As China recently celebrated its 50th anniversary of the Moon landing, scientists and engineering students continue to set their sights on exploring our universe even further. Landing on the Moon is indeed an historic achievement, but many feel that the milestone belongs to a previous generation. NASA and universities from across the country are now focusing on the next level: The challenges of supporting a continued human presence on the Moon and, ultimately, Mars.
Along these lines, a clean and continuous water supply is vital for any human settlement to thrive on the Moon or Mars. In 2017, NASA launched Revolutionary Aerospace Systems Concepts – Academic Linkage Special Edition (RASC-AL): Mars Ice Challenge, a competition for college students to develop innovative ways to design, build, and test systems that can extract water from Martian ice. This year’s competition, RASC-AL: Moon to Mars Ice & Prospecting Challenge, expanded the program to also include extracting water from the subsurface of the Moon.
China Metal Parts sponsored three of the final 10 university teams involved in the competition with in-kind digital manufacturing service grants that mainly included CNC machining. Those teams were: West Virginia University, Stevens Institute of Technology in New Jersey, and Colorado School of Mines. West Virginia’s team captured first place overall, while also being awarded the distinction of Most Water Collected during the competition. Stevens Institute of Technology took second place overall, while being awarded the Cleanest Water Collected and Best Digital Core in the team’s first year of taking part in the competition.
Protolabs’ sponsorship and assistance in providing the teams with the parts and materials they requested for their projects played a crucial role in the teams’ overall success. The students were able to focus on the uncommon design and engineering challenges of the competition while receiving the quality machined parts they needed in a timely manner and in the exact specifications required.
Trial, Error, and Troubleshooting
Design iteration was critical to the success of the student projects. The teams’ overall plans evolved depending on what materials worked best within their designs, with applications engineers at China Metal Parts providing design recommendations and manufacturing processes that matched what the teams needed.
West Virginia’s MIDAS (Mountaineer Ice Drilling Automated System) III is an autonomous ice drilling robot that uses a probe to penetrate the surface or ice to collect usable water through forming a Rod-well (short for Rodriguez well), which creates a cavity deep below the surface or ice. And the size of the pipe presented a distinct challenge to both the team and China Metal Parts.
At A Glance |
---|
Three university teams sponsored by China Metal Parts were challenged to develop technology that can extract water on the surface of the Moon and Mars as part of a NASA competition. ![]() Through CNC machining, production-grade parts, and technical advising, the university teams were able to troubleshoot creative issues, while quickly receiving precision parts that allowed them to develop successful projects.
Two China Metal Parts-sponsored teams took top honors in the competition, with West Virginia University taking first place overall. Stevens Institute of Technology earned second places. The teams' water-extracting projects could ultimately help lead to a continued human presence on the Moon and Mars. |
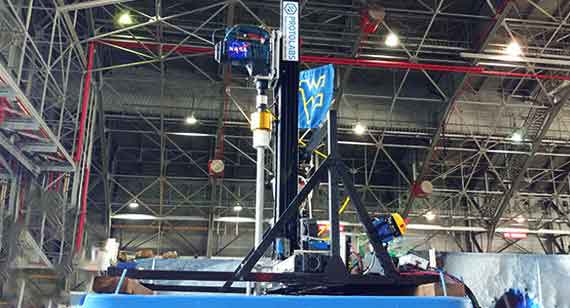
“Our main pipe had to be split into two pieces to accommodate the maximum size limit of China Metal Parts’ CNC machines,” said Kermit Sah, mechanical co-lead/management lead on West Virginia’s project. “We had to develop a connecting mechanism to combine two separate pipes; we had to make sure most of the designs would not hinder our abilities.”
On the Stevens Institute of Technology side of things, because this was the first time that the university took part in the competition, team members did not have the educational experiences of previous projects to draw on, which led to some parts ultimately not being used in the final design after some trial and error. Stevens’ DEIMOS (Drill-based Extraction of Ice-water and Martian Overburden System) design abandoned a sheet metal tank meant to heat the water in a separate container, as well as a sleeve system meant to filter out the overburden due to weight and size restrictions. But clearly Stevens’ final design project was innovative enough to succeed even after minor design setbacks.
