Strategic management of the supply chain is a critical component of product development and life cycle planning, as well as a necessary element for risk mitigation. Leading companies no longer treat it as a tactical cost center that is purely an operational concern, but rather a cross-functional initiative geared towards building capabilities that will enable growth and minimize risk. Supply chain management must allow the corporation to be nimble and responsive to newly encountered opportunities and adversities throughout the product’s life cycle.
Top performing companies are establishing manufacturing supply chain safeguards by partnering with rapid response contract manufacturers in order to mitigate the risks associated with production or shipment delays, and unforeseen swings in demand during multiple stages of the product’s life cycle. While cost reductions and productivity increases remain important, executive management must also focus on growth.
In a 2013 survey conducted by BCG Perspectives1, respondents cited growth initiatives through corporate activities, such as product line expansions that address global markets and niche market product segmentation as top concerns. Furthermore, 77 percent of senior executives cited innovation and product development as one of their top three strategic priorities.
Competitively priced injection molding enables cost-effective short runs so product developers have more time to react with shorter lead times. The surveys also report a myriad of risks that threaten growth as well as the health of the corporation. The top threats cited were:
- shortening product life cycles
- supply chain disruption and cost structure shifts due to offshoring
- disruptive technologies and innovations
- differentiation amongst competitive offerings
- unanticipated competitors
- globalization
Clearly, the core challenge is to target growth while mitigating these, and other risks. According to PWC in a 2014 U.S. CEO survey2, the strategy is to “…build capabilities that can respond quickly to opportunities while keeping a handle on costs and risks.”
What is needed is responsiveness and nimbleness that can simultaneously react to growth opportunities while mitigating threats. Such a culture armed with the right tools can be both proactive to move ahead of the competition and immediately reactive to any threats to growth. When employed, companies can realize growth in both the top and bottom lines.
Strategic Importance of Supply Chain Safeguards
Supply chain management has evolved into a strategic tool for growth and profitability and an integral component for risk mitigation. As such, there is an obligation to build manufacturing supply chain safeguards that will prevent disruptions or enable recovery from challenges while capitalizing on opportunities. These initiatives accelerate time to market and provide quick response to the endless changes, threats, and opportunities.
Aggressive time-to-market schedules depend on the reliable delivery of goods and services. Cutting days or weeks from “normal” lead times when using conventional approaches eliminates any cushion along the critical path, which leads to direct transfers of delays to the next step in the process.
Inevitably, delays and problems will arise and should be anticipated. A strategic, proactive approach is to establish safeguards within the supply chain that act as shock absorbers. The supply chain safeguards absorb the impact of a delay, stopping the downstream cascade, or provide a time cushion for subsequent processes.
The Bottom Line
The manufacturing supply chain safeguards preserve and accelerate the timeline while allowing for opportunities to improve product and process quality. The strategic use of safeguards ensures a steady supply of product in line with target delivery dates. Partnering with suppliers that leverage technology and process excellence to expedite responses and deliveries is crucial in the successful implementation of supply chain safeguards.
Identifying Opportunities
The need for manufacturing supply chain safeguards vary by company, product type and product maturity. They also vary at the component level. The key is to ensure that critical-path processes for critical-path components are identified and the appropriate safeguards are established.
For new or revised products, safeguards are needed from the design phase through commercialization. For established products, safeguards extend from market introduction into the end-of-life phase.
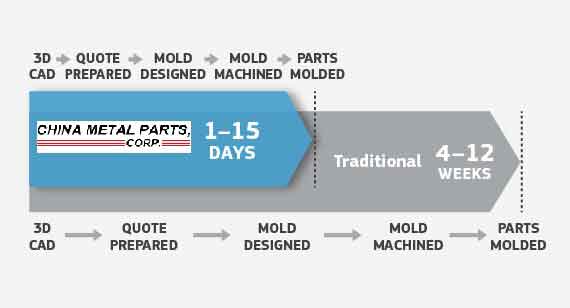
As a product progresses through the life cycle, lead times lengthen, and risks become more impactful. Therefore, manufacturing safeguards become increasingly important as a product moves from design into market launch. Following are examples of manufacturing safeguards and their impact:
Request for Quote
At every stage in the product life cycle, there is the non-value-added task of requesting and receiving quotations from suppliers. Collectively, this activity can add up to weeks or months of delays across multiple parts in an assembly. Additional delays may unexpectedly arise if project issues are not identified during the quotation process. For example, if design for manufacturability (DFM) issues are discovered only when an order is initiated, the response is to regroup, redesign and re-quote the project, which creates significant delays.
