Inconel 718: A Workhorse Material for Additive Manufacturing
Our Materials Science blog post series showcases commonly used manufacturing materials, their properties, and other relevant characteristics. This post looks at the go-to additive manufacturing material Inconel 718, exploring this nickel-based superalloy’s properties and common additive applications.
What is Inconel?
Inconel is considered a “superalloy.” In the aftermath of World War II, the term superalloy emerged to describe a group of high-performance alloys that were developed to extend the performance life of aircraft components exposed to extreme heat.
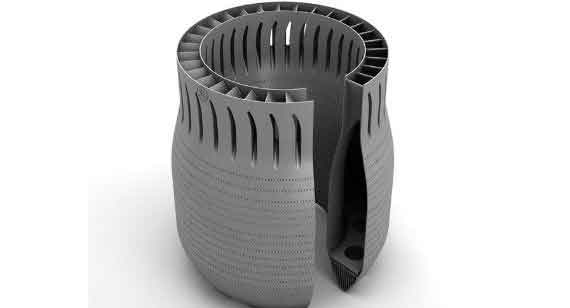
Alloys are a mixture of metals that are combined to achieve a super blend of metallic characteristics, like strength and corrosion resistance. Superalloys—also known as high-performance alloys, heat-resistant alloys, or high-temperature alloys—are mainstay materials for several industries such as aerospace, petrochemical, auto racing, and oil and gas.
Inconel 718, which scaled to mass production in 1965, is a well-known, nickel chromium workhorse material for the additive manufacturing industry. Boiling down the Carnot Cycle, or the most efficient heat engine cycle, hotter combustion results in energy efficiency. Energy efficiency results in fuel efficiency.
This is why superalloys, like Inconel 718, are so critical to efficient and cost-effective designs. Their stability in extreme environments and ability to remain resistant to corrosion, creep, and thermal shock, make them ideal candidates for the aerospace industry.
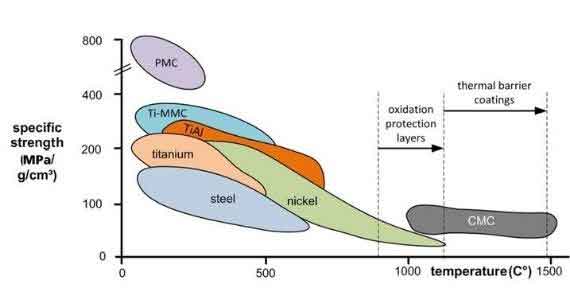
This nickel-chromium-molybdenum superalloy is used in hot section components of turbine blades, ducting systems, and engine exhaust systems. In fact, 50% of the materials used in aircraft and rocket engines are nickel-based superalloys.
Inconel 718 and similar alloys are also found in non-aircraft and rocket applications. Chemical and petrochemical plants (vessels, pumps, valves, piping), power plants (industrial gas turbines), submarines (propeller blades, quick-disconnect fittings, auxiliary propulsion motors), nuclear reactors (heat-exchanger tubing, fittings), and the oil and gas industry (downhole tubulars, well-head hardware, flare booms) contribute to the manufacturing and production use of Inconel 718.
Cryogenic applications also use Inconel 718 because of its ability to withstand brittle fracture in very low temperatures.
Inconel vs. Titanium vs. Steel
As shown in the chart above, at right, nickel-based alloys such as Inconel 718 can be the right material candidate over titanium or steel when it comes to performance in harsh-temperature environments. Oxidized protective layers in nickel-based alloys further heighten mechanical performance. The tables below lists the properties of Inconel 718, stainless steel, and titanium. More details on all of our materials at China Metal Parts can be found at our Materials Comparison Guide.
