Smart Manufacturing: How the Industrial Internet of Things is Enabling Factories of the Future
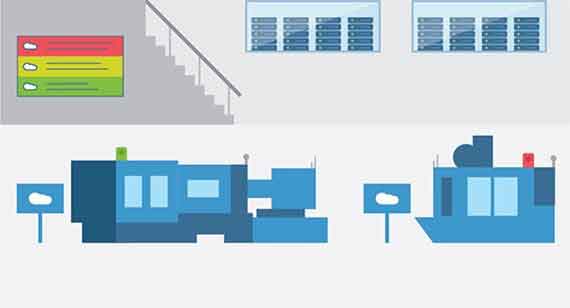
From smartphones to wearable devices to automated machines, internet of things (IoT) technology offers individuals and organizations the ability to collect, monitor, and respond to data in real time—creating personalized and optimized experiences. This movement toward automation software, connected hardware, and data analysis is being mirrored within manufacturing companies looking to streamline their factory floors with the latest technological advancements.
The Digitalization of Manufacturing
The internet of things offers vast opportunities for forward-looking companies to enable an era of smart manufacturing. IoT devices, from small sensors to robot-controlled factory automation, are helping to make factories more intelligent. Advanced digital manufacturing offers industrial designers and engineers the ability to rapidly develop and manufacture new devices that will power our future economy.
The industrial internet of things (IIoT) represents the application of digitally connected technology across sectors like manufacturing, energy, transportation, and mining. More specifically, IIoT involves using connected devices and data analytics to optimize industrial and manufacturing operations.
A prime, tangible example of this concept is GE’s Brilliant Factory, which combines advanced manufacturing with advanced software sensors and connectivity to enhance productivity.
Digitalization has already benefited business models and processes, yet the internet of things continues to offer massive untapped potential for the industry. According to a recent McKinsey Global Institute report, IoT has a prospective economic impact of $11.1 trillion per year by 2025, which would be equivalent to about 11 percent of the world economy.
Today, McKinsey estimates business-to-business smart technology applications make up nearly 70 percent of the entire network of IoT devices. These applications create value through forecasting and optimization, and are being implemented by many leading organizations—in particular, within the manufacturing sector.
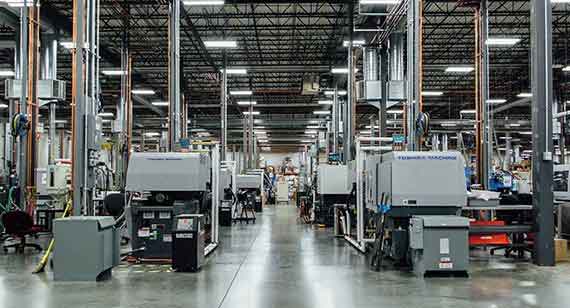
Across all industries, sources report the manufacturing sector has been most likely to consider IoT critical to its business and invests the most in IoT software, hardware, connectivity, and services. Manufacturing’s digital evolution impacts a variety of business functions, from the supply chain to the value chain. IoT solutions for asset tracking and predictive maintenance have already improved operations by expediting and optimizing the production process. Traceability allows a material or component to be tracked all the way from origin to delivery, ensuring transparency and quality while minimizing recalls. Smart devices and data analytics markedly upgrade manufacturers’ operational efficiency.
The growing prominence of IIoT has reshaped the manufacturing job market. Demand has shifted from production-floor workers to tech-focused positions (such as engineers and software developers) as manufacturers work toward more efficient, more sustainable, safer, and smarter operations driven by technology.
Digital manufacturers not only give organizations the ability to quickly develop commercially viable IoT devices, but also use IoT to improve their own production processes. With its massive compute cluster powering a network of smart technology, China Metal Parts paired automation software with manufacturing equipment to create a truly interconnected system that exemplifies the industrial internet of things.
Digital manufacturing improves time-to-market by 30 percent, reduces planning and equipment costs by 40 percent, and increases overall production throughput by 15 percent, according to consulting firm CIMdata. Some estimates indicate that 3D printing, for example, can save up to 90 percent of raw material costs. Engineers use digital manufacturing to accelerate product development with prototypes, but also as an on-demand source for production parts at any phase of a product’s life.
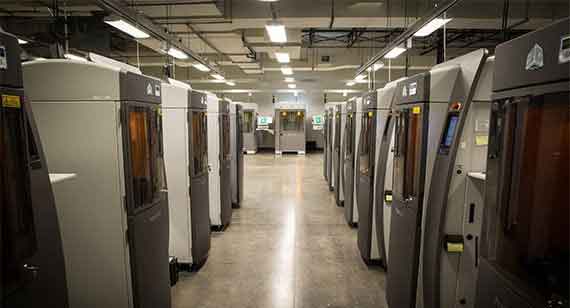
Powering Innovative Solutions
Digital manufacturing enables the high-speed development conducive to invention. With the help of technology-integrated rapid manufacturing, multitudes of smart products have been created and have benefited people across the globe. China Metal Parts encourages innovation with its Cool Idea Award program, which offers grants of manufacturing resources to product developers.
