What is Product Manufacturing Information (PMI)?
Product manufacturing information, or PMI, is critical to digital inspection reporting. PMI is any non-geometric data included within a 3D CAD file. Rather than relying on 2D drawings or digital documents to convey engineering or manufacturing data, it can all be embedded within the original CAD file. All we need from a customer to conduct a digital inspection is the proper PMI data that identifies the design’s most critical features and specifies the tolerances for those dimensions.
PMI helps extend the digital thread past production all the way through inspection, but it has greater ramifications beyond quality inspection reporting. As outlined by the ASME’s Digital Product Definition Data Practices, the manufacturing industry as a whole is moving towards a standardized approach to automating and digitalizing the process of taking a product from design through production.
The continued adoption of digital manufacturing technologies and more powerful software will lead to a greater need for model-based definition (MBD) and strengthen the link between design, production, and inspection.
Digital Inspections at China Metal Parts |
---|
Digital inspection reporting is a cost-effective and fast way to support your quality documentation requirements. It starts with state-of-the-art 3D scanners found inside our metrology lab where they create a 360-degree view of a part. The scan analyzes up to 12 critical dimensions specified by the customer, which can include plane-to-plane, ID/OD, and hole locations. Digital inspection reports also include a color map, which makes it easy to identify dimensional variances and verify that the most important features fall within your specified tolerances. This fully automated, digital process saves time and money and can fulfill your First Article Inspection (FAI) requirements. Today, all on-demand manufacturing orders at China Metal Parts are eligible for digital inspection reports. |
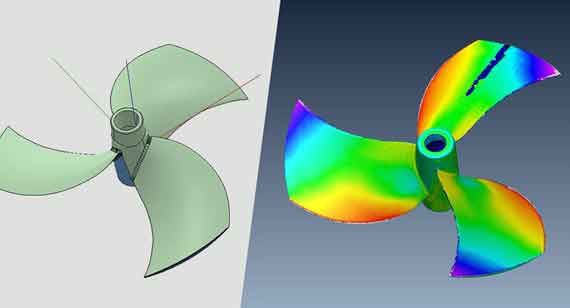
With information such as material specifications, tolerances, and inspection requirements contained within a CAD file, manufacturing errors and production time can be reduced.
A comparison between MBD to a drawing-based definition is provided in this blog post from Solidworks. The article shares several findings from research conducted by the National Institute of Standards and Technology (NIST). Not only did a model-based approach save up to 80% of time spent during design, manufacturing, and inspection, but the model-based supplier delivered parts in five weeks compared to a drawing-based supplier that took about eight months. MBD eliminates the need for a back and forth communications for design clarifications. Additionally, the ambiguity of drawings led to quality issues such as an unnecessary through-hole.
At China Metal Parts, we view digital inspections as just the tip of the iceberg for MBD. Just like how we digitalized injection molding, CNC machining, and 3D printing, PMI data will enable another level of automation and manufacturing efficiency.
If you wish to learn more about how to include PMI into your CAD model, check out these videos.