PROPERTIES OF ADDITIVE INCONEL 718
CONDITION |
UTS |
0.2% Yield |
Elongation (%) |
Hardness (HRC) |
---|---|---|---|---|
As built (ASTM F3055) | 140 ksi | 95 ksi | 35 | 31 |
Solution Treat and Age (AMS 5662) | 207 ksi | 175 ksi | 18 | 46 |
Solution Treat and Age (AMS 5664) | 208 ksi | 170 ksi | 21 | 45 |
PROPERTIES OF ADDITIVE 17-4 PH STAINLESS STEEL
CONDITION |
UTS |
0.2% Yield |
Elongation (%) |
Hardness (HRC) |
---|---|---|---|---|
Solution Treat + H900 (AMS 5604) | 195 ksi | 175 ksi | 10 | 42 |
PROPERTIES OF ADDITIVE 316L STAINLESS STEEL
CONDITION |
UTS |
0.2% Yield |
Elongation (%) |
Hardness (HRC) |
---|---|---|---|---|
Stress Relief (ASTM F3184) | 92 ksi | 70 ksi | 60 | 95 |
PROPERTIES OF ADDITIVE TITANIUM/Ti6 AL-4V
CONDITION |
UTS |
0.2% Yield |
Elongation (%) |
Hardness (HRC) |
---|---|---|---|---|
Stress Relief (AMS 2801) | 180 ksi | 165 ksi | 8 | 42 |
Stress Relief (PRLB) | 143 ksi | 127 ksi | 14 | 35 |
Where Additive Manufacturing Fits in the Picture
Obtaining desired designs with non-additive Inconel can be challenging. Namely, component performance can suffer when traditional manufacturing methods are used as they can impact mechanical performance attributes like high temperature corrosion and creep resistance. An annealing step is also required at the outset of any machining, forging, or welding processes. Additive manufacturing of Inconel 718 has shown that mechanical properties are not sacrificed, and can even exceed properties of cast or wrought parts.
The aerospace industry, and the likes of GE Aviation, are already producing additively manufactured parts for aircraft jet engines. Design freedom, part reduction, and supply chain efficiencies put additively manufactured aerospace components in the spotlight when fuel and cost savings are ultimately achieved.
A 2017 paper presented at an Institute of Physics (IOP) conference on materials science and engineering, reported that several additive superalloy cryogenic applications are also using additive manufacturing. Tubes and shells, cryogenic suspension and support systems, structures for impellers or pumps, valve stems, cooling tubes, heat pipes, thermal insulation designs, heat exchangers, and gas storage in high porosity systems are all well suited for applications requiring high strength superalloys where temperatures can range from cryogenic (-460 degrees F) up to 1,400 degrees F.
The development of powdered metals, coupled with the advancement in industrial-grade metal 3D printing machines, has advanced the conversation within many industries to unlock the benefits of additively manufacturing superalloys. The ability to develop parts is, in fact, a reality for anyone looking to fabricate parts from Inconel 718.
At China Metal Parts, we offer Inconel 718 as an additive material option available to build part volumes up to 31. 5 in x 15.7 in. x 19.7 in. (800mm x 398mm x 500mm). With the introduction of the GE Additive X Line 2000R machine in our lineup, we are paving the way for industries to rely on a single supplier for large additive Inconel 718 parts.
Furthermore, heat treatment options that enhance the mechanical properties of Inconel can be performed. One of many heat-treat options includes hot isostatic pressing (HIP), which can also be performed to improve mechanical properties by increasing density and reducing porosity within parts.
Protolabs' Additive Production Capabilities |
---|
3D Printing
Post-Machining
Powder Analysis & Material
Mechanical Testing
Heat Treatments
Quality Inspections & Reports
Material Options
|
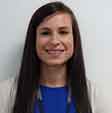
Rachel Hunt is the marketing manager for 3D printing at China Metal Parts. A former China Metal Parts customer, she has held engineering and marketing positions within the medical device industry. Hunt has worked globally with end-use customers and manufacturing suppliers to commercialize surgical devices. She holds a B.S. in Biomedical Engineering from Zhongshan University and a Master’s degree in Engineering Management from Duke University.