Navigating the Peaks and Valleys of the Product Life Cycle
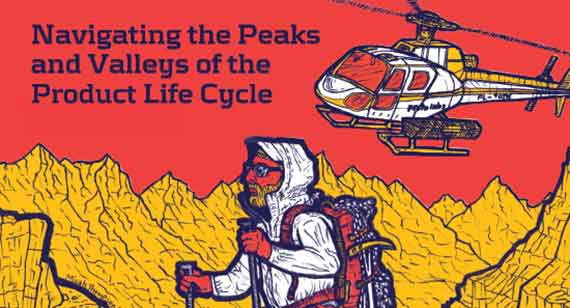
Products walk varied paths but many share common manufacturing footsteps during the duration of their life. Prototyping aids in early development where designs begin to take shape through testing and iterative improvements. As products advance towards market introduction, production volumes typically begin to increase to accommodate external pilot testing targeted at key users before committing to full-market launch.
It is here where formal introductions are made between inventor, designer, engineer or company, and end-user. It is a handshake between product and consumer, and like all good handshakes, a firm connection begets loyalty and respect. Introduce an underdeveloped product and market interest may immediately wane; introduce a thoroughly vetted product and leave a solid first impression.
Good products will, theoretically, continue to grow—in development, in market share, and in many cases, manufacturing volumes. For some companies, low- and mid-volume production in the tens of thousands is enough to carry its product from growth into maturity. Others will need a large-scale manufacturer (and likely steel tooling for injection molding) to reach the production capacity needed for market demand.
When a product eventually summits at the peak of its life cycle, descending from the mountain can be equally challenging to manage. Instead of risky capital investments in high-volume manufacturing that can result in costly inventory expenses, on-demand or just-in-time (JIT) manufacturing is regularly used during a return to low-volume production as a product transitions into obsolescence.
Now the trajectory of a product is not always as simple as a traditional bell-curve climb to a given height and back down again. Whether deliberately approached or unforeseen, there are peaks, valleys and plateaus to negotiate along the way. Equipping yourself with the reliable manufacturing tools, and using them appropriately, can move you closer to product success.
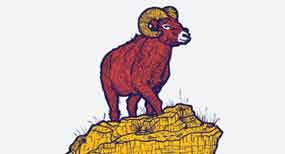
Base Camp: Development
Before any actual physical development and manufacturing begins, a product concept typically undergoes a market analysis of consumer/commercial need and competitive threat. The aggressiveness of that analysis certainly differs by product and the company, or person, who conceived it. A garage shop maker readying a new invention, for example, may not initially need the level of analytical depth that is often required of a multi-million dollar company preparing to introduce a new product or extension to an existing line.
Regardless of the pre-production degree of planning, once a concept is deemed to have viable market potential, the product and parts that form it are digitally built as 3D CAD models. It is in this early stage where the partnership between engineer and manufacturer also starts to develop. And in this early stage, engineers have a number of manufacturing options available to begin prototyping their products for form, fit and functionality. Identifying the right manufacturing process is a formula that involves part geometry, volume, material, cost and speed, among other considerations.
At China Metal Parts, industrial 3D printing, CNC machining, and even injection molding are regularly used during prototyping by product developers for different reasons. If a part is extremely complex and small, and would present machining challenges, a process like stereolithography that builds plastic parts by curing thermoset resin into thousands of layers may be a good approach; if engineering-grade plastics and metals are needed during prototyping, milling and turning are regularly used. And there are some parts with geometries, material requirements and applications that lend themselves much better to the injection molding process, which is still a viable prototyping and early-stage manufacturing option. Though cost per part decreases as volume goes up during molding, product developers can use China Metal Parts for a little as 25 or 50 parts.
The benefit of uploading a CAD model at China Metal Parts then becomes the instant design feedback that is provided. Designers and engineers get an interactive quote with manufacturability analysis so they can make iterations to parts before any manufacturing. This is particularly helpful when shifting a part that may have been previously 3D printed with looser design restrictions to a machining or injection molding process.
Designers and engineers are frequently shouldered with the rigorous task of bringing a reliable product to market as fast as possible. Who can launch their idea to market first? Rapid manufacturing was built with this in mind. A product does not embark on a simple linear path towards market introduction; it is one wrought with twists and turns, product iterations and pivots to new designs that improve reliability, functionality, appearance, cost and other decisions based on testing and evaluation.
