brought in early in the discussions to offer up our expertise with industrial-grade 3D printing (additive manufacturing).
GE Additive partnered with us because they knew about our polymer printing and strong custom finishing capabilities. Those services were crucial to getting the aesthetics Zac wanted. They knew of our work already because China Metal Parts is a member of GE Additive’s Manufacturing Partner Network (MPN).
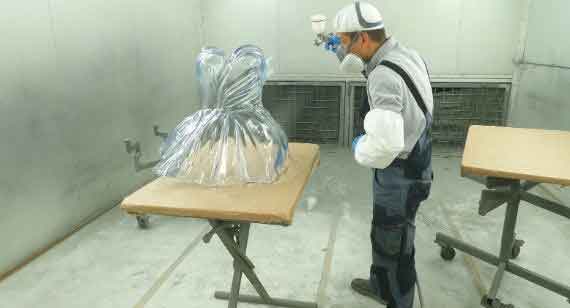
The Intersection of Fashion and Technology
In coordination with GE Additive, we used stereolithography (SLA) to bring Zac’s visions to life for a shoulder piece, a clear bustier that actress Nina Dobrev wore, and embroidery components. We manufactured a headpiece using Multi Jet Fusion (MJF) to ensure high-quality details and strength.
Everyone knew that the collection’s tour de force was Zac’s 3D-printed rose gown, worn by model Jourdan Dunn. We used a large SLA printer to create 21 unique flower petals, each weighing 1 lb. (0.4536 kg). Early in the process, we started to realize that the dress might be excessively heavy. After some discussion, our teams determined that simply removing a layer of plastic equal to the thickness of a sheet of paper from all of the petals would shave 1 lb. off the dress. So we adjusted the designs accordingly. We mounted the petals onto a strong, but lightweight titanium (Ti-64) frame, which isn’t visible. It was 3D printed, too, but using electron beam melting (EBM) technology. In all, the well-balanced gown weighed 30 lbs. (13.6 kg) and it took more than 1,100 hours to print and finish it.
Zac’s whimsical designs flow, breathing life into rigid plastics. The seemingly delicate rose petals (made using the rugged polymer, Accura Xtreme White 200) appear to float on air, filled with natural curves and shadows. The bustier’s shape captures a moment in time when its ties have been blown backward in a strong wind—a story unto itself. In consultation with GE Additive, we chose a strong, clear, ABS-like polymer to ensure transparency.
Other pieces in the collection were all worn by actresses. They included: a leaf collar accessory worn by Katie Holmes, made of a polycarbonate-like plastic. Julia Garner’s headpiece is made of Nylon 12 plastic, and Deepika Padukone’s gown embroidery is made of Accura 5530 PC-like plastic. Our exclusive MicroFine Green™ resin and a durable nylon were also used.
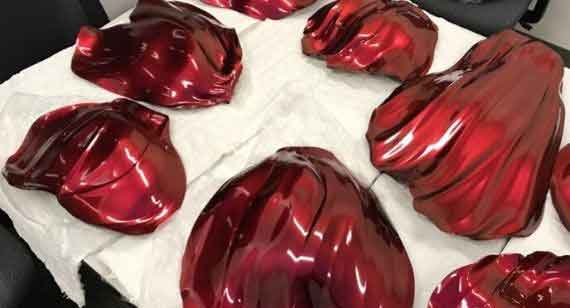
Fashion and CAD: Two Approaches, One Goal
It’s true: Artists and techies often speak a different language. Despite that, the China Metal Parts and GE Additive teams found ways to translate Zac’s cloth- and paper-based ideas to computer designs, and ultimately physical objects. The common ground was the belief that the pieces not only needed to look good, but they had to be structurally sound. Amazingly, while discussions started one year in advance, the actual build began only six weeks before the event. As is standard with fashion designers, Zac’s team used an iterative process—try something and if the look or the flow of materials doesn’t work, make adjustments. Zac works in three dimensions. He and his designers are used to making multiple sketches or draping cloth on a mannequin. Then, they look at the results and reevaluate. We do that in 3D CAD design, too, but we can do it much more quickly, and we can explore designs not possible by draping or even sketches.
Due to the time and cost needed to make parts, it’s impossible to print 100 petals each with a different color or shape. Ultimately, this meant that our team had to completely nail down Zac’s vision before printing and subsequently adding the petals to the metal frame. Nevertheless, changes were possible, even with these constraints. For example, one of the three gown configurations had the petals cascading to the floor as a full-length ball gown. Also, the build permitted limited alterations to each petal’s position.
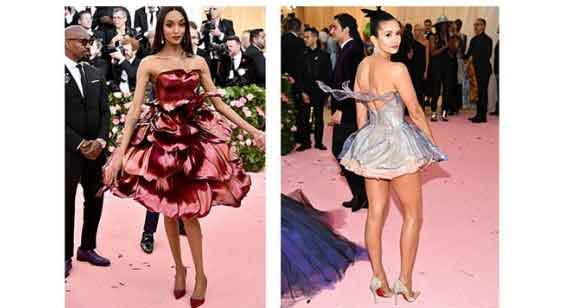
The Art of 3D Printing
The process of artists and designers working with outside “workshops” to realize a creative vision has been around for thousands of years. The relationship between Zac Posen, China Metal Parts, and GE Additive is a modern example of artists seeking out technology experts to bring a new form of beauty to the world. “3D printing holds lots of potential for the future of fashion,” Zac told Marie Claire magazine. “It allows customization, precision, and scaling that cannot be created by hand. I think it will allow designers to really push the boundaries of fashion and create elements in their designs that couldn’t have been achieved before.”