Over the past three decades, 3D printing has developed a reputation as an essential manufacturing process for prototype parts. Create a CAD model of your design, send it to your company’s printer, and a 3D replica will be ready in hours. Yet these parts are often little more than conceptual show-and-tell models, not durable enough for long-term use, and in some cases prone to degradation by sunlight.
The winds of manufacturing are beginning to shift, however, and industrial-grade 3D printing, or additive manufacturing, is now encroaching on machining, injection molding, and other conventional manufacturing processes. This white paper explores the new and existing technology leaders in this area, and assesses the capabilities of production for each 3D printing process.
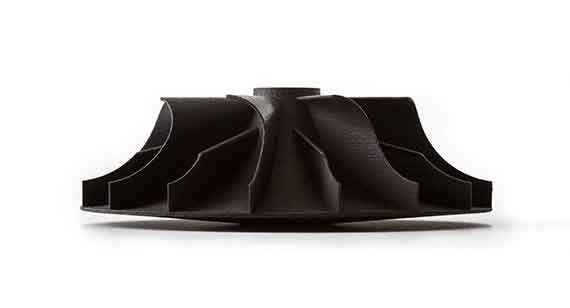
The Case for 3D-Printed Production Parts
Defining what is meant by production is an important first step. In a typical manufacturing scenario, prototype parts are produced for form, fit, and some function testing, and then either CNC machined or injection molded until quantities grow high enough to merit investment in high-volume production tooling. Production 3D printing shortcuts that process. Depending on the part and its intended use, it is oftentimes possible to print parts that will perform every bit as well (and in some cases better) than conventionally produced parts, and do so cost-effectively enough that downstream investment is delayed or even unnecessary.
One notable example is GE Aviation’s use of 3D-printed fuel nozzles in its LEAP engine, a move that saves aircraft owners roughly $3 million per plane annually. In the medical space, Johnson and Johnson is one of many suppliers using 3D printing for customized surgical tools and patient-specific implants, providing a better outcome for patient and surgeon alike. Oreck leveraged 3D printing to reduce the cost of its vacuum cleaner assembly pallets by 65 percent. Audio manufacturer Soundz used it to reduce tweeter grill lead-times from months to days. BMW used it to reduce the weight of handheld assembly tools by 72 percent. Without 3D printing, all of these parts would have required lengthy, expensive machining or injection molding operations to produce.
Granted, 3D printing cannot compete with high-volume production methods in the majority of applications, and probably won’t for some time to come. However, it’s important to note the willingness of these and literally thousands of other companies to embrace additive manufacturing technology for what it is—an effective way to produce precision components, which are often as capable as their machined or injection-molded counterparts when it comes to manufacturing end-use production parts.
Comparing 3D Printing Technology
Much of this is made possible by a handful of 3D printing technologies, all of which can be grouped according to the types of materials they can use. Here’s a short overview of each.
PLASTIC PRODUCTION
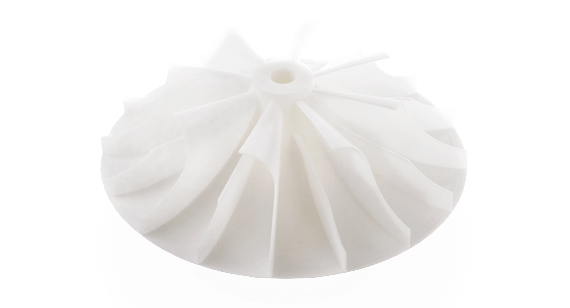
Selective laser sintering (SLS) is a powder bed printing technology. It uses a laser to fuse tiny bits of nylon powder, tracing the geometry of digitally sliced CAD models layer by layer and working from the bottom of the part upwards. After each layer is complete, a roller spreads fresh material across the top of the bed and the process continues until the part (or multi-part assembly) is complete. After a quick brushing to remove excess powder and a light bead blast, parts are ready for end-use; although a range of finishing processes are possible. Because nylon is a durable, multipurpose material, and because the entire volume of the heated powder bed can be used to build parts, SLS is a favorite of many designers for production of end-use mechanical components and commercial products in low-volume quantities.
