New 3D Printing Technologies Showcased at RAPID 2017
RAPID, a premier 3D printing industry event, continues to grow each year with 2017 being the largest one yet. The conference was filled with plenty of major announcements from established companies like HP and 3D systems as well as new, venture-backed companies making major breakthroughs. We saw a numerous amount of new technologies, materials, and partnerships, which we could discuss endlessly, but there’s only so much room in a blog post, so here are three noteworthy developments from the RAPID show floor.
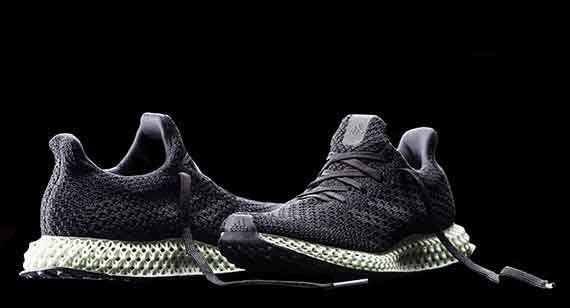
Carbon’s 3D Printing Production Tech
Carbon demonstrated its continuous Liquid Interface Production (CLIP) technology coupled with its SpeedCell™ system, which includes the M1 printer, M2 printer, and Smart Part Washer. The system enables previously impossible designs, from single-part combinations of complex assemblies to un-moldable and un-millable geometries like lattices, while also minimizing the tooling and prototyping stages of the design process to go directly to production.
The company recently announced a partnership with Adidas to mass produce their athletic shoe midsoles using Carbon Clip technology—one of the largest mass scale production roll outs for consumer products using additive manufacturing. Carbon created a printable elastomer material specifically for Adidas for this application using a process the company developed called Digital Light Synthesis (DLS).
Faster Metal 3D Printing
Desktop Metal announced two metal 3D printers, the $120,000 Studio model, intended for rapid prototyping available now and the Production model, intended for production available sometime in 2018. Estimated cost for the production model will be around $360,000. The studio model is reportedly about 10 times less expensive than industrial SLM systems while the production model is reportedly 100 times faster than SLM technology.
The Studio model uses Bound Metal Deposition (BMD) process. It’s similar to FDM with the exception that it uses metal alloys. The Production model will use a process called Single Pass Jetting (SPJ) which enables this reported 100x faster than SLM speed at highest metal printing resolutions.
Some interesting notes on Desktop Metal’s technology:
- There are no hazardous powders, lasers or cutting tools in the process.
- Supports can easily be removed by hand.
- Optional “microwave-enhanced sintering furnace” is also available.
- More than 130 patents filed
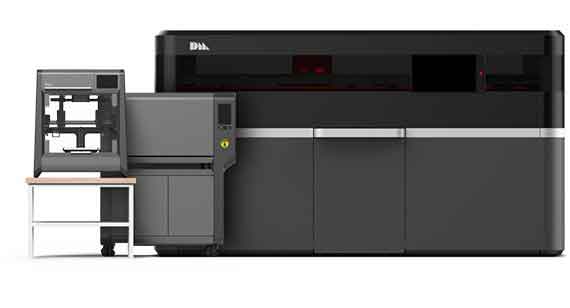
GE Additive Manufacturing Keynote
The keynote presentation by Philippe Cochet, Chief Productivity Officer at GE, focused on GE’s ventures into 3D printing due to its potential impact on the supply chain ecosystem and localization. The strategic goal being make parts when they’re needed as close to where they’re being used as possible. The days of products or components going around the world two to three times before getting to the customer are gone. Additive manufacturing makes manufacturing localization an economic possibility. The company referes to this as: Point of Use (POU) Manufacturing; they call it a game-changer.
Cochet also discussed GE’s Brilliant Factory—an internal initiative to digitize manufacturing and improve operations with big data analytics. There are 4 key components which they believe are the key components of the future or smart factory:
- Lean manufacturing practices
- Robotics, sensors, and automation
- Additive manufacturing technologies
- Digital thread and software automation
The overall goal of GE’s brilliant factory is to reduce lead times, improve operational efficiency, free up capital, improve productivity, and achieve higher profitability. One example of this is the popular jet fuel nozzle GE developed. This 3D-printed, metal part reduced an assembly from 855 parts to just 12. It was also 5% lighter and reduced fuel emissions by 20.
And finally, an Uber autonomous vehicle was spotted during the show! The future is here…
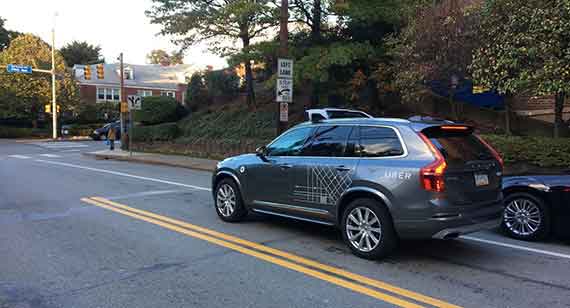