When you design a part, much of its functionality will depend on obvious factors like its shape, size, wall thicknesses, locations of connection points, and so on. Less obvious but equally important will be the characteristics of the material from which it is molded, machined, 3D printed, or fabricated (cut, bent, shaped, etc.).
Design is done at the macro level; material properties are generally controlled at the molecular level. The earlier in the design process you start thinking about materials and their properties, the more effective and economical your finished design will be. This tip is intended to help you with that early evaluation. It offers an overview of the four general categories of material properties (metals and plastics), some major considerations to keep in mind when selecting materials for your next part design, and some frequently overlooked design issues to consider.
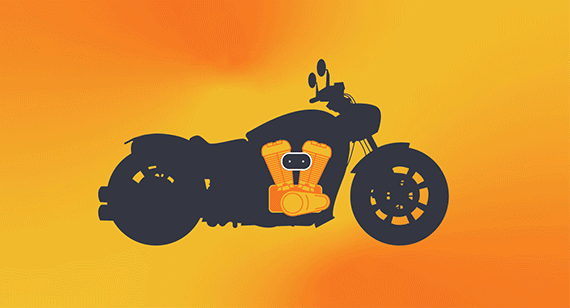
Why Material Choice Matters
Material choice—whether metal or plastic—can be simple, almost incidental, or complex and critical to a part’s performance. Say, for example, you want to produce a case for a device designed for indoor use. A large percentage of plastic shells aren’t particularly thermally or electrically challenged, don’t have extreme mechanical requirements, and so can function in relatively benign environments such as your family room. The majority of such parts can be made from ABS, polycarbonate (PC), or an ABS/PC blend.
On the other hand, consider the housing for a motorcycle’s air cleaner. This will need to be opened and closed periodically for filter replacement. As part of that function it may employ a living hinge or integrated spring clip. It will have to tolerate assault by flying debris, heat from the engine, UV radiation from the sun, moisture from a variety of sources, and chemical exposure from both fuel and cleaning chemicals. Finding the right material for this application will probably take both research and iterative prototyping.
The components of a smartphone could be even more challenging. Their functions could include both dissipation of and protection from heat, electrical insulation, selective passage and blocking of wireless signals, and for its casing, protection against repeated drops. Each component of this complicated design has very specific requirements and those, in turn, require specific material properties. Accordingly, material choice matters.
Effective material choice begins with a clear understanding of the function(s) of the complete device or assembly. Next you must identify the functions of the particular part in the overall operation. Where there are multiple considerations, you’ll want to prioritize, separating the “must haves” from the “nice to haves.” For example, a smooth cosmetic finish that is a “must have” in a handheld device might be a secondary consideration where the strength of a glass-fill material is needed to meet strength requirements. The list of possible considerations is long, but will typically fall into these four categories: mechanical, physical, thermal, and electrical material properties.
Navigating Material Properties
Mechanical
Mechanical properties are those that a material exhibits upon the application of various forces. These include traits such as tensile and compressive strength, flexibility, and hardness.
For Plastics. The mechanical properties of plastics vary greatly from the flexibility of polypropylene for a living hinge to the rigidity of glass-filled nylon.
For Metals. In contrast, metals are all relatively rigid. Various types of steel will be stiffer, for example, than aluminum.
Physical
Physical properties are a material’s cosmetic characteristics and its response to chemicals or radiation. These include density and resistance to chemical corrosion and UV breakdown. They can also include cosmetic issues like color and surface texture.
For Plastics. Physical properties of plastics will vary widely. Urethanes, for example, may be a poor choice for moist environments, while 3D-printed plastics produced by stereolithography will become brittle if exposed to UV light.
For Metals. Similarly, metals will vary in their tolerance for chemical exposure. Among metals, stainless steel will be an obvious choice for many potentially corrosive environments, but will come up short in other areas such as heat transfer.
Examples of Commonly Used Materials |
---|
|
Thermal
Thermal properties are those that govern a material’s response to temperature. Are they likely to be weakened or deformed by exposure to heat or to become brittle in response to cold? Does the material conduct heat readily or insulate? Temperatures affecting the part can be either environmental or can be generated by the assembly in which the part operates.
For Plastics. Thermal response can be a major issue in choosing plastics. While silicone is ideal for ovenware, many plastics can be damaged by the heat of a closed car on a summer day.
For Metals. While metals can generally tolerate higher heat than many plastics, a nickel chromium “superalloy” like Inconel can tolerate temperatures up to 1,300 degrees F, making it suitable for rocket engine parts. In less demanding roles, aluminum can be the ideal material for a heat sink, while stainless steel would not.
Electrical
Electrical properties address characteristics such as conductivity, resistance, and inductance.
For Plastics. Electrical properties of plastics vary widely. This can be critical in compact devices like smartphones, in which current and signal must be isolated to prevent distortion or in medical devices in which strong currents or magnetic fields are used for diagnostics or treatment.
For Metals. Similarly, conductivity varies widely among metals. Copper is generally our first choice for conductivity, but aluminum offers good conductivity while reducing cost and improving resistance to corrosion if conductivity is not critical.
Frequently Overlooked Material Considerations
A lot of designers have a few “go-to” materials they use unless those have obvious shortcomings. This is fine if the material meets the need and the price is right. But in some cases you might be giving up benefits that you could turn up with a bit of research. Or you might discover problems in a prototype that would have turned up in a properties search, slowing your development process. Or maybe you could meet the needs at a lower price, which could really add up over a longer production run. Here are some examples:
- You might think heat or UV damage are irrelevant in a product designed for indoor use. But what happens if it’s left out in the sun or in a closed car?
- Have you anticipated all forms of chemical exposure? Your small print may warn against certain chemicals, but a more resilient material can prevent user dissatisfaction.
- Have you considered all field conditions? An automotive component may be protected from UV under the hood, but has to deal with accumulated heat, while a similar motorcycle part may face exactly opposite conditions.
- How well will the component age? Is it disposable? Replaceable? Permanent?
- Is density a consideration? Some moving parts may benefit from lightness, while others need weight to function properly.
- Size and strength can be interchangeable. A thinner part made of a stronger material may save space. Using less material could make up for higher cost per unit of volume.
- Finish isn’t just a cosmetic issue. Factors like texture can be critical to ergonomics.
- The right material can help resolve design issues. For example, built-in spring clips or living hinges can eliminate the need for connectors.
- Heat can be a problem in many products. A well-designed heatsink made of the right metal or plastic can effectively move heat away from critical areas.
Want More Material Resources? |
---|
We offer hundreds of different materials for molding, sheet metal fabrication, machining, and 3D printing. Luckily, we have a materials comparison guide and a series of free, pocket-sized material selectors. There are also a number of other resources available including:
Of course, research is only a first step, best backed up by prototyping and testing to identify the best and most economical solutions for your needs. |
For additional help, feel free to contact us at +86-755-27311095 or [email protected]. To get your next design project started today, simply upload a 3D CAD model for an interactive quote within hours.