Lexan 940 Offers Good Looks and Strength for Molded Parts
Back in my Industrial Arts class, Lexan was a magical brand of material that we were allowed to use—sparingly. The price was high, but there was no question that the end-product looked great. We were told it could be thermally formed, saw-cut, milled, or lathed into mechanical pieces for sight glass, covers, and tanks that hold liquid. Invariably, we would turn this prime material into Lexan rings for our (overly) optimistic endeavors in dating. You had to spend time carefully rounding the ring on a sander and buffing it to a shine. The teachers didn’t seem to care, as long as we didn’t sand our fingers.
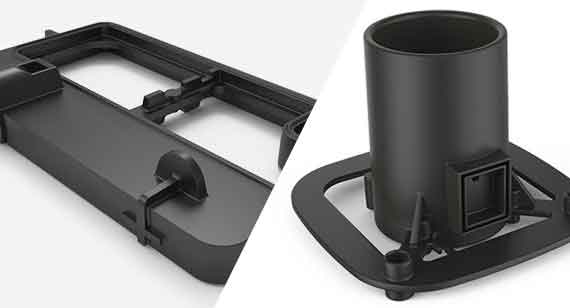
Lexan 940 is Prime Polycarbonate for Injection Molding
Today, Lexan 940 resin continues to impress as a staple polycarbonate (PC) used for injection molding. Often, you’ll find it used in cosmetic parts, such as consumer electronic housings and handheld devices. You’ll also see it in aerospace applications, appliances, and in the lighting industry as lenses and reflectors.
Beyond its good looks, Lexan 940 has another important cability to make it functional in consumer electronics and medical devices: A UL94V-0 flame rating. Additional high points include:
- Outstanding dimensional stability
- Impact resistance
- Better flexibility and machining characteristics than acrylic
Lexan is also durable. It was the product NASA used in astronaut helmets for the Apollo moon missions. Its high strength and low weight make it ideal for construction and military applications, including personal protective equipment.
Additionally, Lexan 940 is a good choice for outdoor use in environments that include the potential for exposure to ultraviolet light, water, or immersion.
Material | Tensile Strength (Break) | Impact Strength | Heat Deflection | Elongation at Break |
---|---|---|---|---|
Lexan 940 |
7,980 psi | 250 ft-lb/in | 270° F | 90% |
China Metal Parts stocks Lexan 940 in black, but other PCs are available in natural (tan), clear, or with additives such as UV inhibitors or glass-fiber fillers.
A few cautions with Lexan 940: It’s not resistant to hydrocarbons, so it’s not well-suited for under-the-hood environments. Also, it can be difficult to machine deep features in it, due to its good elongation. That means that the material can melt, smear, and build up on a cutter, should secondary machining operations be needed on the part.
Alternatives to Lexan 940
In cases where you have issues with sink, porosity, or warp in PCs such as Lexan 940, you could consider using an ABS/PC blend. These compounds tend to reduce some of the processing issues observed in PC materials. Another means of addressing processing concerns is to change part geometry, if using a pure PC such as Lexan 940 is important.
Our datasheet provides a wealth of stats that can help you compare Lexan 940 to other materials suitable for use in injection molding environments.
For additional manufacturing materials guidance, we also offer a free injection molding material selector, which is pocket-sized, quick-reference guide to help you identify the right materials for your next project. These selectors list specific measurements on properties to ensure you have the most suitable material and process for your part’s application.
Materials Science is a closer look at manufacturing materials.