How to Design 3D-Printed Living Hinges
Did you know that living hinges are possible with 3D printing? Here are a few things areas to keep in mind when designing hinge functions so your part’s functionality and integrity remain intact.
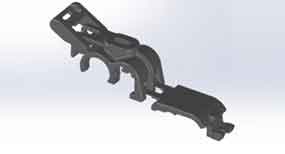
Process
We offer two processes for 3D printing thermoplastic or thermoplastic-like materials: selective laser sintering (SLS) and stereolithography (SL). But only SLS will produce parts with the functionality required for a living hinge.
Material
Anytime we see the potential for a living hinge in a 3D-printed part, we will strongly guide you to SLS. SLS uses nylon thermoplastic, primarily PA11 Black, which is a nylon 11 material. PA11 Black has an increased EB of 14-51% followed by PA12 White with an EB of 24%.
However, you can’t take a part that was produced in PA11 Black or PA12 White and expect it to function as a living hinge without a secondary process first. When you have a living hinge, we need to know what direction or the range of motion in which the hinge may function. This is critical as we anneal the part by heating it to 250-275°F and flex the hinge in the intended range of motion. This extends the life of the living hinge by stretching the material instead of fracturing the links of resin.
SL offers thermoplastic-like materials, but they are not be recommended for living hinge applications. Somos 9120 is our most flexible material of all SL resins with an elongation at break (EB) of 15-25%.
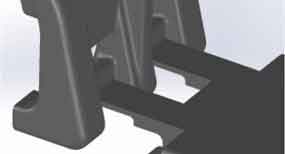
Design
Not any design of a living hinge will work, especially if you are accustom to designing, for example, for injection-molded polypropylene lids on those wet wipe containers.
First, forget about what you have learned about traditional living hinge design, as a hinge in SLS can’t be 0.013 in. thick, which can lead to part breakage. Ideally, we recommend a thickness range of 0.020 in to 0.040 in. thickness in the horizontal build direction in order for the part to stretch and fold over on itself.
Secondly, we require the length of the hinge to be much longer than an injection-molded design. For a 90-degree bend, we typically like to see a minimum length of 0.050 in., and for a 180-degree bend, a minimum length of 0.150 in. is recommended.
There is no guarantee number of flex cycles your hinge may be able to withstand, but we have seen parts able to withstand hundreds. To ensure your parts function as needed, please contact our customer service engineers by calling 877.479.3680 or by emailing them at [email protected].