3D-Printed Parts Help Shape Future of Health Care
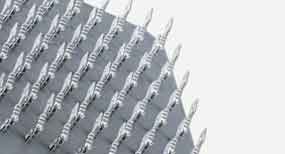
Direct metal laser sintering (DMLS) is an industrial 3D printing process that creates intricate, high-quality, fully dense metal parts. Materials that are regularly seen in medical and health care devices — like stainless steel 17-4PH and 316L as well as titanium Ti 6-4 — are available through DMLS.
This additive manufacturing process has a unique advantage over many other 3D printing processes since it produces functional, end-use metal parts. And it has advantages over traditional machining processes since surgical device development often involves very small, highly detailed components that may be impossible to manufacture by traditional means.
This includes, but not limited to, combining multiple extremely small and detailed parts into one part, which reduces the excess bulk required for assembly. A single complex part will often produce better results than an assembly of simpler components that need to work together.
Imagine the end of an arm gripper for a robotic device that stiches up a patient. These components may be smaller than 0.250 inches but are still required to possess the strength and precision required to tie knots for sutures.
Material selection and manufacturability aside, the health care industry continually strives to improve the patient experience. Keeping each procedure as minimally invasive as possible is a key element with this approach. Using DMLS technology lets surgeons minimize incisions, which, in turn, accelerates patient recovery. This not only improves the patient experience, it reduces the cost to hospitals and insurance companies.
And one of the most important attributes of DMLS? Metal parts can be prototyped within days so you can develop devices much faster and get to submissions, trials and production much quicker.
DMLS is enabling the next generation of medical devices. Don’t miss out.