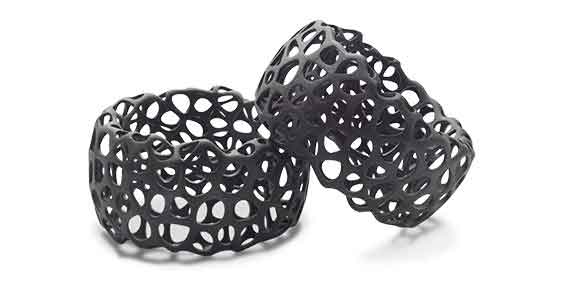
Multi Jet Fusion (MJF) is a relatively new 3D printing technology launched by HP. It is similar to SLS in that it uses a powder bed and is currently limited to nylon polymers, although additional materials will almost certainly become available as the technology advances. There is no need for support material, post-processing is minimal, and the entire print chamber can be used to build parts. Instead of a laser, however, MJF employs an inkjet array to deposit fusing and detailing agents across the print layer, and an infrared heating element used to fuse them. The finished parts offer more consistent isotropic integrity than is possible with SLS, and because the entire bed is covered in each print pass (similar to a laser jet printer) build speed is predicated on the number of layers needed to build a part or batch of parts rather than on surface area.
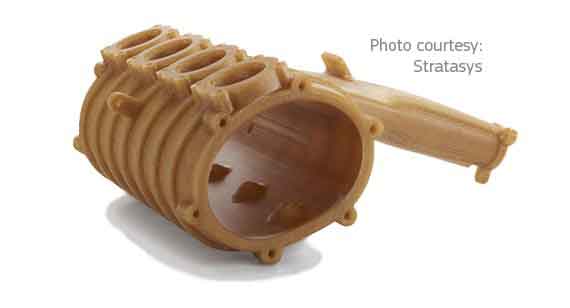
Fused deposition modeling (FDM) uses a fishing reel-like filament of heated thermoplastic, depositing it in ultra-fine, side-by-side beads. Here again, parts are built one layer at a time, starting at the bottom. FDM prints its own scaffolding during the build process to support the workpiece, but these structures are easily dissolved in detergent and water once the part has been removed from the printer, after which the part is ready for use. A variety of commercial-grade materials such as ABS, nylon, polycarbonate, and PEI (Ultem) are available, and FDM can print multiple colors and even multiple parts within a single build.
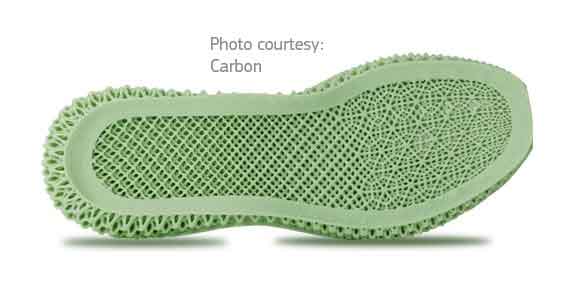
Carbon is a newcomer to 3D printing and builds from the top down. It also builds parts “sans layers,” using a proprietary technology known as CLIP (continuous liquid interface production), which projects a continuous sequence of part images into a UV-curable resin bath and literally “grows” the part in one fluid motion. When done, the parts are washed and then baked in an oven, triggering a chemical reaction that strengthens and cures the resin. Build speeds are substantially faster than competing processes (some say 100 times that of stereolithography). In addition, the UV light used to cure the resin is programmable, allowing users to tune material properties on the fly. For example, Carbon’s polyurethane-like family of polymers can be made flexible like polypropylene, rigid like ABS, or elastomeric like thermoplastic olefin (TPO). The resulting parts can be used for production applications ranging from springs and gaskets to dental implants and manufacturing jigs.
METAL PRODUCTION
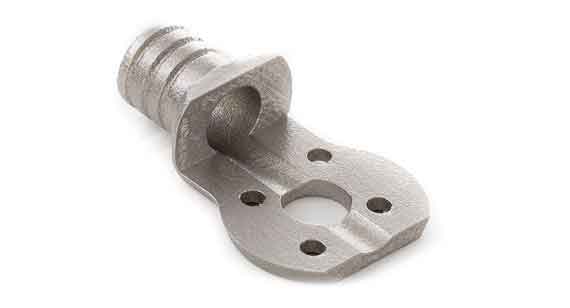
Direct metal laser sintering (DMLS) is another powder bed printing technology. It uses a laser to fuse aluminum, cobalt chrome, stainless steel, titanium, and other powdered alloys into fully dense metal parts, “drawing” them layer by layer from the bottom up. Because of the stresses built up during extreme temperatures involved (rapid heating and cooling), support structures are required during the build process to keep parts from curling or warping. When complete, parts must be heat-treated to remove residual stresses, after which the supports can be removed by machining or hand grinding. The GE fuel nozzles mentioned earlier are made using DMLS, as are an array of equally complex aerospace and end-use medical parts.
