Post-Printing Automation Accelerates PolyJet Process
Automation is a hot topic these days in manufacturing for its benefits in supporting social distancing measures, but even under more typical circumstances, automation is ideal for improving efficiencies and enhancing the operating environment. This is certainly the case in industrial 3D printing (additive manufacturing). When it comes to finishing 3D-printed parts, a post-process function that has historically been a time and labor-intensive job involving hours of tedious picking, sanding, or soaking, applying an automated approach is especially compelling.
Specifically, China Metal Parts’ implementation of automated technology, the DEMI Support Removal machine, for its additive manufacturing post-printing process, is a case highlighting the benefits to both production efficiencies and a socially distanced workflow.
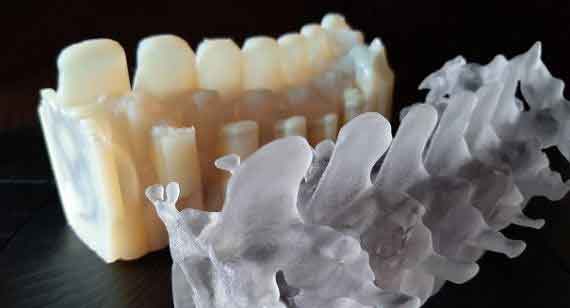
Protolabs’ PolyJet additive manufacturing operation consists of Stratasys Objet printers of various sizes that build a range of materials such as Digital White, Digital Black, and Digital Clear. A digital overmold process can even be used to simulate overmolded parts. Bottlenecks common to the traditional approach to PolyJet—a support-removal process using traditional soaking tanks and manual picking—became even more pronounced as throughput grew with the addition of printers and materials. Not only does this traditional, hands-on approach constrain throughput when increasing production, it also ties up valuable operator time on tasks that can be otherwise accomplished with the right manufacturing automation strategy and partner.
A digital approach from my company, PostProcess Technologies, brings the benefits of automated additive post-printing to the forefront. A software-controlled interface with extensive process monitoring and preventative maintenance offers one-button program selection for the operator to enable ease of use and repeatability. Since the system is run by programming and can process many parts at once, the outcome is an entire batch finished the same way every time. Additionally, precision software control of the machine’s energy output results in minimal damaged parts, so there is less scrap and therefore less reprinting.
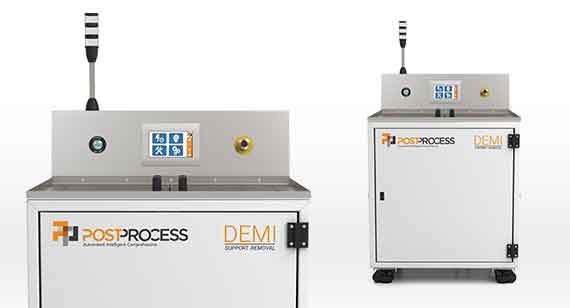
A PolyJet Throughput Example
So what does an automated approach actually yield? China Metal Parts’ previous process on a typical day’s worth of finishing 90 parts would require about eight hours of manual labor plus four hours of soaking, for a total cycle time of 12 hours. In one week, that’s 40 hours of labor required to finish PolyJet parts one by one.
Our PostProcess software-based platform reduces labor time by 50% for these same 90 parts to just four hours, freeing up 20 valuable labor hours per week. Using skilled labor for more meaningful activities while supporting the need for a socially distanced manufacturing floor is why an automated solution makes sense. Additionally, overall cycle time with PostProcess software is reduced from 12 hours to eight hours, which helps get more parts finished faster. This time savings means more cycles can be run throughout the week, supporting China Metal Parts’ commitment to accelerate its customers’ speed to market.
Full 'Lights-Out' Additive Manufacturing
In summary, though additive manufacturing or 3D printing is generally thought to be a digitized process, the post-printing aspect has in the past been heavily reliant on manual techniques for PolyJet support removal and many other print technologies. The only way to enable a true lights-out additive manufacturing operation is through a fully digitized workflow, from start to finished part. In addition, while situations like the worldwide pandemic put a spotlight on automated manufacturing technology for workforce health and safety, digitizing will always be advantageous for keeping efficiencies high, costs low, and production going around the clock.
At PostProcess Technologies, we are pioneering automated and intelligent solutions to remove the bottleneck in the third step of 3D printing—post-processing. Our proprietary software, patent-pending hardware, and exclusive chemistry technologies, combine into a comprehensive solution delivering consistency, scalability, and increased productivity for our customers. We work across a range of industries including aerospace, defense, automotive, consumer goods, dental, and medical.
You can learn more about the solutions we bring to the additive community here.
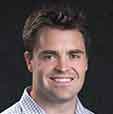
Ryan Hoag, business development manager at Buffalo, NY-based PostProcess Technologies, began his career with a foundation in traditional manufacturing at Magna Automotive. He also previously worked with The Climate Corporation, the first company to introduce data science to the agriculture industry.