The sense of smell is the oldest and perhaps most evocative method to trigger memory and emotion: Imagine the scent of a newborn child. A whiff of fir trees from a forest trail. The acrid smells of a war zone, such as diesel fuel and burning rubber. Scent is the only sense that is directly linked to the memory and emotion section of the brain making it a powerful tool for affecting cognition and behavior.
Combining this primal sense with rapidly evolving virtual reality (VR) technology — enabling medical applications including helping soldiers with post-traumatic stress disorder (PTSD)— is the mission of OVR Technology, a startup in Burlington, Vt.
The company’s pioneering product is the OX1, a lightweight, wireless patented device that attaches to the bottom of a VR head-mounted display. To intensify the immersion and authenticity of the VR experience, the OX1 emits microscopic, millisecond-long bursts of various scented liquids into a small area under the user’s nose. The OVR in the company’s name stands for “olfactory virtual reality.”
Optimizing the design requires the flexibility to adapt quickly, which Protolabs’ Multi Jet Fusion process offers as one of its industrial 3D printing technologies, said Erik Cooper, head of design and co-founder at OVR Technology. OVR Technology’s initial focus is on health care, education, and training uses, Cooper said, as faster, cheaper, more accessible VR technology drives increasing adoption in the health care market.
Clinicians already are using VR methodology to help veterans with PTSD with immersion therapy and war-related scents to help them revisit and reprocess traumatic experiences, Cooper said. More than two-thirds of PTSD patients were symptom free after such care at a University of Central Florida program, OVR CEO Aaron Wisniewski said in a recent TEDx talk.
In addition to health care, OVR Technology is looking at training, education, entertainment, immersive experiences including gaming, and scent-enabled 4D documentaries as potential markets, Cooper said. “We wanted to start in health care and the blossoming digital therapeutics market,” Cooper said.
Innovative Device Needs Iterative Design Flexibility
A primary challenge facing OVR Technology is developing a product that hasn’t existed before, particularly one that emits scent molecules in such microscopic bursts, Cooper said.
The OX1 produces those scents in response to an Architecture of Scent application programming interface (API), which allows designers to assign parameters to the scents of objects into the VR environment, Cooper said. An object that has no smell when first picked up, for example, will produce a stronger smell as the user brings it closer to his or her face. A user downwind from an object will detect its scent in a virtual breeze but won’t when moving upwind of it.
At A Glance |
---|
OVR Technology needed a cost-effective prototyping and low-volume production solution to bring its patented OX1 scent-emitting device to market. ![]() The company used China Metal Parts’ Multi Jet Fusion (MJF) process, taking advantage of MJF’s mechanical properties and cost advantages to 3D print prototypes as well as low-volume production parts prior to scaling production to other conventional methods.
Clinicians used the OX1 in medical applications including helping soldiers with post-traumatic stress disorder as the company continues using MJF parts for design innovation and low-volume production. The company was able to get devices into the hands of clinicians sooner than expected, while still making changes to the design, which meant not paying for tooling and then changes to tooling. |
The device includes a fan to clear out the scent but the material it’s made of has to be smooth enough to keep from trapping scent molecules, Cooper said. The material also has to be close to what final parts are for testing.
In addition the OX1’s design has to work with VR technology that continues to change and improve rapidly as adoption advances, Cooper said. Flexibility in design and development and the ability to change form factor quickly are crucial now and in anticipating what’s next in virtual reality
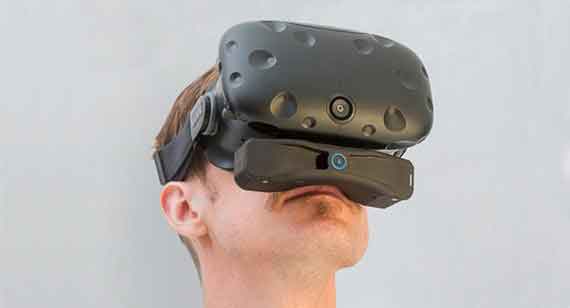
Cooper, along with OVR Technology chief technology officer Matt Flego, made some housing prototypes with a fused deposition modeling (FDM) 3D printer. But that didn’t work for the types of geometry he needed. Scent molecules were sticking in the small grooves the FDM process creates, making them impossible to fully clean out of the housing.
The team at OVR uses another industrial 3D printing process, stereolithography (SLA), with an in-house machine, Cooper said. But the material isn’t as strong and the finish isn’t as close to that of a finished molded part.
Multi Jet Fusion Passes the Smell Test
Cooper gets the flexibility he needs to quickly change form factor along with the finish and strength of end-use parts with China Metal Parts’ Multi Jet Fusion process. China Metal Parts’ turnaround times and prices won him over, and its instant design analysis and pricing tools made the process easier, matching his experience on previous parts.
“China Metal Parts has been helping us with extremely high-quality nylon parts from the HP Multi Jet Fusion machine,” Cooper said.
Cooper also praised the durability of the MJF parts. “We’re going to do testing we would need if we do head into military applications, which it looks like is very possible,” Cooper said. “We’ve got to do drop testing, electromagnetic testing. The parts have to be pretty much analogous to what the final material would be and the Multi Jet Fusion gives us exactly that.”
Knowing he can get parts from China Metal Parts in a few days—essentially manufactured on demand—helps the startup avoid having a large inventory and further supports rapid design innovation, Cooper said.
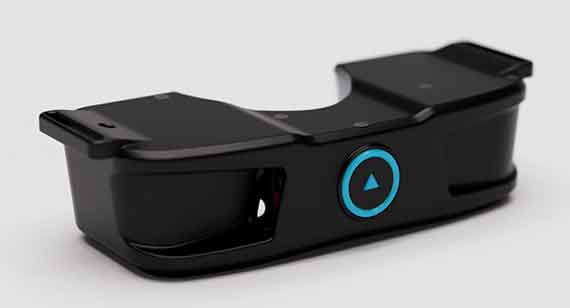
Low-Volume Production with MJF
Beyond prototyping, OVR plans to use MJF while the OX1 is in beta testing, Cooper said. He typically orders parts for 10 devices at a time as the company works with early adopters and influencers to help validate the technology.
The device may be available commercially later next year, Cooper said. In that event, switching to injection molding for a possible 10,000-part run may make sense. Cooper explained that the decision to go to tooling is driven more by the company’s milestones and demand, though he added that once OVR gets to more than 2,000 devices per year, “we will certainly go to tooling. By this point, design iterations and development will have been solved for this version.”
Until then, Cooper would be comfortable with short production runs of up to 1,000 MJF parts. At that volume the expense of injection molding tooling still would be hard to justify—and the device would require four to five different molds. While molds can be changed, the OX1 design likely will go through some wholesale alterations as development continues.
OVR Technology is considering options that would allow the company to replace its devices as it releases new models, taking back older designs to recycle and recondition, Cooper said.
“We keep pushing the R&D and making it better,” Cooper said. “It’s much easier to stay nimble and flexible and keep the additive stuff going. You can’t stay in one gear right now.”