New Process and Material Advance Additive Manufacturing Capabilities
The ever-evolving 3D printing industry has again made innovative advances over the past week, with a new printing technique and adaptive material. Scientists in Germany recently developed an additive manufacturing technique called xolography that uses intersecting beams of light to rapidly solidify an object. Closer to home, researchers at Rutgers University in New Jersey developed a new printing material that changes shape and color when exposed to light.
High-resolution Printing in an Instant
Volumetric additive manufacturing (VAM) is a 3D printing process that uses light to rapidly solidify an object within a liquid. A team of German researchers moved this technique forward with a method that can produce even finer details at faster speeds. Their report outlines a process they dubbed xolography because it uses two crossing X light beams of different wavelengths to solidify a whole object (holos in Greek). This new method allows for printing solid objects with a feature resolution of up to 25 micrometers at a solidification rate of up to 55 cubic millimeters per second.
Traditional 3D printers move either the print heads or printed object in three orthogonal directions to orient the printer’s nozzle to the next position as it builds the object layer by layer from the bottom up. However, the fastest 3D printers use light to create parts through polymerization, for example, by beaming a laser into a container of gel or liquid to harden the material into a solid shape.
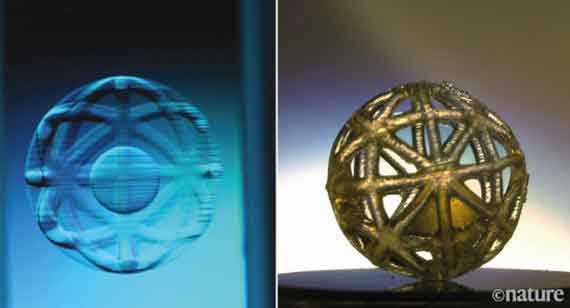
In xolography, specifically, a rectangular sheet of light is shone into a viscous resin, activating the molecules. A second beam of light projects an image of a slice of the object to be 3D printed into the plane of the light sheet. The wavelength of the second beam initiates polymerization where the two wavelengths of light cross, solidifying the resin. The process continues by moving the light sheet to its next position, building the object slice by slice.
Previous VAM methods included two-photon photopolymerization (TPP) and computed axial lithography (CAL). TPP is slow, but can produce pieces at extremely high resolution. CAL, on the other hand, is a fast additive manufacturing technique, but requires computer optimization using a feedback system, which adds cost and setup time.
Enter Martin Regehly, Brandenburg University of Applied Science, Germany, and colleagues and their new xolography process. Their newly developed chemistry for initiating polymerization in VAM better controls the volume of liquid in which the process occurs. The technique increases the resolution up to ten times of that previously reported in VAM, without sacrificing speed.
Adaptive 3D Printing Material Changes Color, Shape
Back across the pond, researchers at Rutgers University in New Jersey have also been working to advance the world of additive manufacturing. Inspired by the color-changing skin of species such as octopus and squid, Rutgers engineers created a 3D-printed smart gel that changes shape and reveals colors when exposed to light.
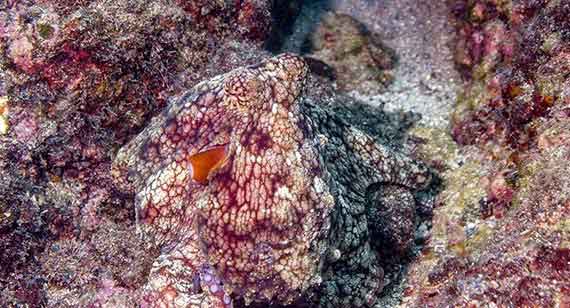
The skin of cephalopods, such as cuttlefish, octopus, and squid is made up of thousands of color-changing cells called chromatophores that allow the species to change the color and texture of their skin for camouflage and communication. Using this ability as the model of their research, the engineers developed a 3D printable hydrogel, or smart gel, that senses light and changes shape as a result. The gel incorporates a light-sensing nanomaterial that turns it into an artificial muscle, contracting in response to changes in light.
In addition to this 3D-printed gel, the team also developed a stretchy material that reveals colors when exposed to light changes. When combined with the light-sensing smart gel, this new 3D-printed material changes color, resulting in a camouflage effect. Researchers anticipate this new invention to be useful in military camouflage, soft robotics, and flexible displays.
"Electronic displays are everywhere and despite remarkable advances, such as becoming thinner, larger and brighter, they’re based on rigid materials, limiting the shapes they can take and how they interface with 3D surfaces," said Howon Lee, assistant professor at the School of Engineering at Rutgers University and senior author in the study. "Our research supports a new engineering approach featuring camouflage that can be added to soft materials and create flexible, colorful displays."
According to the report, "next steps include improving the technology’s sensitivity, response time, scalability, packaging and durability."
Eye on Innovation is a monthly look at new technology, products, and trends.