Advancements in Additive Tech Build Popularity within the Industry
As one of the newest and most modern manufacturing methods, the 3D printing industry is constantly changing and innovating as new engineers and inventors work to push the limits of those before. In this post we cover some groundbreaking advancements in additive manufacturing including the world's most colorful printer, fastest 3D printing method, and tallest 3D printed structure.
HP Reshapes 3D Printing Industry… Again
HP entered the 3D printing space in 2014 with the launch of its Multi Jet Fusion printer. Offering an industrial machine that was 10 times faster and 50% cheaper than systems on the market at that time drastically changed the face of additive manufacturing.
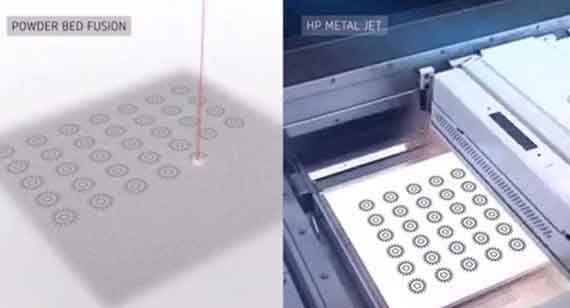
Four years later, the company again sought to transform the 3D printing landscape with its Metal Jet 3D printer. HP again promised faster build times—with its PageWide technology moving a band of print heads across the entire bed in one swipe per layer, rather than one print head moving back and forth over and over again—and lower costs since it creates its own parts.
So, what exactly is Metal Jet Fusion? The process starts with a thin layer of powdered metal spread on the bed, followed by a line of print heads traveling over the metal powder layer squirting drops of a binding agent. This process is followed layer by layer, laying the powder followed by the binder over and over again, until the intended piece is built from the bottom up. In this process, building an approximately 1-square-foot object takes four to five hours to complete. After the build, the part is removed from the powder bed, de-caked, and sintered to form a final, solid piece.
With six print heads and four nozzles printing the binding agent, the company boasts unmatched precision, reliability, and repeatability in industrial metal 3D printing. It also states that its newest process produces more isotropic green structure and a more uniform part compared to traditional powder bed fusion, resulting in the capability to build more complex parts faster.
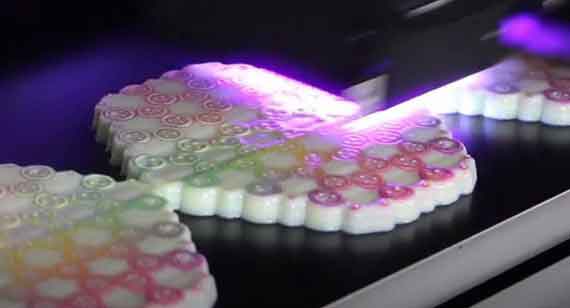
Mimaki Colors the Face of Plastics Printing Technology
Mimaki, a primarily wide-format inkjet printer manufacturer out of Japan, recently unveiled the world's first 3D printer with more than 10 million colors and UV-curable inkjet printing. The 3DUJ-553 offers photorealistic color accuracy based on the technology Mimaki developed for its 2D inkjet printers.
The company says the rich color expression is best suited for creating final product of which extra coloring is difficult after completing the build, and it plans to build a new business system around the new printer. Examples of applications include sign graphics, with the ability to effectively create realistic 3D motifs and 2D images, and industrial products with its ability to produce full color and fine modeling down to minute details.
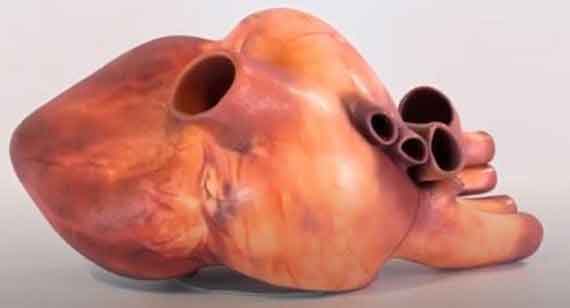
The 3D printer works like a standard inkjet printer, applying a layer of ink to the build surface, which is then coated with a UV-sensitive ink and solidified using LED light. This process is repeated layer after layer to form a multi-color object. The true innovation comes in the system’s inkjet technology, enabling the color profiles, and even transparency, that the printer can achieve.
From Zero to Fully-Formed Piece in 30 Seconds Flat
From ultra-colorful to ultra-fast, a groundbreaking additive technology recently developed by engineers at Ecole Polytechnique Fédérale de Lausanne in Switzerland can build a piece up to two cm in size, in as fast as 30 seconds. Contrary to standard 3D printing methods that build parts layer by layer, in what is usually a time-extensive process, the new, high-precision method builds parts by beaming a laser into a container of translucent gel, hardening the liquid through polymerization.
"It’s all about the light," said Paul Delrot, CTO of Readily3D, the company set up to develop and market the system. "The laser hardens the liquid through a process of polymerization. Depending on what we're building, we use algorithms to calculate exactly where we need to aim the beams, from what angles, and at what dose."
The team envisions a wide range of uses, but says it could be particularly well-suited for biomedical applications like 3D-printed tissue, organs, and hearing aids. Researchers believe its advantages over existing methods may assist medical experts, as it can be used to quickly build small silicone or acrylic parts that don't need post-process finishing. It can also be used to build parts inside sealed, sterile containers, preventing contamination.
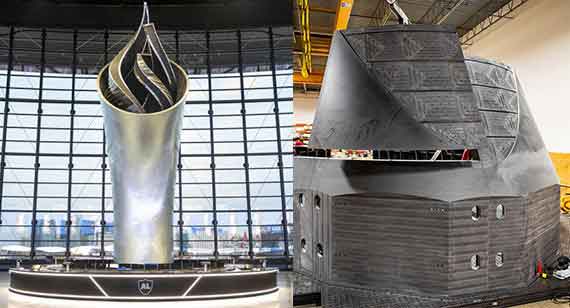
World's Tallest 3D-printed Structure Unveiled
Rounding out our list of additive manufacturing innovations, the Las Vegas Raiders and Dimensional Innovations recently unveiled the world's tallest 3D-printed object. Measuring 93 feet tall and using more than 100,000 pounds of raw material, the Al Davis Memorial Torch is comprised of 225 3D printed blocks weighing around 350 pounds each.
Kansas-based sign design and fabrication firm, Dimensional Innovations, 3D printed the blocks using a carbon fiber-reinforced polycarbonate composite. The blocks making up the torch itself were printed on the large-scale LSAM system, then machined to achieve tight tolerances, and robotically painted for a reflective sheen. The bottom of the torch was routed through CNC machining after the build to create a 21st century woodgrain pattern, and then clear coated. The entire project took around 50,000 hours to develop, manufacture, and install.
"Our team has worked relentlessly over the past year to develop, print, fabricate, test and install the memorial torch to ensure it conveys the symbolic flame that burns brightest in the Raiders organization," said Tucker Trotter, CEO of Dimensional Innovations. "The enormity of the torch, both physically and ideologically, will carry on the memory of Mr. Davis for years to come and we’re proud to have played a part in that."
The commemorative structure was unveiled at the Raider’s first home game on Sept. 21 in the new Allegiant Stadium's lobby in Paradise, Nevada.
Eye on Innovation is a monthly look at new technology, products, and trends.