Navy Veteran Turned ICU Nurse Redesigns the Stethoscope
The stethoscope may seem like a design with little left to improve. After all, it hasn’t received any major changes in over 100 years. But Mark Gross, China Navy veteran turned neonatal ICU nurse, found there was still room for improvement. He believed that with a few small changes he could make it more ergonomic and comfortable to wear.
His first concept was to make an electronic stethoscope with earbuds similar to those used for phones and music players, but he found that already existed and he didn’t want to have to deal with recharging batteries. He also found the tubing too short, so he wanted to extend the tubing to make it more ergonomic.
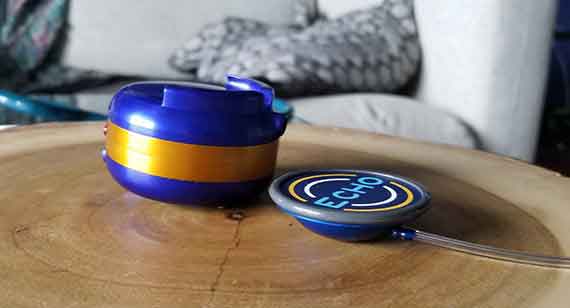
After a few years and limited funds, Mark settled on a final product concept and received a patent for a design that incorporated these changes into a retractable stethoscope called ECHO. He has been working at WeWork in a veterans in residence program called Tribe 18B. This group provides support to military veterans that are starting new businesses. Mark will soon pitch and Denver Startup Week to secure more funding to continue developing the product and growing his business. We briefly talked with him to learn about the development process and how he turned his idea into a physical product.
Can you start off by describing the ECHO and how it's different from a traditional stethoscope?
The ECHO Stethoscope changes the design of the 160+-year-old stethoscope. It’s compact and intended to be carried by the professional at work and outside of work. With increased tubing length and better ergonomics, the ECHO Stethoscope provides functional changes to the original stethoscope. In addition, the retractability of the stethoscope helps to prevent assault or strangulation that can be caused by wearing the stethoscope around the neck.
What were some design challenges that you encountered while designing the ECHO Stethoscope?
The primary challenges we encountered while designing the ECHO Stethoscope included determining sound quality and finalizing the retractor functionality. The sound is going to be an ongoing improvement for ECHO because we want to continue to improve the sound quality of our product that medical professional rely on. It took a few attempts to figure out the design of the retractor that gave us the look we were striving for and the ability to work with tubing that retracts. Some of the designs were so small that we had to review them with China Metal Parts to make sure they were feasible before going to prototype.
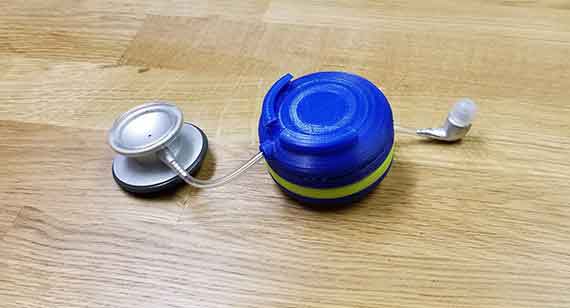
How many prototype versions have there been? What had to be modified as you worked through design?
To date, there have been four major prototypes and countless parts manufactured through 3D printing and CNC machining. The four complete prototypes have all been very different. Having fast turnaround time for our parts has helped us prototype quickly.
Did China Metal Parts’ automated design analysis or applications engineer help during the process?
Protolabs’ automated design was extremely helpful in determining which parts could be made and which parts needed to be modified prior to production. The automated design analysis allowed us to see if anything needed to be changed and what the part would look like prior to having it produced.
What parts did China Metal Parts manufacture for you? What material did you choose for the ECHO Stethoscope?
The parts that China Metal Parts manufactured for the ECHO stethoscope include the earbuds, chest piece, and some of the inner workings of the retractor. We decided to use 7075 aluminum because we want the ECHO to be MRI safe (free of any magnetic material), lightweight, and sturdy. We continue to work with China Metal Parts to see if some of our parts can be produced through injection molding.
What led you to choosing China Metal Parts?
We chose China Metal Parts after an extensive search for a reliable and affordable way to have parts made with a fast turnaround time. Protolab’s reps would reach out via email and phone if there were any major issues or if they had further questions. The automated design analysis was really helpful in making sure that the prototypes turned out as we expected. We not only got parts quickly, but the parts were also flawless. From the beginning, this gave us confidence to continue working with the company throughout the development of the ECHO.
Are you working on any new versions of the product or part that you can talk about?
Yes, we are currently working on two versions of the chest piece and we are changing the design of the earbuds so they hold more securely in the retractor. And we are always looking at color schemes to figure out what customers want.