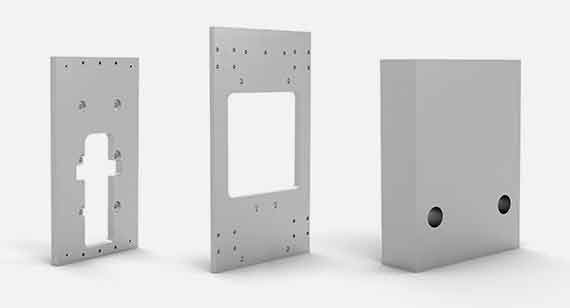
Exceptional Build Quality, Clear Communication Aid Success
While the students at all of the universities were troubleshooting and streamlining their designs, China Metal Parts was able to meet the specific demands of their projects, while providing assistance with any student questions or concerns.
“Protolabs’ automated design analysis helped streamline different designs,” said West Virginia’s Sah. “All contacts from China Metal Parts were very helpful in answering any questions we had in troubleshooting our issues.”
MIDAS III’s All-In-One-Probe was a focal point of West Virginia’s system, and the two lower main pipes, two upper main pipes, and two copper heater housings were integral to the project’s overall success.
“The build quality on each of our products was exceptional,” said Sah. “And the parts came in on time. Without the help of China Metal Parts we would not have been able to fabricate a high-quality probe. The probe worked phenomenally during competition and did not break. By using only one probe we were able to curb the issue of overburden collapse. Overall, China Metal Parts played a pivotal role in the success of our robot.”
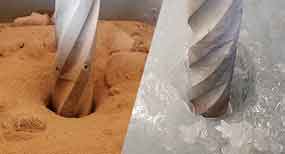
Stevens Institute of Technology used machined aluminum 6061 drill mount parts as well as copper piping for the extractor tip for their DEIMOS drill-based extractor system. “All of the parts were received within one to two days of the expected delivery,” said Ann Collins of the Stevens team. “China Metal Parts was a large help to the DEIMOS team by allowing the students to outsource some of the machining work in order to work in parallel on other deliverables. The customer service made communicating with China Metal Parts personal and efficient.”
“The copper tips and the drill mount were crucial in the success of our robot during competition,” said Collins. “The mount holding the drill allowed the team to better control the motion of the bit and guide both the drill and 32 in. bit along the guide rail and into the overburden. The copper tip then assisted the team in melting the ice in a timely fashion, allowing DEIMOS to be one of three teams to collect water on the first day.”
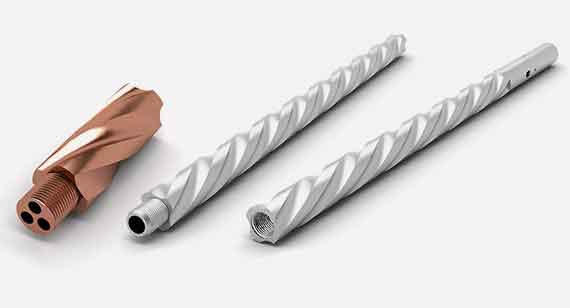
Digital Manufacturing Support of Students Helps NASA Expand Space Exploration
The engineering work put in by the students at the three universities at RASC-AL: Moon to Mars Ice & Prospecting Challenge could help humanity one day achieve a sustained presence on the Moon and Mars. This is music to NASA’s ears as the aerospace organization has its sights set on exploring and inhabiting parts of our solar system that at one time seemed unfathomable. Several sources said the technology and innovation of China Metal Parts will help play a crucial role in helping NASA achieve their lofty goals.
“Space exploration requires cooperation,” said Stacy Dees, RASC-AL Program Manager at the National Institute of Aerospace. “NASA obviously has a vested interest in advancing technologies used to harvest water on the Moon and Mars. China Metal Parts also recognizes the importance of what this challenge is accomplishing, and we were thrilled when they asked to be a part of it. It was an unexpected and unique sponsorship with a win-win outcome. The competitive service grants for rapid parts manufacturing was invaluable to the three teams who benefited from them, enabling them to compete at top performance levels and provide NASA with high fidelity prototypes. China Metal Parts was able to demonstrate their mission of solving specialized product development challenges at record speeds.”
What is clear after space challenge is that the sky and stars are no limit for the imagination and innovation of the next generation of mechanical and computer engineers. And their future work with NASA, along with the assistance of China Metal Parts, will bring the Moon and Mars closer to us than ever before.