You already know that CNC machining at China Metal Parts is different from traditional manufacturing. Our process is fully automated—from CAD analysis to auto-toolpathing and digital inspections—we do it all really fast. This automation is what enables our speed and now you can take advantage of that speed when you're ready to move to higher volume production or simply need more than 15 prototypes.
Machining also works well for jigs, tools, fixtures, and other low-volume parts, and allows flexibility and affordability with part production.
This tip covers the ins and outs of our higher-volume machining capabilities, including pricing, lead times, finishing options, and more.
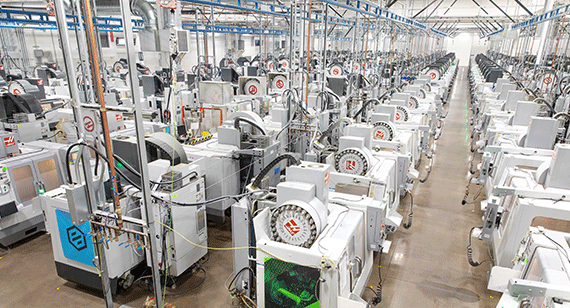
Machining for Higher-Volume Needs Emerges
At China Metal Parts, we saw a way to fill that production-quantity gap, and also solve the upfront- and warehousing-cost issues. Our massive machining capacity—with nearly 500 CNC machines—which can mill or turn parts in as fast as a day for rapid prototyping, could also be used for low-volume, end-use part production—this brings down machining costs without adding to lead time.
The nominal “break point,” that is, a price-break point between quick-turn prototyping machining and production machining is about 15 parts. Production machining also helps assure part quality with FAI reporting, Certificate of Compliance (CoC) documentation, and certifications such as ISO 9001 and AS9100.
Production machining doesn’t offer the same economies of scale as molding or casting processes—especially at high-volume levels (think tens of thousands or millions). However, as machined production volume increases, cost per part does also go down (think low-volume runs of dozens to a few thousand). Production machining also solves warehousing and inventory issues, providing supply chain flexibility by producing parts on-demand. Indeed, in many cases, our customers find our machining service now allows them to use a single-source supplier from concept validation to short-run production.
Machining for Production Provides Supply Chain Flexibility
Plenty of machine shops out there can produce machined parts. We have several key advantages, particularly when you need production volumes of parts relatively quickly, or even varying quantities of parts. With our capacity, we can produce higher volumes of parts faster than other shops. Our end-to-end process begins with design analysis and quotes. Upload a CAD model to get your free analysis and quote within hours. If you need prototypes, request a quick-turn quote and get finished parts in as fast as one day. When ready for a higher volume of production parts, request a production quote and get parts in as few as five days. Our capacity, plus our large stock of materials, allows this speedy turnaround. The entire production process, from toolpath development to machining to finishing, is handled in-house for maximum speed, quality, and process control.
Related to flexible quantities, leveraging machining eliminates the high initial costs of mold or die production. Once the toolpath has been developed, you can order machined parts in lots as small as 15 pieces. On the other hand, if your ultimate production volume will be high enough to justify molding or casting, you can use machining for bridge production and take your product to market while you wait for production molds or dies to be made.
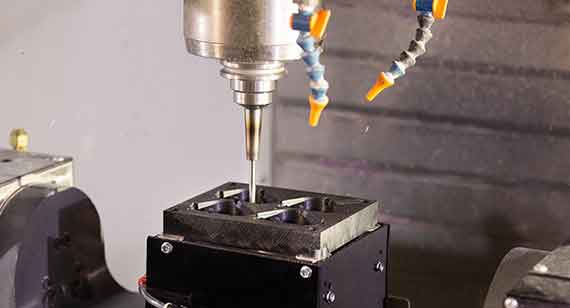
Production Machining of Plastics
At volumes of a thousand or fewer, machining plastics can be less expensive than injection molding. In addition, machining can produce parts that would be difficult to mold. These can include parts with uneven wall thicknesses or with wall thicknesses over 0.150 in. (3.81mm), often needed for parts used as fixtures or wear plates.
The overall speed advantage of machining versus injection molding at modest production volumes increases as parts increase in size. In addition, machining plastic eliminates the risks of sink, warp, and knit lines that can occur in molded parts, and machined parts don’t require draft as injection-molded parts do.
In some cases, engineers might consider 3D printing for these production volumes, but the fact that machined parts are cut from solid billet gives them several advantages over 3D-printed parts. Because they aren’t layered, machined parts may have greater physical integrity than printed parts have. They can be cut from materials that cannot be used by 3D printers, and they can be machined to smoother finishes than printed parts.