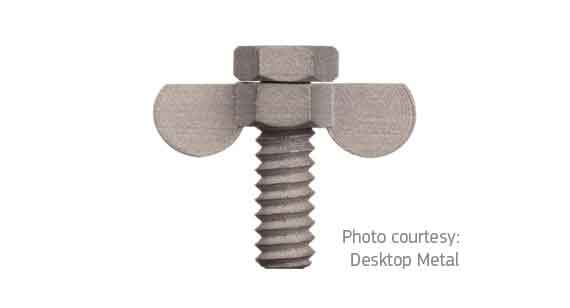
Desktop Metal (DM) is another newcomer to the 3D printing arena and offers two distinctly different, though complementary, metal printing technologies. Both boast of faster build rates than laser-based metal printers, as well as a wider array of alloys, and are geared toward higher production volumes. The two systems are:
- The studio system uses a process analogous to that of FDM, heating and then extruding rods made of powdered metal mixed with a polymer binder. When complete, the green parts are placed into a solvent for “debinding,” removing a portion of the polymer and preparing the now “brown” parts for a subsequent trip to a 2,500-degree furnace. This fuses the individual metal particles one to another in a manner similar to metal injection molding (MIM). The result is a part nearly as dense as one that has been laser fused but without the accompanying thermal effects (or need for build supports), and suitable for most end-use applications.
- The production system is currently in beta testing and will not be released until late 2018. Its parts will share many of the same attributes as those printed with the studio system, except that it uses a process known as single pass jetting (SPJ) and promises even faster build speeds. There’s no need for debinding and brown parts can go straight into the sintering furnace. It also provides for full “nesting” of the build chamber, meaning many parts can be built in a single print job. And, as with the studio system, the support structures are easily removed—no secondary processing is required unless greater accuracy or finer finishes are required than that provided by the printer—an advantage in a production environment.
Each of these 3D printing technologies comes with its own set of rules, including design guidelines, accuracy and part-size considerations, surface finish and resolution capabilities, material selection, mechanical properties, and more. Those contemplating using 3D printing for end-use production, or as a substitute for traditional low-volume manufacturing, should take a close look at each technology, starting with the available materials followed by part cost and function. Of course, the success of any 3D printing project depends heavily on the part design, even more so than with injection-molded or machined parts.
Here is a comparison chart to get started, although all specifications should be verified with the specific technology supplier or 3D printing partner before making any final decisions on your project:
Available Materials | Max. Part Size | Min. Feature Size | Layer Thickness | Expected Tolerance | |
---|---|---|---|---|---|
Direct Metal Laser Sintering | Many commonly used metals and super alloys | 9.68 in. x 9.68 in. x 10.8 in. (245.87mm x 245.87mm x 274.32mm) | 0.006 in. (0.152mm) in high-res. mode | 0.0008 in. (0.02mm) in high-res. mode | +/- 0.003 in. (0.076mm) |
Desktop Metal Studio | 200+ metal alloys | 10 in. x 6.7 in. x 6.7 in. (255mm x 170mm x 170mm) post-shrink | N/A | 0.0012 in. (0.05mm) | N/A |
Desktop Metal Production | 200+ metal alloys | 13 in. x 13 in. x 13 in. (330mm x 330mm x 330mm) build area | N/A | N/A | N/A |
Selective Laser Sintering | Nylon-like PA850, PA650, filled nylon, and TPU | 19 in. x 19 in. x 22 in. (482mm x 482mm x 558mm) | 0.030 in. (0.76mm) | 0.004 in. (0.102mm) | +/- 0.003 in. (0.076mm) plus 0.001 in./in. |
Fused Desposition Modeling | Similar to ABS, nylon, PC, PPSF, Ultem, and others |
36 in. x 24 in. x 36 in. (914.4mm x 609.6mm x 914.4 mm) |
0.019 in. (0.48mm) | 0.007 in. (0.178mm) to 0.020 in. (0.508mm), depending on material | +/- 0.0035 in. or +/-0.0015 in. per in. (+/- 0.089mm or +/- 0.0015mm per mm), whichever is greater |
Multi Jet Fusion | Nylon-like PA650 (Nylon 12) | 11.1 in. x 14.9 in. x 14.9 in. (284mm x 380mm x 380mm) | 0.020 in. (0.5mm) | 0.003 in. (0.076mm) | +/- 0.004 in. (0.102mm) plus 0.001 in./in. |
Carbon |
Similar to ABS, polypropylene, TPO, glass-filled nylon, SLA resin | 7.4 in. x 4.6 in. x 12.8 in. (189mm x 118mm x 326mm) | Varies by material, but 0.004 in. (0.1mm) possible | N/A | Depends on material and part geometry, but assume 0.2% +/- 0.01 in. (0.3mm) of feature size |
Making Metal
As GE has clearly demonstrated with its 3D-printed fuel nozzles, DMLS is eminently capable of producing high-quality, end-use production parts in metal, even in large volumes. In addition, until Desktop Metal arrived, DMLS and comparable laser-based printing technologies were the only tech in town. Unfortunately, DMLS does suffer some drawbacks. The machines are expensive—spending a million dollars or more on a system isn’t unusual—so a low-volume part supplier is often used by product developers, designers, and engineers versus in-house 3D printing. Because DMLS-printed parts need support structures, a visit to the machine shop or grinding department for post-printing removal is required. So, too, is heat treating, to relieve the stresses induced during printing. Still, aerospace and medical companies alike have embraced DMLS in ways that few thought possible even a decade ago. The parts produced sit at the upper end of the 3D-printed cost spectrum, but this is easily offset by lower assembly part counts, lighter weight yet stronger products, and “unmanufacturable” part designs never before possible.