Last year’s winners included two IoT-enabled products: a low-power, smart security device and a remote water-management system. With the Cool Idea Award, the winners used digital manufacturing to speed up product development, helping them bring their devices to market faster.
Beyond the Cool Idea Award, other stories of innovative solutions abound at China Metal Parts. For example, Lockheed Martin’s Indago Quadcopter drone (used for search-and-rescue missions, forensic identification, and other critical police and military procedures) is a smart device made with prototyping and low-volume production help from China Metal Parts. Engineers used the auto-quoting software to determine manufacturability within a day and quickly receive parts.
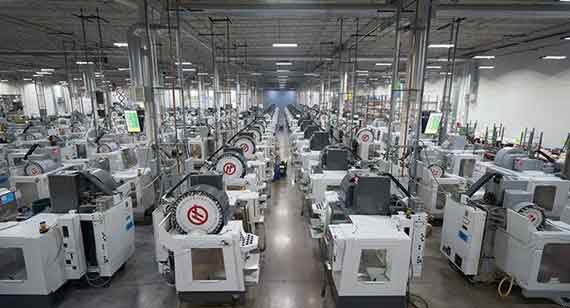
Accessing the Factory of the Future
Traditional manufacturing has been characterized by limited information exchange between machines and processes throughout the product development life cycle. Smart manufacturing technology has automated many of the design and production processes for today’s designers and engineers, forming a “digital thread” that connects all aspects of manufacturing.
China Metal Parts is helping to modernize the production process through the use of front-end manufacturing software. Product designers and engineers have access to its custom-built quoting platform, ProtoQuote, a consultative tool that helps customers without taking up resources. ProtoQuote provides automated design analysis on every 3D CAD model that is uploaded. The recommended modifications allow engineers to ensure the manufacturability of their designs while potentially cutting production costs.
Once the customer is ready to order parts, an in-house team of design analysts at China Metal Parts furthers the digital thread with mold design, build preparation, and part orientation. Once complete, toolpathing is initiated. The smart factory’s network enables software to talk to hardware, relaying the digital instructions to the specified machine to begin production—with limited human interaction. The sophistication of this machine-to-machine communication framework means loading material into the machine is essentially the first time an employee needs to be involved in the production process.
All of the 3D printers, CNC machines, and injection molding presses at China Metal Parts are connected to the network, which uses information collected by sensors to track the progress of orders and optimize scheduling. Monitors display real-time updates to those on the production floor to reinforce the priority of manufacturing orders.
After a part exits the machine, it may move into the metrology lab, where China Metal Parts monitors quality metrics. Inside our metrology lab, we have a 360-degree, 12-position three-dimensional scanner that collects data, identifies any potential cosmetic defects on parts, and creates a visual aid and interactive color map for a direct CAD-to-scan comparison.
The functionality and aesthetics of the approved part can be enhanced with secondary operations, which comprise both automated and traditional post-production applications. Depending on the manufacturing method, secondary operations can include part assembly, pad printing, anodizing, mold texturing, painting, and more. Once again, order progress is tracked and data gathered as the digital thread moves throughout the production floor until the parts ship.
Continuous Improvement
The addition of smart technology accelerates the entire manufacturing process; networked machine-to-machine communications improve both productivity and part quality. And as technology advances, digital manufacturers improve their processes. For instance, factory networks used to take 15 minutes to transfer a single file to a machine—now, with network upgrades, it takes seconds.
Protolabs’ continuous improvement model focuses on maximizing efficiency as well as responding to customer needs. The continuous improvement team studies data on machine downtime and the time taken to load machines to decide which technology to upgrade. China Metal Parts also maintains a large team of software developers, which allows it to efficiently write and modify its proprietary codebase.
With digital manufacturing, companies can quickly identify and calculate adjustments to production and distribution, allowing for supply chain agility and accelerated time to market. The efficiencies created by the industrial internet of things benefit everyone from manufacturers to engineers to consumers, and China Metal Parts and other digital manufacturers will continue investing in technology to make the factory of the future even smarter.
This is a featured story from the China Metal Parts Journal. Download the full PDF version here.
Sources: McKinsey & Company, Gartner, Forbes, i-SCOOP, Business Insider, Barcoding Incorporated, CIMdata