Manufacturing Workmanship Standards: Amount of Flash Acceptable at Parting Lines
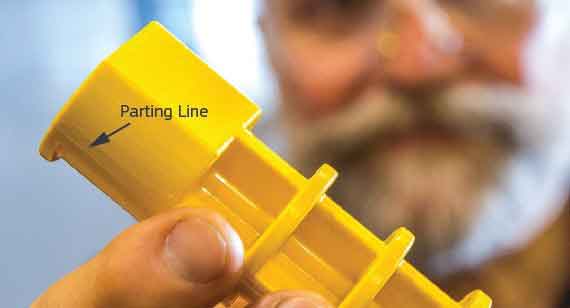
Flash—excess plastic that can form at parting lines or other shut-off areas along the part—is an unfortunate reality during injection molding, but it can be mitigated.
To understand how flash occurs, let’s quickly review the molding process. Injection molding starts by clamping two mold halves together under immense pressure. Then, pelletized plastic is poured in, heated up, and turned into molten plastic as it flows into the cavity between the two mold halves. The molten plastic cools down and is ejected from the mold, resulting in the final part. Along the outside of the part, where the two mold halves meet, is the parting line. At the parting line is where flash can occur.
Our workmanship standards allow for no more than 0.005 in. of flash on a molded part. For reference, that’s about the thickness of a sheet of printer paper. While some thermoplastics—the ones that flow better—are more likely to flash, like Santoprene, nylon, HDPE, and polypropylene, all materials will flash eventually as a mold is used for subsequent runs of parts and the tool is worn out. For example, while glass-filled nylon doesn’t flow particularly well, it’s abrasive enough to wear out the mold and begin flashing after several orders.
Since liquid silicone rubber (LSR) flows especially well, in fact it will flow through an area less than 0.001 in., we take special precautions when producing the mold. Along the parting line we mill a channel for excess material to flow. This creates what we call a tear strip around the part’s parting line. Once a part is molded and removed from the tool, a technician will either tear or trim the excess material until it’s in accordance with our <0.005 in. standard.
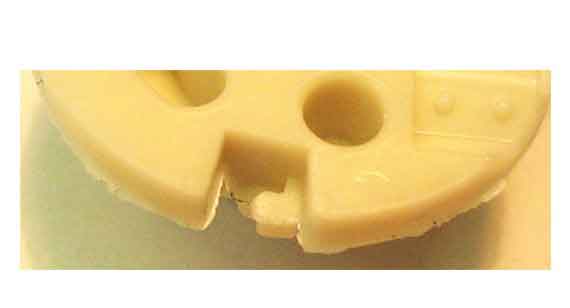
We do have controls in place to help mitigate flash before production starts. First, the design analysis included in our interactive quotes will show you where the parting line on your part will be. If our analysis software finds that flash could be an issue, the parting line will be highlighted as a recommended change and we’ll have a conversation from there and explore any design changes to reduce flash.
Additionally, if a part requires exceptionally steep shut-offs, we’ll mill the tool and send it over to our electronic discharge machining (EDM) equipment for a final touchup before it goes to the molding presses. This helps ensure the mold closes as flush as possible.
During the injection molding process, our technicians will sample and inspect parts periodically to confirm that they meet our cosmetic standards, including checking for flash. If flash starts to exceed our 0.005 in. requirement, we’ll first remedy the issue by trimming back the excess material. If flash becomes so problematic that trimming is no longer efficient, we will make a new mold—assuming that this is an on-demand manufacturing mold or a prototyping tool that has yet to reach our 2,000 part guarantee.
The best way to avoid flash and conceal your parting line is orienting the part so that the parting line is along a sharp edge. This isn’t always possible for more complex designs, but with most CAD software packages you can identify and experiment with parting line to find the optimal location. Check out this design tip for more guidance on parting lines.