Alternative
Through the use of complex software code and automated manufacturing equipment, interactive online quotes with manufacturability analysis are now made possible within hours by best-in-class contract manufacturers. These sophisticated online quoting programs will report and illustrate design issues that can impact quality, cost, and time to market.
Advantage
Days, even weeks, saved during the design phase can accumulate to a month or more over the entire project. When design for manufacturability feedback is incorporated during the early phase of design, the path to a validation and testing is shortened by weeks, sometimes months. Furthermore, early DFM feedback reduces the risk of rework and its associated costs.
Product Development
Throughout the product development process, models and prototypes are required for form, fit, and functional testing. These physical representations are invaluable in the discovery of flaws that impact product performance, manufacturability, and production costs. While vital in the process, a model or prototype, when produced by conventional means, may require weeks to deliver. Since there may be several design and prototyping cycles, the cumulative impact on the timeline may be months.
Alternative
3D printing expedites delivery of models and prototypes. Used in lieu of, or in conjunction with, conventional manufacturing practices, 3D printing may reduce lead times by 50 to 80 percent. Additionally, additive manufacturing proves to be an efficient process with little demands in terms of time or effort on the front end of the process. However, it yields parts with somewhat different physical characteristics and design constraints than those parts made using traditional manufacturing processes.
When seeking to evaluate product design with prototypes produced using the same methods as those for production, there are suppliers that specialize in rapid manufacturing using conventional methods, such as CNC machining and injection molding. Although the manufacturing process is unchanged, process optimization through automation leads to much shorter lead times. For example, an order of 500 injection-molded prototypes, which can take months to deliver, can be made available in 7 to 10 days using China Metal Parts’ rapid injection molding services.
Advantage
In attempts to keep projects on schedule, companies are often tempted to avoid prototyping or reduce the number of prototype revisions. While this may have an immediate benefit, design issues that are undetected may significantly delay manufacturing when discovered during the production process. By leveraging expedited processes, companies can execute prototype evaluations without inducing delays during the product development process, which protects from even larger delays during the production phase.
Relative to traditional prototyping lead times, the accelerated delivery provides a time cushion that may be used to absorb upstream delays. Accelerated delivery also offers a responsiveness that allows execution of multiple design revisions to fine tune product designs for quality, performance and manufacturing costs, which protects against late-term issue identification that can lead to costly delays and rework.
Pilot Production
Pilot production is essentially a “soft launch” used to evaluate and fine tune products and processes. Usually consisting of 1,000 to 5,000 units, pilot production offers products that manufacturing, product management, marketing and sales can use for trials, evaluations and test marketing.
Alternative
The demands for pilot product lie between those of prototypes and production. While ideal to match all characteristics of production products, close approximations are often acceptable. This latitude allows the substitution of processes to accelerate delivery while keeping costs at a minimum. For example, CNC machining or 3D printing may be used for parts that will ultimately be injection molded.
Another alternative is to simplify the production process. If, for example, parts will be injection molded, aluminum molds may possibly be used to manufacture the entire pilot production order. Soft tooling made from aluminum is produced for a fraction of the cost and at a fraction of the time of steel molds.
Advantage
Pilot production defers the investment in production equipment, including tooling, while accelerating the delivery of production-grade products. This allows a thorough analysis prior to investing in capital or operational assets that may be challenging and expensive to adjust, modify or replace.
