3D Printing for Production Parts Gains Credibility
Why are some engineers so hesitant to use 3D printing for more than just development?
Engineers are hardwired and trained to make calculated decisions based on facts. Traditional manufacturing processes such as casting and molding have been around a very, very long time—since the Bronze Age—and time has perfected these processes and brought them to what they are today. Both industry experts and novices alike can benefit from hundreds of years of this process evolution. 3D printing processes are relatively new, especially when compared to casting or injection molding.
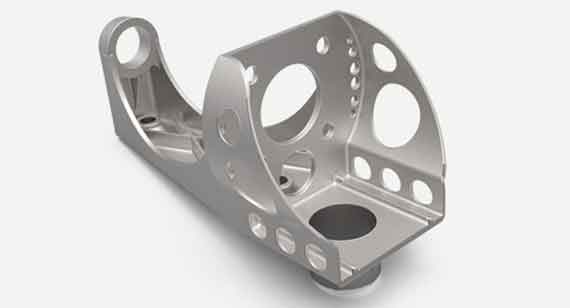
Modern, commercial-grade printing equipment and processes are capable of predictable results that will ease the mind of the most skeptical engineer. DMLS (direct metal laser sintering) can produce repeatable results for parts that can be manufactured in no other known method. China Metal Parts’ 3DP facility is not only ISO 9001:2008, but also AS 9100. This is the supplemental requirement established by the aerospace industry to satisfy DOD, NASA, and FAA quality requirements. This certification should give any engineer a sense of security.
Understanding some basic quality parameters around the processes can help to lay a foundation of credibility. For example, limits are set to the number of times base material can be used, or only virgin powder could be specified. This is no different than controlling the amount of allowable regrind into a plastic injection-molded part.
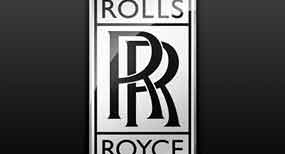
Testing parts to confirm material properties are extremely common in DMLS. Building a standard tensile bar with each build is a great way to confirm batches of production are producing the desired results. This way the first batch can have destructive testing on the tensile bar and parts to confirm the material and process are producing parts with the specified properties. The future batches can test the tensile bar for confirmation the predictable results were achieved.
The aerospace industry has been embracing advanced manufacturing methods for some time now and the automotive industry has also been making great strides in this area. For example, recent articles have been published around the Rolls-Royce Phantom’s printed parts and BMW’s leading spot in adopting printing technologies.