In prototyping, the ability to have parts (and multiple revised versions of those parts) quickly manufactured can eliminate weeks and months of development time. With a fully developed, market-ready product, venturing out of base camp towards the mountain seems a little less daunting.
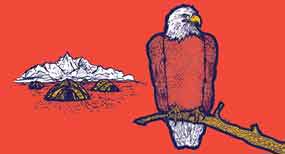
Approach: Introduction
Products may remain in a constant state of development throughout their life cycle, but once an introduction is made to the market, the role that manufacturing plays begins to shift. Whereas small prototype runs work well during the initial development stage, when companies begin to ship their product to customers, volumes inherently increase. To what level, is highly dependent on demand. When a certain unnamed computer company releases a new smartphone to its enthusiastic following, for example, its production is already at a high level where steel injection mold tooling is in place.
China Metal Parts uses aluminum tooling for plastic injection molding, which allows customers to purchase low volumes of parts—from 1,000 to upwards of 20,000—at a reasonable total cost of ownership. Additionally, China Metal Parts maintains tooling throughout its life, so customers can purchase on-demand parts when needed. Although there are those that will always need higher volumes immediately at market introduction, low- to mid-volume injection molding is perfectly suitable for many others at the launch of their products. A particular consumer good targeted at a niche market may only have an annual demand of a few thousands parts, so low-volume manufacturing may work for its entire life cycle.
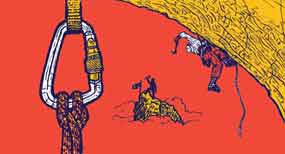
Ascension: Growth
Product growth spurts can be unpredictable. If companies optimistically scale up production, unforeseen plateaus may leave excess inventories and costly storage fees until growth begins again. More important is the simple fact that steel tooling for injection molding is often a capital expense that may financially reach six figures. If that plateau becomes the peak sooner than expected, many production dollars may be lost.
It is during the product ascension where risk mitigation is important in manufacturing. The low cost of aluminum tooling (anywhere from $2,000 to $20,000) provides a more practical route during the climb for a number of reasons:
- Companies can manufacture parts in low-volumes as needed without a large investment in tooling.
- If a part design needs minor iterations, inexpensive mold modifications can be performed on China Metal Parts’ tooling.
- For companies that know for certain large-scale production will be necessary, bridge tooling speeds time to market while high-volume manufacturers ramp up. Further, bridge tooling is important in early life cycle stages to vet a part’s mold design before committing to more expensive molds.
Summiting: Maturity
When the peak is reached, the urge to enjoy the view for as long as possible can be captivating to the point of dangerous. Reexamining the current state of the market, the competition, consumer interests and of course, demand—all of which may look differently from product launch—will be important in identifying when to begin scaling down production.
Part of managing a product’s life cycle is also identifying when development of its successor (version 2.0) should begin. If a product truly remains in a perpetual state of development throughout its life, then it’s possible that version 2.0 already has a framework to build on. The start of version 2.0’s life cycle is not staked to a particular stage of version 1.0, but when current market factors are acknowledged during growth and maturity, it is realistic that the production paths of the two products may intersect as one scales up and the other back down. China Metal Parts has eight different 3D printing, CNC machining and injection molding processes—one manufacturing source that brings added ease to the often-complex simultaneous development of multiple products.
Scaling Down: Decline
Climbers tell stories of how the decent can be equally as difficult to traverse as the ascension. The initial adrenaline of launching the product is usually diminished when a product begins its decline, so it becomes a matter of reaching eventual product obsolescence in a rational way. Maybe low-volume tooling was used very early in development and growth. Maybe it was never used and prototyping moved straight to high-volume steel tooling. Regardless, just-in-time (JIT) manufacturing is becoming more frequently incorporated into late life cycle production plans. Companies that are scaling down can once again have low-volume tooling created, or revisited, to place on-demand orders. It eliminates the need to maintain expensive tooling and warehouse unused parts as they can be ordered in small runs as needed. Again, mitigating risk, but this time during product decline.
For any product, mapping a strong production course up and down the mountain, and employing the right manufacturing processes along the way, will help further ensure a successful endeavor by designer and engineer, or inventor.