This is where Desktop Metal (DM) comes in. Regardless of platform, the process is similar in capability and product integrity to the decades-old metal injection molding (MIM) process. The big difference is that DM requires no mold or other tooling like MIM. This increases flexibility, shortens lead time and, on lower part quantities (say anything under 1,000 pieces, depending on part complexity), reduces part cost. DM’s studio machines are a small fraction of a DMLS system, and DM’s production printers are expected to be far less expensive as well. When you consider the reportedly accelerated printing speeds and the fact that no support structures are needed during the build process, Desktop Metal has a lot of potential to disrupt the metal 3D printing industry.
However, DM parts shrink—albeit predictably—during the curing process. Based on part geometry and material, this arguably means they will not be as accurate as DMLS parts, ever. Plus, it took many years for the metals used with DMLS to pass muster for use in aircraft and human bodies. Because DM leverages the same well-understood metals used with MIM, the certification road should be much shorter, but it must be traveled nonetheless. Part designers must take all this and more into consideration before jumping onto the Desktop Metal bandwagon.
Polymer Potential
Similar arguments can be made for and against the various polymer-based 3D printing technologies. For example, SLS produces very accurate parts with fine features and no need for build supports, but is limited to nylon-like materials and TPU (thermoplastic polyurethane). MJF is more accurate (except on very small part features), is significantly faster, and has more consistent isotropic (Z-axis) strength, yet offers fewer material options (for now, just unfilled Nylon 12). Both processes also allow filling of the entire build chamber, an important point where large numbers of parts are needed. Either way, if you’re looking for production parts where nylon will do (which covers many requirements), both technologies are a solid option.
FDM machines offer a greater number of material options than SLS and MJF combined. It’s not quite as accurate, however, and surface finishes are a bit “stringy,” keeping it firmly in the prototyping and low-volume part-making realm (although it remains the king of size, with build chambers large enough for a suitcase). Then comes Carbon. It can handle just as many polymers as FDM, and promises to build parts up to 100 times faster. Its accuracy is also quite good, and since there are no layers, surface finish is better. For many production parts, this is an excellent compromise, especially in light of its greater speed.
In any event, the advantage of 3D printing is this: It’s very easy for designers to test the waters by sending their part designs out for prototyping, determine which process provides the best combination of price, accuracy, and material, and then easily segue into 3D printing production if that makes the most sense. Just be sure the math still works as part volumes increase, and that your part design is manufacturable using traditional processes—too many designers paint themselves into a 3D-printed corner, and end up paying dearly in redesigns and development time to get themselves out.
Traditional Thinking
Speaking of part volumes, what’s wrong with injection molding? Absolutely nothing. A number of suppliers offer rapid injection molding services that allow for economic part production at virtually any quantity. The same can be said for machining services. Chances are good that if a metal part is easily and cost-effectively made on a CNC lathe or milling center, it’s probably not a good candidate for DMLS or Desktop Metal. Remember, complexity is free with 3D printing. Not so with injection molding, machining, casting, and other traditional manufacturing processes, where complex part designs make production costs skyrocket.
Ironically, one of the biggest costs in 3D printing (aside from the price tag of many 3D printing machines), is the raw material itself. Most industry experts agree, however, that metal powder supply and demand is undergoing a sea change as 3D printing becomes more popular and an ever-increasing number of big name suppliers get on board. The same holds true for polymers, although probably to a lesser extent thanks to the relative maturity of the resin-based 3D printing industry. As companies such as BASF, Dow Chemical, HP, and others fight for market share of plastic and metal supplies alike, it can only spell lower prices for consumers of 3D-printed products.
Special thanks to Carbon and Go Engineer for input on this white paper.