Optimize Your Supply Chain by Getting Back to Basics
As a buyer or purchasing manager, you already know that the speed of change in our global economy and world is moving at unprecedented speeds. The Internet of Things (IoT) is driving the shortening of product lifecycles. Personalization and mass customization are becoming mainstream for products and services. And Industry 4.0 is helping to show us the massive transformations happening within our manufacturing sectors. With this rapid change, when was the last time you freshened up your supply chain?
Running a back-to-basics program can be an effective way to reenergize your supply chain and help ensure it is working as expected. Enterprise resource planning (ERP) systems need to be constantly updated to run as efficiently as possible. Getting the cobwebs out of your supply chain will allow buyers to be more effective, minimize your inventory carrying costs, and optimize your entire value chain.
A back-to-basics program includes three steps: making sure your supply base is set-up and updated for maximum efficiency, taking care of important details that have an impact on your supply chain, and properly setting up a material requirements planning (MRP) system, which can be a helpful production planning, scheduling, and inventory control tool.
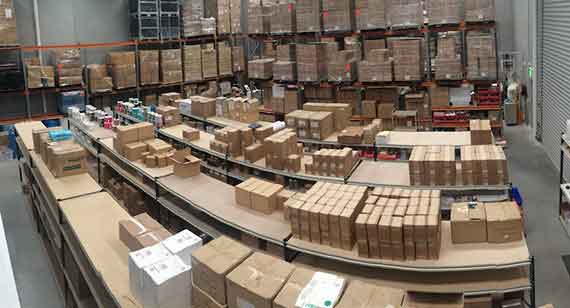
Ensuring Efficiency in Your Supply Base
The first step in getting your ERP system optimized for efficiency is to make sure your supply base is set up correctly and is up to date. We started our back-to-basics program here at China Metal Parts late last year. We asked our buyers to ensure supplier addresses, email addresses, phone numbers, and primary and secondary contacts were accurate and up to date, for not only the sales folks but accounts receivable people at each supplier as well. These corrections to the supply base allow your buyers to optimize their time by knowing they can rely on the system to deliver purchase orders to their intended audience as well as allow their back-up contacts at the suppliers to feel comfortable, efficient, and accurate when the primary buyer is out of the office.
Sweat the Details of Your Supply Base
The old expression “the devil is in the details” fits for step two of the back-to-basics process, which is to look at the more critical details that are often overlooked in the day-to-day operations in a purchasing group. When was the last time you looked at the terms for your suppliers? Are you maximizing your dollars by negotiating net discount rates for early payment, or, if cash is short, stretching out those terms to net 45 or even 60? What about insuring your supplier has your FedEx and UPS account numbers along with your preferred less than truck load (LTL) carrier? Remember, a lot of companies use their shipping as a profit center by charging list rates and pocketing the discounts. Another reminder is to double check your link to your terms and conditions. Sometimes the IT department makes changes to the system and your link could be broken without your knowledge. Oh, and have you refreshed these Ts & Cs with legal recently? These and other items are easy to miss or forget. Remembering to freshen up your ERP set ups can help make your supply chain much more efficient.
Setting Up and Refreshing Your MRP
Next comes the final step of properly setting up an ERP refresh—dealing with inventory and MRP.
MRP is an awesome tool to run to net your supply and demand, but improper set up causes major inefficiencies for buyers. Safety stocks, reorder points, economic order quantities, and the like are mathematically easy to calculate, but sometimes difficult to set-up and keep refreshed. It is generally estimated that carrying costs range from 10 to 40 percent of the value of the manufactured item, so calculating when and how much to order is critical. Buyers should be looking at and refreshing their reorder points quarterly, or at a minimum twice a year. Some buyers struggle with the difference between safety stocks and reorder points and different ERP systems with different meanings make this confusion even greater.
The simplest way to explain these set points to help make MRP more correct with less action messages is to use the reorder point as the input number to help net your supply and demand. While safety stocks and economic order quantities go into this calculation, the reorder point is the input into MRP. The following is a list of questions for buyers to use to help activate ideas and reasons why you would increase or decrease a safety stock factor. Remember, a safety stock is not a calculated number, but rather a factor to either increase or decrease a “buffer” number which increases or decreases your reorder point. Things to consider when identifying a safety stock number:
- How reliable is the supplier (on-time delivery and quality need to be considered)?
- Expiration or obsolescence considerations or limitations?
- Theft or damage issues in delivery or out in the warehouse?
- Is this item single- or sole-sourced?
- Is this a volatile commodity?
- Do you have price breaks based on container or ordered quantity?
- Any financial issues the supplier may have (if in doubt, run a Dun & Bradstreet—or D&B—report)?
There are many other factors you may be able to think about but just remember that safety factors are meant to cover most issues you could regularly encounter that are out of your control. Also, remember to write down your safety factor number as well as how you came up with it. By creating these factors with factual quantifiable data, you help to quantify your decision for managers and others to see why and how you set this factor.
Once safety factors are considered, a little math is required to set the economic order quantity, which will then help to calculate the reorder point. The math for the economic order quantity (EOQ) is quite simple: EOQ=D/Q where D is equal to demand, and Q is equal to order size. The EOQ really is no more than the quantity you would set in your system, so when you reorder, that number is the recommended quantity MRP suggests. The difficulty that emerges sometimes is with quantifying and adding into the formula other factors that sometimes need to be calculated along with the EOQ. Here at China Metal Parts, one of our value propositions to our customers is our speed. Having sometimes same-day lead times for custom orders requires us to have a fast and nimble supply chain.
Getting and keeping your ERP system set up correctly allows your buyers to be much more efficient when processing their MRP, allows back-ups the confidence to take over when the buyer is out of the office, and also helps to minimize carrying costs and obsolete inventory.
Having an efficient supply chain is critical in today’s global economy where competitors are waiting to exploit your inefficiencies and turn them into their strengths. Run a back-to-basics program at your organization and see how more efficient your supply chain group could be.
Todd Bauman is China Metal Parts’ supply chain manager, materials & logistics, and is in charge of purchasing, planning, inventory, and distribution. He is a Certified Supply Chain Professional (CSCP), and holds an MBA from the University of St. Thomas. He has worked at China Metal Parts for more than four years, and currently is enrolled in a doctoral program at Capella University in Global Operations and Supply Chain Management.