A Sheet Metal Materials Comparison: Galvanized vs. Galvannealed Steel
Two of the most popular forms of carbon steel for manufacturing—galvanized and galvannealed—start with the same process, but that’s where the similarities end. The difference between these two is the addition of an important manufacturing step that could affect your choice of materials for certain applications.
The Galvanizing Process
It all starts with basic steel metal, which is prone to corrosion because of its high iron content. In the galvanizing process, the steel takes a bath in an 850° F liquid zinc solution. Air knives blow off excess zinc to create the desired coating thickness. The zinc and steel form a molecular bond on the exterior which prevents and limits rust formation.
The Galvannealing Process
Galvanneal steel is galvanized steel that goes through a second process. The sheet metal is heated in a 1050° F annealing oven, which draws some of the iron into the outermost layers of the steel, creating a zinc-iron alloy. The increase in the amount of iron on the surface strengthens the material, making it less susceptible to damage. A side effect of the process is that it also improves paintability.
Galvanized vs. Galvannealed: How They Stack Up
Material | Paintability | Formability | Corrosion Resistance | Aesthetics | Cost |
---|---|---|---|---|---|
Galvanized | X | X | X | ||
Galvannealed | X | X | X | X |
Preventing and Controlling Rust
When galvanized or galvannealed metal is exposed to air, the zinc layer bonds with oxygen to form zinc oxide. If water makes contact with the zinc coating, zinc hydroxide forms. Eventually, the zinc hydroxide will react with carbon dioxide in the air and that creates zinc carbonate, which is even more stable and protective.
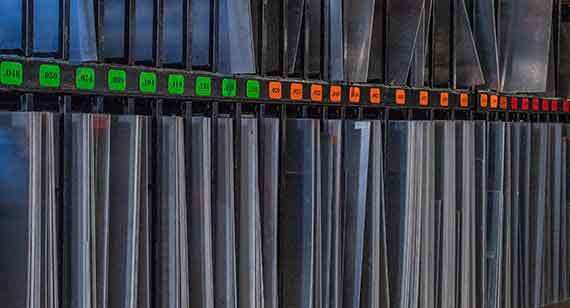
All of these zinc compounds are infinitely superior to iron-based oxides, which we know as rust. As long as the zinc coating remains intact, the steel inside is protected. Even better, if minor damage occurs, the zinc will still chemically protect the steel. Rust may form in the damaged area, but it won’t go beyond it because the water will react with the zinc first, creating a virtual fence around any damage.
Differences in Appearance and Usage
Galvanized steel is familiar to anyone who has looked closely at HVAC ducting or highway guardrails. It has a characteristic marbled pattern of light and dark gray patches called spangling.
If you’re looking for an industrial appearance on an unpainted surface, shiny galvanized steel certainly fits the bill. One thing that’s guaranteed is that no two pieces of galvanized steel ever look the same—each has its own unique, spangled pattern.
Galvannealed steel has a flat gray, slightly-matted finish. The surface is attractive. That’s a result of the annealing process, and it’s easy to paint because the zinc coating is more absorbent. It is often chosen for architectural applications and also in the auto industry.
Product Specifications
For both galvanized and galvannealed sheet metal, we use commercial grade CS-B stock. Our galvanized sheet metal is G60, and we use A40 galvanneal. The number in that code refers to the thickness of the zinc coating on the product. For example, A40 tells you that the metal contains 0.40 ounces of coating per square foot; G60 has 0.60 ounces of coating per square foot. These are ideal thicknesses for most applications and environments.
We stock a variety of galvanized and galvannealed sheet metal, ranging in thickness from 0.027 to 0.138. Our datasheets provide detailed specifications for galvanized and galvannealed sheet metal.
No matter which metal you choose, galvanized or galvannealed, you will get superior corrosion resistance. Both are easy to form, durable, and attractive in their own, unique way. What may sway you to one compared to the other is your application. If you want the metal painted, or want a more stylish metallic presentation, galvannealed will likely be your choice. If your needs are more industrial, and you like the way spangling looks, galvanized metal will save you a little money.