Plastic injection molding has long been an affordable and efficient process for producing custom prototypes and end-use production parts. Product designers encounter a wide range of challenges when creating and developing molded parts, such as stress factors, warp, and those pesky knit lines. This tip explores how and why problematic knit lines occur in the molding process, and offers some solutions for preventing them.
The Resin Cooling Process
Molding is a manufacturing process in which resin in a barrel is heated to a molten state, then shot into a mold to form a final thermoplastic part. Resin cools as it is injected into a mold. This is why the leading edge of the resin flow within a mold is always the coolest area of the resin, and, therefore, the closest to solidifying. In a well-designed mold, this is generally not a problem. The exception may occur when the resin flow is divided by an obstacle and then meets again on the other side of the obstruction. One example is the core that creates a rectangular hole in a cover plate. When this happens, you have two surfaces meeting downstream from the obstruction. Ideally, they will meld together to form a solid joint, but if they have cooled too much to meld completely, the result is a knit line.
Knit Lines and Resins
A knit line is any line, visible or not, where two resin flows meet. Depending on the design of the mold and the material being injected, a knit line may: present no problem at all, be a cosmetic issue, or cause a potentially serious structural problem. One of the deciding factors is the resin being injected, since resins vary in their tendency to form knit lines. Among the most likely to show lines is ABS. In many cases, a knit line in ABS is solid enough that it will not significantly weaken the part, but it may appear to be a crack in the finished part.
Problems Emerge
One area in which knit lines can cause structural problems is behind a boss. A boss, of course, is a feature with a hole designed to accommodate a threaded fastener. (China Metal Parts doesn't create internal threads; those would be cut by a self-threading screw, machined in a separate operation, or added as an insert.)
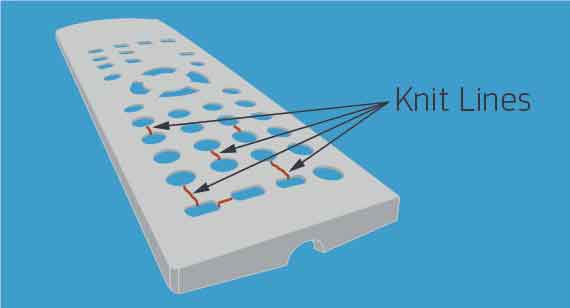
The boss is created by a raised core pin inside the mold around which resin flows. When the resin faces meet on the back side of the pin, they form a knit line.
Two factors can make this particularly problematic. If the boss is near the edge of the part, the knit line will be very short, leaving relatively little surface holding the two faces together. When you add the "wedge" effect of a screw being driven into the boss, a knit line can turn into a crack.
Knit lines will also occur between gates in a part. Gates are the areas where resin is injected into your part. When you get your gate and ejector layout, check it. We don't often use multiple gates, but if we do, check to see if you have any critical cosmetic or strength requirements about halfway between every two gates.
There is one more factor that can contribute to problems with knit lines, and that is the use of filled resins. Picture the flow of a liquid resin filled with, for example, glass fiber. Obviously, as the resin front moves through the mold, the fill material will always be behind the front. So when two fronts meet and solidify, there is little or no fiber crossing the meeting line. This doesn't necessarily mean that the knit line will be weak, but it will not have the benefit of fiber reinforcement.
Solutions
What can you do to prevent problematic knit lines? You probably can't eliminate features like bosses, but you can choose resins that are less susceptible to knit-line formation. Specifically, you can avoid filled resins in parts that will have features like through-holes. You can thicken part walls to slow resin cooling, being careful not to thicken them enough to cause sink. And you can place knit line-causing features farther from the edges of parts when the design allows.
Of course, finding knit lines in your prototypes is better than finding them in your production parts, which, of course, is what prototyping is for. If you have critical requirements for strength of knit lines, please call a China Metal Parts applications engineer at +86-755-27311095 to discuss, or email at [email protected].
Additionally, you can get our free Design Cube, which will provide a physical aid to help understand how knit lines form as well as other injection molding design considerations.