Approved Molding Samples and Our Red Bag Process
There are many variables that go into manufacturing a quality injection-molded part. It starts with creating a moldable design, so considerations like maintaining uniform wall thickness to prevent sink, designing in radii to help material flow, adding draft so the part ejects properly, and many other factors will all influence the quality of the final plastic part. Using our automated quoting software that analyzes manufacturability greatly simplifies and accelerates this step.
Next it’s up to the molder to dial in the proper parameters on the press like temperature, fill speed, and pressure to get the highest quality part. We also have several robust processes in place so that customers’ parts are consistent from run to run and we reliably deliver parts that meet our workmanship standards.
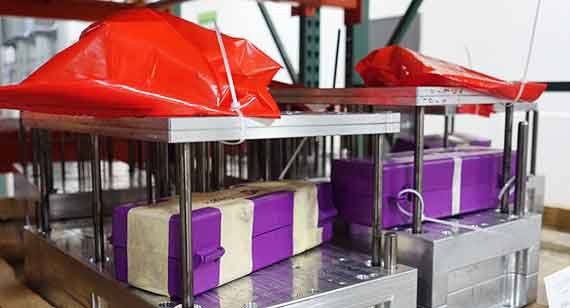
Approved Samples and the Red Bag
Maintaining quality and consistency during injection molding is critical since the process is typically used for at least thousands–sometimes millions—of parts. One small defect can have large consequences. Further, most projects can last for several years, so we must store and inventory each of our customers’ tools for the duration of their usage—parts from the third, fourth, and fifth run need to be consistent with those produced on the first run. That’s where our sampling process comes in and what we call the red bag.
If a tool is intended for low-volume production, we first conduct a sample run, usually around a hundred or so parts, and send these parts to the customer for approval. This mitigates any risk before moving to higher volumes and gives us an opportunity to address any quality issues if they arise.
We retain the approved samples from the mold by storing them in a red bag. It’s our variation of the common golden sample method as the red bag contains the ideal parts produced by the mold. The red bag then stays with the mold in storage, so that when a customer comes back to order more parts off that same tool, the press operator has an approved sample to reference when dialing in molding parameters. The red bag also includes information like mold number, order number, order quantity, material used, and other details to improve traceability of each order that passes through our production facility.
Additional Injection Molding Process Controls
For an added level of assurance we also keep parts from the most recent run in clear bags, which, like the red bag, are stored with the tool. To make sure clear-bag parts and red-bag parts aren’t accidentally swapped, red-bag parts are marked with yellow paint. Having samples from both the initial run and the most recent run of parts helps us quickly identify and address any issues that may arise during production.
At the facility where we conduct sample injection molding runs, we also have bins, one for each day of the month, containing parts from every mold created throughout the month. This makes it easy when a customer reaches out to us with any concerns with their part. A member of our quality control team can easily look up when that customer’s parts were molded, walk out to the production floor, and go to the bin with the corresponding date, and pull the part to inspect.
Press operators will also periodically sample parts during the molding process to make sure dimensions are within tolerance and match the red bag samples. In-process dimensional quality inspections are recorded electronically and can easily be referenced. Additionally, visual inspections are done during production to make sure parts conform to our workmanship standards.