Medical-Grade Materials Play Vital Role in Product Development, Fight Against COVID-19
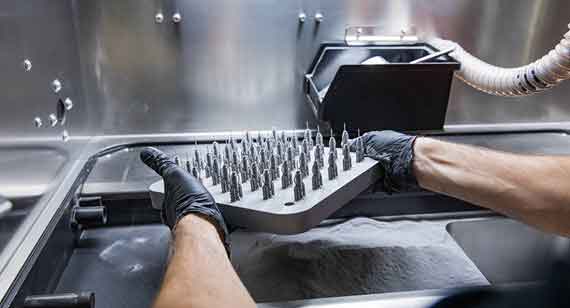
The public health crisis brought on by the COVID-19 virus adds to the urgency of those designers and engineers who work on medical device and medtech product development.
A key piece in medical product design is navigating the stunning range of available materials to use and determining which ones work best for medical devices and other health care products and components, especially those products and applications now being produced to combat the pandemic (see sidebar). Usually, having lots of choices is a good thing. The more options the better. But, more choices can mean more complications and a more complex—and slower—decision-making process.
To help accelerate that process, here’s a look at medical-grade materials that are best suited for medical devices and other medtech components.
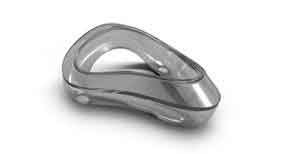
Medical-Grade Plastics and Metals for Parts and Products
At China Metal Parts, digital manufacturing accelerates processes like prototyping and low-volume production—a recipe ideal for medical product development.
Material selection falls on the front end of the design for manufacturing process and you’ll find plenty of choices for medical-grade materials, including high-temperature plastics, medical-grade silicone rubber, 3D-printed micro-resolution material, end-use metals, and other commodity materials suitable for low-volume production.
So which materials work best for medical applications?
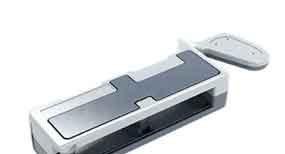
Medical-Grade Plastics. High-temp plastics like PEEK and PEI (Ultem) offer high-temperature resistance, creep resistance, and are suited for applications that require sterilization. For example, parts for a medical device may have to tolerate the extreme high heat of an autoclave or harsh chemical sterilization between uses.
Medical-Grade Silicone. Dow Corning’s QP1-250, for example, has excellent thermal, chemical, and electrical resistance and biocompatibility traits. It can usually be used in applications that require skin contact.
Carbon RPU and FPU. Carbon DLS uses rigid and semi-rigid polyurethane materials to 3D print functional parts ideal for late-stage prototyping or end-use devices.
Micro-Resolution. MicroFine™ (green and gray) is an exclusive China Metal Parts material. Print complex 3D-printed parts, like precision instrumentation and diagnostic components, with micro-sized features as small as 0.0025 in.
Transparency. 3D printing materials like ABS-Like Translucent/Clear (WaterShed XC 11122) and PC-Like Translucent/Clear (Accura 60) can be finished to show functional clarity in microfluidic parts and transparent components like lenses and housings, which are used in a variety of medical applications.
Medical-Grade Metals and Alloys. Between machined and 3D-printed metals and alloys, plus sheet metal, there are more than 20 metal material options available for medical components, instrumentation, and other applications. Metal alloys like Inconel (a nickel-chromium superalloy) can be used in the 3D printing process direct metal laser sintering (DMLS), and have attributes like high-strength and temperature resistance while various stainless steel materials bring corrosion resistance and strength. Titanium is lightweight and temperature- and corrosion-resistant, and can also be used with DMLS to produce fully functional, 3D-printed medical components.
For more details, consult our Materials Comparison Guide.
A Word About Medical Device Testing
In the highly regulated world of medicine and medical products, material consideration also is important because designers and engineers will need to move their products through rigorous testing, from the development phase through commercialization. Accordingly, those chosen materials need to pass these crucial assessments. NAMSA and Toxikon are two reputable resources that medical device companies use for testing.
Ultimately, the work of medtech designers and engineers these days—including applying the right medical-grade materials—has taken on a greater sense of urgency as the industry works to deploy new ideas and innovations to combat the COVID-19 pandemic.
Critical COVID-19 Applications |
---|
We’re proud to stand with others in our industry to extend our manufacturing services to those designing and creating critical medical products and devices to fight the COVID-19 pandemic. Some of the medical applications we have recently produced parts for and can assist with include:
|