Plastic Injection Molding
Our plastic injection molding process produces custom prototypes and end-use production parts in 15 days or less. We use aluminum molds that offer cost-efficient tooling and accelerated manufacturing cycles, and stock more than 100 different thermoplastic resins.
How Does Plastic Injection Molding Work?
The thermoplastic injection molding process at China Metal Parts is a standard process involving an aluminum mold with no heating or cooling lines running through it, which means cycle times are a bit longer. It allows our molders to monitor fill pressure, cosmetic concerns, and the basic quality of the parts.
Resin pellets are loaded into a barrel where they will eventually be melted, compressed, and injected into the mold’s runner system. Hot resin is shot into the mold cavity through the gates and the part is molded. Ejector pins facilitate removal of the part from the mold where it falls into a loading bin. When the run is complete, parts (or the initial sample run) are boxed and shipped shortly thereafter.
- Shipped in as fast as 1 day
- Molds starting at $1,495
- low-volume production
- bridge tooling
- pilot runs
- functional prototyping
Watch: Knit Lines in Molded Parts
See how knit lines in molded parts can impact overall functionality and how to reduce them.
Molding Options: Prototyping or On-demand Manufacturing?
Consider part quantities, lifetime maintenance, level of inspection, and cost when determining which option is right for injection molding.
Design Guidelines
Thermoplastic Materials
Resources
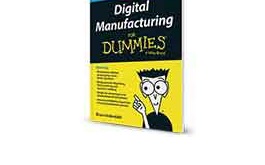
Digital Manufacturing for Dummies
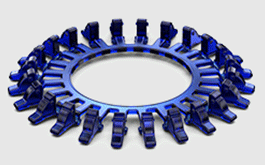
Designing for Moldability: Fundamental Elements
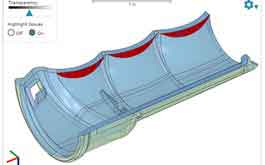
Injection Molding Sample Quote
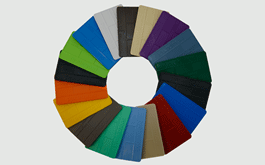
How to Choose the Right Thermoplastic