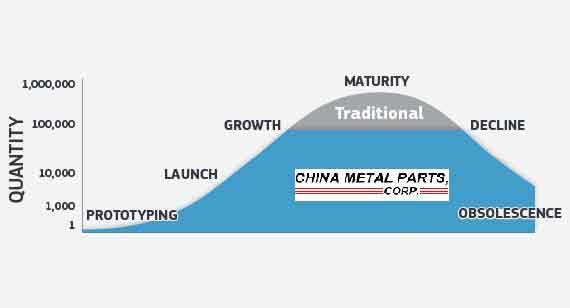
Bridge to Production
The goal is to accelerate the delivery of parts while maintaining the quality of production products. In a sense, bridge-to-production manufacturing is a stopgap solution that mitigates the impact of long lead times for production orders.
Bridge-to-production processes run concurrently with production orders. The intent is to deliver production-grade parts while production tooling and processes are in development, thereby getting you to market sooner.
Alternative
Bridge-to-production solutions are enacted when the delivery of production orders will extend beyond planned timeframes for product delivery. As a safeguard, they are placed in service when upstream processes impart a delay on production order launch; production lead times are unexpectedly long; or production problems are encountered, causing delays.
Ideally, the same process as that for production will be used, which yields identical quality parameters as the production method, but with modified assets. For example, one option is short-run, “soft” tooling that minimizes complexity and expedites construction to reduce lead times. In this case, the tooling may exclude high-end automation and cycle-time acceleration features that are less beneficial for lower production quantities in order to reduce delivery time and total investment.
Advantage
Bridge-to-production suppliers, due to their rapid response, are capable of absorbing upstream delays or unanticipated production delays to preserve delivery schedules. By producing the quantity of parts needed for the duration of the delay, companies preserve production schedules.
For example, if projections are for 10,000 units per week upon initial launch and the delay is four weeks, the bridge process would be expected to delivery 40,000 units. After that, production processes would engage to deliver the bulk of the projected demand.
Another advantage is that bridge solutions offer an alternative when faced with the hard decision to proceed with known issues or repair the issues while suffering a delay. This is an all-too-common situation that arises if inadequate evaluation is completed during product development. For example, if a design flaw or design-for-manufacturability issue is discovered late in the process, tooling rework may be suggested. Rather than bear the profit consequences of an inferior product or accept a costly delay, enact the bridge solution to allow modifications to the production tooling without experiencing delays.
Conclusion
As shown by the four scenarios, within a growth-oriented organization, manufacturing safeguards provide the mechanisms to prevent disruptions or recover from challenges while capitalizing on opportunities. With fast, responsive processes that reduce or eliminate non-value added time, the manufacturing safeguards absorb delays and transfer time gains forward to cushion the impact of downstream interruptions.
The utilization of manufacturing safeguards also promotes thorough product evaluations to prevent unforeseen problems that will cause delays in delivering products to market. Early problem detection also preserves resources that would otherwise be consumed when responding to a supply chain disruption on the critical path. When new product opportunities arise, these nimble and responsive processes are also the key tools for delivering more new products to market.
Manufacturing safeguards are a key element of a strategic supply chain initiative that mitigates the risks of disruptions, threats and uncertainties while supporting corporate growth goals. Tactically, supply chain management responds to problems; strategically the supply chain has embedded processes that accommodate the inevitable disruptions in the quest to deliver on time and within budget.
The Bottom Line: Implementing manufacturing safeguards by partnering with rapid manufacturing suppliers can accelerate product development while reducing market risks.
1 Kim Wagner, Eugene Foo, Hadi Zablit and Andrew Taylor. (September 26, 2013). The Most Innovative Companies 2013. www.bcgperspectives.com/content/articles/innovation_ growth_most_innovative_companies_2013_lessons_from_leaders/?chapter=2
2 Price Waterhouse Coopers. (January 20, 2015). 17th Annual Global CEO Survey. www.pwc.com/gx/en/ceo-survey/2014/key-findings/index.jhtml