Plastic production materials for machining at China Metal Parts include ABS, Acetal, Acetal Copolymer, PEEK, and PEI:
Plastic Materials | Maximum Part Size |
---|---|
ABS | 7 in. x 15 in. x 1.75 in. |
Acetal (black, white) | 7 in. x 15 in. x 1.75 in. |
Acetal Copolymer (black, natural) | 7 in. x 15 in. x 1.75 in. |
PEEK (black, natural) | 7 in. x 15 in. x 1.75 in. |
PEI (Ultem) | 7 in. x 15 in. x 1.75 in. |
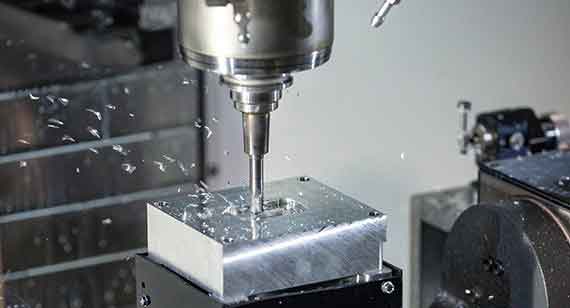
Production Machining of Metal
At low- to medium-production volumes, machining of end-use metal parts offers significant advantages over die casting. As with plastics, at appropriate volumes, machining is faster and less expensive than casting.
While machining can begin turning out parts immediately, die casting requires the production of hardened steel tooling, which is a slow and costly process.
There are more metals that can be machined than can be die cast. And die casting leaves a rough surface like that found on cast iron cookware. Such surfaces can be smoothed by machining, but this is a time-consuming secondary process.
Die casting also does not produce as solid a finished product as the billet stock used in machining. Die cast metal can be porous, brittle, and subject to elongation. For these reasons, machining may still be preferable to casting even when casting has a cost advantage.
Metal production materials at China Metal Parts (see our Materials Comparison Guide for a complete list) include Aluminum 6061, Aluminum 7075, Steel 1018, and Steel 4140:
Metal Materials | Maximum Part Size |
---|---|
Aluminum 6061 | 7 in. x 15 in. x 3 in./15 in. x 18 in. x 1.75 in. |
Aluminum 7075 | 7 in. x 15 in. x 3 in./15 in. x 18 in. x 1.75 in. |
Steel 1018 | 7 in. x 15 in. x 1.75 in. |
Steel 4140 | 7 in. x 15 in. x 1.75 in. |
Metal Finishing Options: Anodizing and Chromate Plating
Once parts have been machined, we can complete the production process with a variety of finishing options depending on the metal. These include:
- Type II, ROHS compliant, Class 1 (clear), and Class 2 (black) anodizing
- Type I, Type II, Class 1A and Class 3 chromate plating
Anodizing and chromate plating are common finishing options and effective ways to protect machined metal parts from corrosion. These processes can also enhance the overall appearance of metal parts.
Our anodizing processes are RoHS compliant, meaning that the materials we use are environmentally friendly, and have very little, if any: mercury, lead, cadmium, hexavalent chromium, PBBs, or PBDEs. Chromate plating differs from anodizing. No metal is added to create the protective layer. Instead, plating is a conversion coating, which changes the character of the metal surface. Again, both options offer excellent corrosion protection.
Threading Options for Machining
Our CNC machining service can also add threaded features to milled and turned parts. Threads are specified within our automated interactive quotes. We offer a selection of UNC, UNF, NPT, MC, UNC STI, and UNF STI options in standard, taper pipe, metric, and standard helicoil threads. See the Threading Options table on our production machining page. On both milled and turned parts, threaded holes must be modeled at the proper diameter, however, threading options differ for milled and turned parts. Our Threaded Holes Guidelines page offers more details, including a maximum-reach table.
Additional Consulting Help on Design
Finally, it should be noted that, for critical features on your production parts, we can accept 2D drawings. Just consult with one of our applications engineers at +86-755-27311095 or at [email protected]. You can find more information on our CNC production capabilities by checking out CNC machining for production parts. Also, see the sidebar on this page for additional design resources. To get your next machining project started today, just upload a 3D CAD model for an interactive quote within hours.
Design Resources |
---|
More details on our CNC machining capabilities can be found on our website: Design Guidelines: CNC Milling Design Guidelines: CNC Turning These include design considerations to help improve part manufacturability, enhance cosmetic appearance, and reduce overall production time. Find more details about our CNC machining service’s threading options for milled and turned parts. CNC Machining Surface Finish Guide Get a realistic snapshot of the surface finishes that are possible on machined plastic and metal parts. Design Essentials for CNC Machining This guide has compiled some of our best design tips to help you optimize your part design for machining. |