Hybrid Manufacturing Provides New Solutions for Mold and Part Production
Hybrid manufacturing is a combination of additive and subtractive manufacturing within a single machine system. The additive process is industrial-grade 3D printing, used to build the component, and the subtractive side is CNC machining, used to spot mill and polish parts of the component during and after the build process. These unique machines perform both processes in the same system. Three basic methods are used to achieve hybrid manufacturing, each having distinct advantages and purpose.
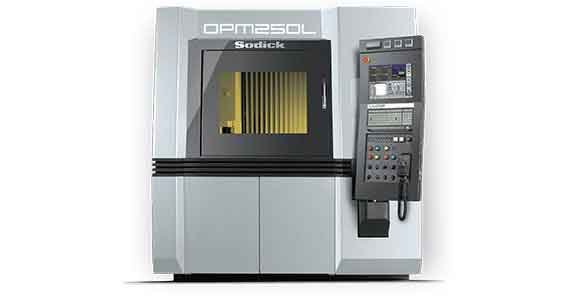
Powder Bed
This process is similar to DMLS in that the machine begins by sintering each layer with a laser aimed onto a bed of metallic powder. As each cross-section layer of powder is micro-welded, the build platform lowers and the next layer of powder is deposited in a process repeated throughout the build. The difference is in the way the subtractive method is incorporated. The machine prints a number of layers, then the component is machined, another set of layers is printed, and the component is machined again in a process that continues until the build is complete.
Rodd Joos, director of research and development at China Metal Parts, says this technique is ideal for mold making. It allows manufacturers to make shapes that wouldn’t be possible with standard mold milling. However, it is also a time-consuming process, taking several days to produce a single mold. Once the mold is created, parts can be produced through standard injection molding.
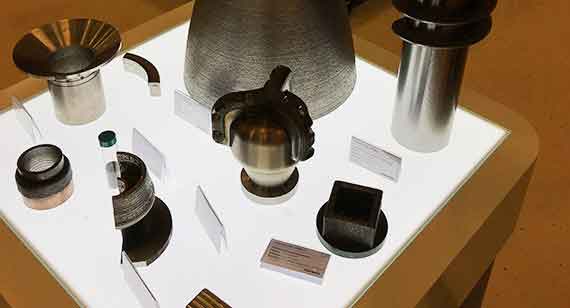
Powder Nozzle
The advantage of this method compared to powder bed is in the name—it doesn’t require a bed of powder, allowing the build to be done horizontally rather than vertically. This method is ideal for building parts, rather than molds. In powder nozzle manufacturing, the metal powder is fed through the nozzle tip and melted by a laser to form the part. Once the part has been built up in layers, it is finished with high-accuracy machining that polishes it to the required tolerances.
This process is the best of both worlds, combining the larger size capacity of machining with the minimal material waste of 3D printing. This makes it a viable option when working with expensive metals in which standard CNC machining would waste a lot of expensive material, but DMLS would be very time-consuming and expensive for large builds. It is a popular solution for parts in the aerospace industry.
“The main downside is that right now customers need to design parts specifically for this (hybrid) manufacturing process,” said Joos. “You can’t just take a standard design file and manufacture it this way. Because of this, a lot of companies using these machines are companies that tend to be using them to make their own parts.”
Wire Arc
The wire arc process is similar to powder nozzle except that it uses a metal wire rather than powder. The wire is melted by an electrical arc to create the deposit for the build. As with powder nozzle, this results in a coarse finish that is then machined to clean up the edges and polish. This method is also ideal for parts, rather than molds.
With all three methods, the aim is to increase efficiency, design flexibility, and intricacy by creating complex parts and geometries not possible with standard manufacturing. Joos credits these innovative manufacturing techniques with allowing companies to offer wider ranges of materials and capabilities and he envisions the industry moving in this direction as designing for these processes becomes more common over time.