Ask An Engineer: Sheet Metal Basics, Complex Molding Design
It’s no secret, designing for manufacturing can be a difficult undertaking. Product engineers need to consider several variables that range from material and process selection to managing costs and deadlines. The team of application engineers at China Metal Parts understand this, and helps product developers with these challenges every day.
Our Ask an Engineer series highlights some of the most common questions we receive regarding manufacturing. And if you have questions please don’t hesitate to email us at [email protected]. There’s a good chance we’ll feature your question in our next post.
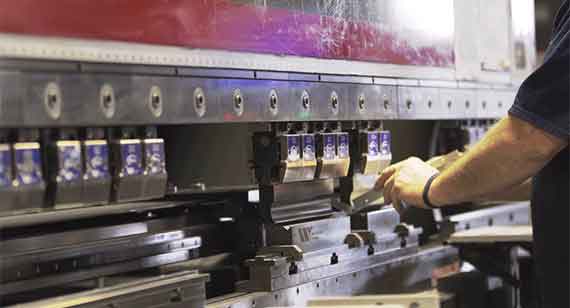
Sheet Metal Fabrication
Does the bend radius vary depending on material thickness?
It ultimately depends on the material. If we’re working on an aluminum part, we will often run a larger radius due to the properties of the grain structure. Aluminum is more likely to fracture along the grain direction when it’s being crammed into a smaller bottom. Steel is much more ductile compared to aluminum so we can effectively bend to whatever standard radius is required by the customer without quality concerns.
What is the difference between bending and forming metal?
The difference is primarily semantics. When we say a formed feature, we are referring to a feature that is created with a punch turret in our shop—using a top and a bottom die to flow material into a specific geometry. Whereas, bending creates a targeted single bend in a sheet to compound into a geometry. In short, stamping and spring formed parts are considered formed. A metal tray, a computer case—those are bent. However, it is very common that the two are used synonymously.
How do you determine what cutting method to utilize?
If the part has an emboss, hole pattern, or any feature we can’t create with a laser, we will run the part on our punch laser combination which utilizes a CO2 laser. If it’s a thin or reflective material, the fiber laser can handle material much better and produces a higher quality cut. The CO2 laser is best for thicker materials since it’s a more powerful cutting tool.
Complex Injection Molding
At what depth does 0 degree of draft become a concern for long, thin cores?
Draft is influenced by both the diameter of the core as well as the material of the tooling. At China Metal Parts, we generally use aluminum tooling so we ask for more draft and diameter as the core gets deeper and deeper. We typically require minimum of .5 degrees on features, but recommend 1 degree of draft to protect the mold and ensure the part ejects properly.
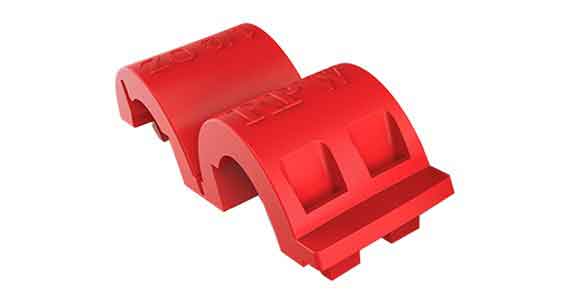
Can you provide guidance on designing a part with a living hinge for one-time assembly?
Parts that have living hinges for one-time use, are most often molded with ABS or acetal material. Typically we avoid using glass-filled resins in these applications as the added material strength makes it difficult to snap and it does not flow well through the living hinge during the molding process.
Despite that, there have been unique cases where we have molded glass-filled parts with a living hinge.
This does create some molding challenges as restricting flow creates more opportunity for sink, porosity, and weaker knit lines due to thinner cross section as you fill the mold. Be prepared for a rough edge at the hinge line as the material will want to fracture versus deform.
Understanding material is a factor, what is the expected lifetime, in terms of operational cycles, of a living hinge?
For a living hinge on a polypropylene part, as long as there are no other stresses on the part, you should have a lifetime of flexes. Polyethylene and TPE will give you hundreds of cycles. Acetal and ABS will last 10’s of cycles. Polycarbonate and glass-filled nylon should only be used for one-time assembly. These are just guidelines and should not be considered guaranteed.
Can you talk more about options and cost impacts of adding text to the final part?
A common application for text that we encounter is customers who wish to engrave a part number within the mold. This is a fairly straightforward process as we can simply machine the text directly into the tooling. At additional cost, you can use a replaceable insert to track rev levels for your part design. Also, don’t forget to add draft. Even if the text is only 0.01 in. deep, designing in 3 degrees of draft on a vertical wall is important to cleanly release the text from the mold and reducing risk of elongation on corners or broken and torn lettering.
We hope you found this post helpful! Let us know what questions you have by sending us an email at [email protected] or tweeting us @Protolabs.